государственное автономное профессиональное образовательное учреждение
Челябинской области «Политехнический колледж»
(ГАПОУ ЧО ПК)
Комплект контрольно – оценочных средств
для промежуточной аттестации по дисциплине
ОП.05 Основы металлургического производства
индекс и наименование
основной профессиональной образовательной программы (ОПОП)
по специальности СПО
22.02.01 «Металлургия черных металлов»
код и наименование
(программа подготовки специалистов среднего звена)
(программа базовой подготовки)
(на базе основного общего образования)
2 курс 3 семестр
Магнитогорск, 2016
СОГЛАСОВАНО на заседании предметной (цикловой) комиссии «Технологии материалов» (название ПЦК) Протокол № 2 от «20» сентября 2016 г. Руководитель ПЦК /И.М. Курлова/ ![]() (подпись) (Ф.И.О.) | УТВЕРЖДАЮ Заместитель директора по учебной работе ГАПОУ ЧО ПК «22» сентября 2016 г. / О.В.Разина / ![]() (подпись) (Ф.И.О.) |
СОГЛАСОВАНО на заседании предметной (цикловой) комиссии «Технологии материалов» (название ПЦК) Протокол № от « » 201 г. Руководитель ПЦК / / ![]() (подпись) (Ф.И.О.) | УТВЕРЖДАЮ Заместитель директора по учебной работе ГАПОУ ЧО ПК « » 201 г. / / (подпись) (Ф.И.О.) |
Комплект контрольно-оценочных средств для промежуточной аттестации
по дисциплине ОП.05 Основы металлургического производств
индекс и наименование модуля
Разработан в соответствии со следующими нормативными документами и локальными актами:
1) Федеральным государственным стандартом по специальности/профессии среднего профессионального образования 22.02.01 Металлургия черных металлов (утверждён Минобразования России утв. от 03 июля 2013 г. рег. № 4);
2) Положением «Об организации и проведении текущего контроля успеваемости и промежуточной аттестации студентов ГАПОУ ЧО «Политехнический колледж» (утв.29.12.2015г.)
3) Учебным планом Колледжа (утв. 01.09.2015 г );
4) Рабочей программой учебной дисциплины ОП.05 Основы металлургического производства (утв. 30.06.16г.)
Проводится в форме дифференцированного зачета
Разработчик:
__________________ /С. А. Байченко/
(подпись) ( И. О. Фамилия)
1 | ПАСПОРТ КОМПЛЕКТА КОНТРОЛЬНО-ОЦЕНОЧНЫХ СРЕДСТВ | 4 |
| 1.1 | Область применения комплекта контрольно-оценочных средств | 4 |
| 1.2 | Система контроля и оценки освоения программы учебной дисциплины в рамках промежуточной аттестации | 5 |
| | 1.2.1 | Формы промежуточной аттестации | 5 |
| | 1.2.2 | Характеристика заданий для промежуточной аттестации и их оценивание | 5 |
2 | КОНТРОЛЬНО-ОЦЕНОЧНЫЕ ЗАДАНИЯ С ЭТАЛОНАМИ ОТВЕТОВ ДЛЯ ПРОМЕЖУТОЧНОЙ АТТЕСТАЦИИ ПО УЧЕБНОЙ ДИСЦИПЛИНЕ | 7 |
4 | ИНФОРМАЦИОННОЕ ОБЕСПЕЧЕНИЕ | 29 |
1. ПАСПОРТ КОМПЛЕКТА КОНТРОЛЬНО-ОЦЕНОЧНЫХ СРЕДСТВ
1.1 Область применения комплекта контрольно-оценочных средств
Комплект контрольно-оценочных средств предназначен для проверки результатов освоения учебной дисциплин
ОП.05 Основы металлургического производства
(индекс и наименование дисциплины)
основной профессиональной образовательной программы по специальности СПО
22.02.01 Металлургия черных металлов
(код и наименование специальности/профессии)
Комплект контрольно-оценочных средств для проведения промежуточного контроля позволяет оценивать:
Освоение профессиональных компетенций (ПК), соответствующих виду профессиональной деятельности, и элементов общих компетенций (ОК):
Таблица 1
Код | Наименование результата обучения |
ПК 1.1 | Осуществлять технологические операции по производству черных металлов |
ПК 1.2 | Использовать системы автоматического управления технологическим процессом |
ПК 1.3 | Эксплуатировать технологическое и подъемно-транспортное оборудование, обеспечивающее процесс производства черных металлов |
ПК 1.4 | Анализировать качество сырья и готовой продукции |
ПК 2.1 | Планировать и организовывать собственную деятельность, работу подразделения, смены, участка, бригады, коллектива исполнителей. |
ПК 3.1 | Принимать участие в разработке новых технологий и технологических процессов. |
ПК 3.2 | Участвовать в обеспечении и оценке экономической эффективности. |
Таблица 2
ОК 1 | Понимать сущность и социальную значимость своей будущей профессии, проявлять к ней устойчивый интерес |
ОК 2 | Организовывать собственную деятельность, определять методы и способы выполнения профессиональных задач, оценивать их эффективность и качество |
ОК 3 | Решать проблемы, оценивать риски и принимать решения в нестандартных ситуациях |
ОК 4 | Осуществлять поиск, анализ и оценку информации, необходимой для постановки и решения профессиональных задач, профессионального и личностного развития |
ОК 5 | Использовать информационно-коммуникационные технологии для совершенствования профессиональной деятельности |
ОК 6 | Работать в коллективе и команде, обеспечивать ее сплочение, эффективно общаться с коллегами, руководством, потребителями |
ОК 8 | Самостоятельно определять задачи профессионального и личностного развития, заниматься самообразованием, осознанно планировать повышение квалификации |
Таблица 3
| Освоение умений и усвоение знаний: | Задания №№ |
| В результате освоения дисциплины студент должен знать: | |
З1 | теплотехнические основы металлургических процессов | 1-9 |
| В результате освоения дисциплины студент должен уметь: | |
У1 | производить расчеты основных параметров металлургического производства; | 10-35 |
1.2 Система контроля и оценки освоения программы учебной дисциплины в рамках промежуточной аттестации.
1.2.1 Формы промежуточной аттестации
Таблица 4
Семестр | Формы промежуточной аттестации |
3 | Дифференцированный зачет |
1.2.2 Характеристика заданий для промежуточной аттестации и их оценивание
Комплект контрольно-оценочных средств для проведения промежуточного контроля содержит 35 заданий. Материалы составлены на основе рабочей программы дисциплины и охватывают разделы и темы, изучаемые на 2 курсе в 3 семестре в объёме 106 часов (71 ч. аудиторных занятий, 35 ч. самостоятельной работы студентов).
Контрольно - оценочные материалы состоят из двух частей (часть А,В).
Часть А (задания 1 – 9) содержит теоретические задания, составлены с учетом профессионально значимой информации, направленной на формирование профессиональных и общих компетенций по дисциплине, в которых необходимо полно и верно раскрыть основное содержание вопроса, соблюдать логическую последовательность теплотехнического металлургического процесса.
Часть Б (задания 10 – 35) содержит задания, в которых необходимо уметь рассчитывать основные параметры металлургического производства
Контрольно-измерительные материалы ориентированы на комбинированную форму проведения, которая включает выполнение двух типов задания: теоретический вопрос и два практического задания.
Задания целостно отражают объём проверяемых умений, знаний и навыков в рамках дисциплины. Задания, представленные в вариантах, одинакового уровня сложности
Время, отводимое на выполнение заданий, составляет не более двух академических часов(90 минут).
Оценивание качества ответов экзаменуемых производится по следующим критериям:
Оценивание качества выполнения теоретического задания:
Оценка «отлично» выставляется в том случае, когда в ответе полно и верно раскрыто основное содержание теоретического вопроса, соблюдена логическая последовательность теплотехнического металлургического процесса.
Оценка «хорошо» выставляется в том случае, когда в ответе содержится верное освещение темы вопроса, но отсутствует полнота его раскрытия; соблюдена логика изложения, но отдельные положения ответа содержат лишь общие рассуждения, не проявляет достаточно уверенного и полного владения этими знаниями, допускает отдельные незначительные ошибки.
Оценка «удовлетворительно» выставляется в том случае, когда в ответе приведены отдельные несистематизированные положения, имеющиеся рассуждения, направленные на получение ответа на вопрос задания, не доведены до конца и не приводят к верному ответу. А так же когда студент проявляет слабое освоение требуемого знания по теплотехническим металлургическим процессам
Оценка «неудовлетворительно» выставляется в том случае, когда студент имеет разносторонние, бессистемные знания, не умеет определять главное и второстепенное, допускает ошибки в определении понятий, искажающих смысл, беспорядочно и неуверенно излагает материал, не может применить знания для ответа теплотехнического металлургического процесса
Рекомендации по оцениванию выполнения практического задания:
Оценка «отлично» выставляется в том случае, когда студент показывает освоение необходимых для выполнения практического задания, умений производить расчеты основных параметров металлургического производства
Оценка «хорошо» выставляется в том случае, когда в ответе содержится верное освещение сути задания, но отсутствует полнота его раскрытия, показывает владение требуемым умением, но допускает незначительные ошибки.
Оценка «удовлетворительно» выставляется в том случае, когда в ответе приведены отдельные не систематизированные положения, отсутствует конкретизация, или частично приведены отдельные конкретные факты, но демонстрирует верное понимание отдельных элементов умения.
Оценка «неудовлетворительно» выставляется в том случае, когда студент демонстрирует низкий уровень освоения учебной программы, в ответе отсутствует логика изложения, ответ не обоснован аргументами.
Оценка по дисциплине за дифференцированный зачет является определяющей независимо от полученных в семестрах оценок текущего контроля.
При оценке усвоения дисциплины ОП.05 «Основа металлургического производства» используется четырёх бальная система: 5(отлично), 4(хорошо), 3(удовлетворительно), 2(неудовлетворительно). За ответ на вариант дифференцированного зачета выставляются три оценки. За каждое задание в варианте и оценка выставляется как среднее арифметическое число, которое выставляется целым числом с правилами математического округления.
2. КОНТРОЛЬНО-ОЦЕНОЧНЫЕ ЗАДАНИЯ С ЭТАЛОНАМИ ОТВЕТОВ ДЛЯ ПРОМЕЖУТОЧНОЙ АТТЕСТАЦИИ ПО УЧЕБНОЙ ДИСЦИПЛИНЕ
Часть А
Проверяемые результаты обучения:
Задание 1.
Проверяемые результаты обучения: З1
Текст задания: Описать тепловой процесс при производстве кокса в камерах коксования
Эталон:
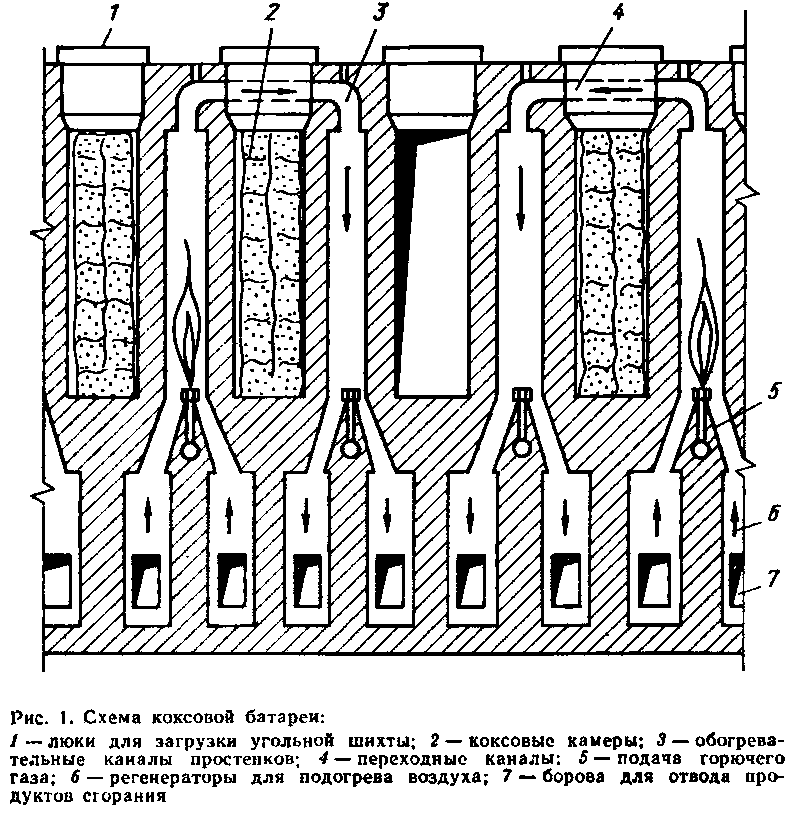
Основным видом топлива доменной плавки является каменноугольный кокс, который представляет собой твердую и прочную пористую массу(83…88% С), оставшуюся после удаления из угля летучих веществ при сухой перегонке его при высокой температуре без доступа воздуха. Кокс получают в коксовых печах или камерах коксования при температурах 950…1100°С. Шихтой для производства кокса служат коксующиеся угли разных сортов, которые сначала дробят, обогащают для уменьшения содержания золы, измельчают и усредняют.
Коксовые печи периодического действия состоят из камер коксования, которые представляют собой камеры динасового кирпича высотой 5…7 м и шириной 0,4…0,45м.
Шихта из угольной башни с помощью загрузочного вагона через люки поступает в узкие (плоские) камеры, которые объединены в коксовые батареи параллельно расположенных по 60…80 камер коксования, каждая из которых имеет объем до 42м3 и позволяет получать за один прием до 20 т кокса.
Нагрев камер до температур около 1100°С обеспечивается за счет применения подогретого воздуха в регенераторах воздуха, используемого для сжигания доменного и коксового газов в простенках между камерами - вертикальных каналах. Камеры регенератора, заполненные решетчатой кладкой из огнеупорного кирпича. В каждую пару регенераторов по очередно с интервалом в 20..30 минут направляют горячий и холодный воздух, который нагревает или охлаждает насадку.
При нагреве в камере:
- до 250°С угольная шихта подсушивается и начинает выделять летучие продукты разложения;
- в интервале 250…350°С выделяется легкая смола;
-выше 450°С уголь начинает превращаться в пластическую массу;
- при 500… 650°С пластическую масса начинает разлагаться с выделением смолы и газа, затвердевает и образуется полукокс;
- при 800°С выделение газа прекращается;
- при температуре около 1000°С образуется кокс.
Процесс коксования длиться 14-16ч, после чего открывают передние и задние торцевые двери камер и специальным выталкивателем коксовый пек в виде пирога выдавливают в вагон, который отправляют в башню для тушения кокса водой или азотом. Охлажденный кокс поступает на сортировку.
Задание 2.
Проверяемые результаты обучения: З1
Текст задания: Описать тепловые процессы, происходящие при агломерации
Эталон:
Агломерация заключается в спекании шихты, состоящей из железной руды мелких фракций (40…50 %), известняка (15 … 20 %), возврата мелкого агломерата (20… 30 %), коксовой мелочи (4 … 6 %), влаги (6…9 %) на специальной машине для улучшения их металлургических свойств. Эти материалы смешиваются с измельченным твердым топливом (коксом, углем), увлажняются и подаются в агломерационную машину слоем 200-300мм. Спекание выполняют на агломерационных машинах при 1300…1500 °С. В процессе спекания из руды удаляются вредные примеси (сера, частично мышьяк), карбонаты разлагаются и получается кусковой пористый офлюсованный материал - агломерат.
Процесс спекания тонкого слоя шихты наиболее часто проводят на машинах ленточного типа. Они представляют собой конвейер, состоящий из большого количества спекательных тележек, двигающихся по направляющим рельсам (рис.).
«Днищем» этих тележек служит колосниковая решетка. На нее загружается тонкий слой мелкого агломерата (постель), чтобы агломерируемая шихта не сыпалась книзу. Затем загружается тщательно перемешанная, увлажненная (7—9 %) и окомкованная шихта. Ее основные железосодержащие компоненты следующие: мелкая и пылеватая железная руда (крупность менее 10 мм), железорудный концентрат, возврат агломерата (менее 10 мм), колошниковая пыль (см. с. 38), иногда окалина, мелкая металлическая стружка и т. д. Топливом (4 – 6 % от массы шихты) служат коксик - мелкий кокс (менее З мм) и антрацитовый штыб (пыль).
Агломерационная машина ленточного типа состоит из большого числа паллет спекательных тележек с отверстиями в днище, двигающихся по направляющим рельсам (рис.). В загруженной паллете после зажигания газовыми горелками начинается горение топлива, причем фронт горения распространяется сверху вниз. Воздух просасывается сквозь слой шихты благодаря действию специальных вакуумных устройств, называемых эксгаустерами. Температура в слое шихты достигает 1300…1600 °С.
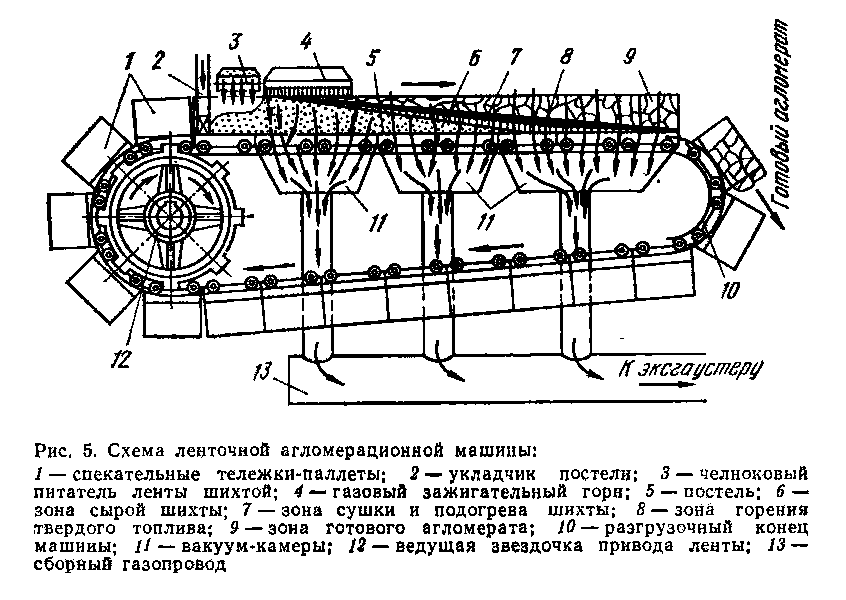
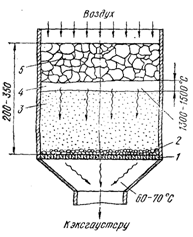
Рисунок - Схема ленточной агломерационной машины:
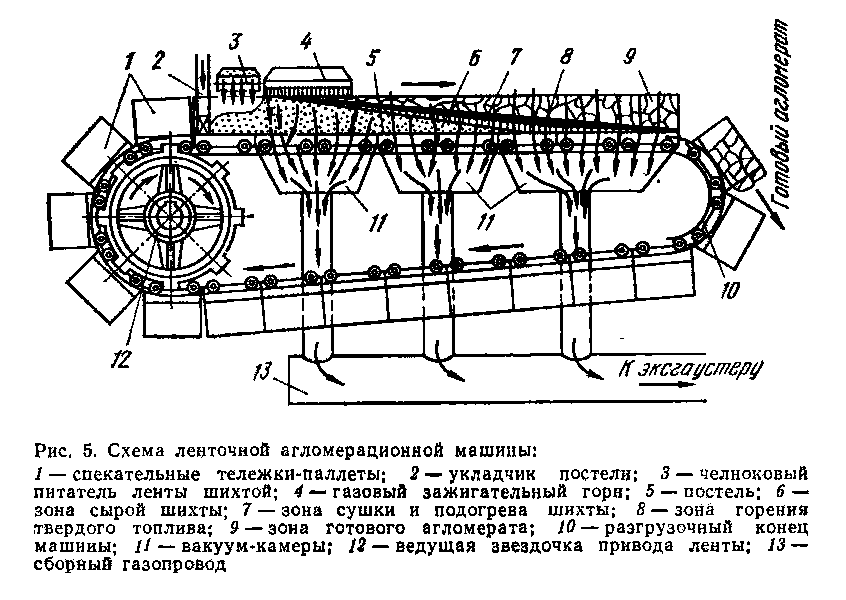
В результате восстановления оксидов железа в присутствии кремнезема образуется фаялит Fе2SiO4 по реакции
2Fе304 + 3Si02 + 2СО = ЗFе2SiO4 + 2СO2.
В зоне горения фаялит, имеющий температуру плавления 1265 °С, плавится и смачивает зерна шихты, благодаря чему при охлаждении образуется твердая пористая масса — агломерат. Агломерат имеет высокую пористость (до 50 %) и хорошую восстанавливаемость. Кроме того, в процессе спекания почти полностью выжигается сера, которая удаляется в виде сернистого газа. В металлургии обычно используют офлюсованный агломерат, для чего в шихту дополнительно вводят известняк.
Задание 3.
Проверяемые результаты обучения: З1
Текст задания: Описать тепловые процессы, происходящие при производстве чугуна в доменной печи
Эталон:
Доменный процесс
Доменная печь работает по принципу противотока. Шихтовые материалы загружают сверху при помощи засыпного (загрузочного) аппарата. Навстречу опускающимся материалам снизу вверх движется поток горячих газов, образующихся при сгорании топлива (кокса), а также природного газа.
В доменной печи протекают следующие основные процессы.
Горение топлива. В районе воздушных фурм (верхняя часть горна), кокс сгорает по реакции С+О2 = 2СО +Q кал.
В результате этой реакции выделяется большое количество тепла и в фокусе горения развивается температура 1800-2000°С. Образующийся углекислый газ СО2 взаимодействует с углеродом кокса, восстанавливаясь до окиси углерода: СО2+Скокса = 2СО - Q.
Окись углерода СО в доменной печи является главным восстановителем железа из его окислов.
Природный газ в основном состоит из метана СН4. В окислительной зоне фурм сначала происходит его полное сгорание по реакции CH4 + 2О2 = CO2 + 2H2O + Q.
Эти продукты сгорания не являются конечными. СО2 восстанавливается углеродом до СО. Пары воды также взаимодействуют с углеродом раскаленного кокса: Н2О + С = Н2 + СО - Q.
По этой же реакции происходит и разложение влаги воздушного дутья.
Таким образом, при использовании природного газа доменный газ дополнительно обогащается СО и Н2, что увеличивает его восстановительную способность.
Восстановление железа, происходит последовательно от высших окислов к низшим, далее к чистому металлу (принцип А. А. Байкова): Fe2O3 Fe3O4 FeO Fe
Главными восстановителями железа в доменной печи являются окись углерода и твердый углерод кокса. Некоторое количество железа восстанавливается водородом.
Восстановление окисью углерода называется косвенным (непрямым) восстановлением и происходит по реакциям
3 Fe2O3 + СО = 2 Fe3O4 + СО2 + Q 400-500оС, верхняя часть шахты
Fe3O4 + СО = 3FeO + СО2 - Q;
FeO + CO =Fe + CO2 + Q 900-950оС, нижняя часть шахты
Восстановление Fe2O3 начинается при сравнительно низких температурах (400-500°С) в верхней части шахты печи. По мере опускания рудных материалов повышаются температура и содержание СО в доменных газах; при этом создаются условия для окончательного восстановления железа. Эти процессы заканчиваются в нижней части шахты печи при температурах около 900-950°С.
Одновременно в шахте печи происходит косвенное восстановление окислов железа водородом. Значение косвенного восстановления очень велико. В зависимости от условий работы печи окисью углерода СО и водородом восстанавливается 60-80% всего железа. Остальная часть железа восстанавливается твердым углеродом.
Восстановление твердым углеродом называется прямым восстановлением.
Оно происходит при температурах выше 950-1000°С (зона распара печи и заплечики) по реакции FeO + C = Fe+CО - Q
Науглероживание железа. Восстановление железа начинается при 400-500°С и заканчивается при 1300-1400°С (в распаре печи). При этих температурах железо (Тпл = 1539°С) находится в твердом состоянии в виде пористой губчатой массы.
Уже в шахте доменной печи при температурах выше 400-500оС наряду с восстановлением железа происходит и его науглероживание за счет окиси углерода СО по реакции 3Fe + 2CO = Fe3C + CO2+ Q
Карбид железа Fe3C хорошо растворяется в твердом железе и постепенно образуется сплав железа с углеродом. С увеличением содержания углерода температура плавления сплава значительно понижается и достигает минимального значения 1147°С при 4,2% С. В зонах печи с высокими температурами - обычно в нижней части шахты - начинается плавление сплава. Жидкий сплав - чугун, стекая вниз, омывает куски раскаленного кокса и дополнительно интенсивно науглероживается. В нем также растворяются восстановленный марганец, кремний и другие примеси. Конечный состав чугуна устанавливается в горне. При этом большое значение имеют состав, свойства и количество шлака.
Восстановление других элементов. В доменную печь с шихтовыми материалами попадают марганец, кремний, сера и другие элементы в виде различных химических соединений. Эти элементы частично или полностью восстанавливаются и входят в состав чугуна, улучшая или ухудшая его свойства.
Постоянными полезными примесями чугуна являются марганец и кремний, вредными - сера и фосфор.
Марганец - постоянная примесь железных руд. При выплавке чугунов с повышенным содержанием марганца в доменную печь загружается марганцовая руда.
Высшие окислы марганца восстанавливаются до закиси марганца MnO окисью углерода, аналогично окислам железа: MnО2 Mn2О3 Mn3О4 MnО.
Закись марганца восстанавливается твердым углеродом по реакция Mn + CO - Q.
Эта реакция протекает при температурах выше 1000°С с поглощением тепла. Поэтому для восстановления марганца требуется увеличивать расход кокса и температуру дутья.
Кремний находится в пустой породе руды и в золе кокса в виде свободного кремнезема SiO2 или в виде силикатов.
Восстановление кремния происходит по реакции
SiO2 + 2C = Si + 2CO - Q
Другие полезные примеси - никель, ванадий, хром и т. д. - попадают в доменную печь в виде примесей железной руды. При доменной плавке никель восстанавливается и переходит в чугун полностью, хром на 85-95%, ванадий - на 70-80% и т. д.
Фосфор - вредная примесь железных руд находится в них главным образом в виде Р2О5·3СаО. Восстановление фосфора происходит окисью углерода СО, водородом, а также твердым углеродом. Весь фосфор, внесенный шихтой, восстанавливается и переходит в чугун практически полностью.
Сера - особенно вредная примесь в чугуне (и в стали). Основное количество серы вносит кокс, часть железная руда, агломерат, окатыши. В доменной печи 10-20% серы удаляется в виде газообразных соединений (SO2 H2S и др.). Остальная часть серы переходит в чугун и в шлак в виде сульфидов FeS, CaS и др. Сульфид железа хорошо растворяется в чугуне. В условиях доменной плавки основным способом десульфурации, т. е. удаления серы из металла, является образование сульфида кальция CaS по реакции FeS + CaO = FeO + CaS +Q. Сульфид кальция CaS нерастворим в чугуне и находится в шлаке.
Шлакообразование начинается примерно в распаре печи. Первичный шлак образуется в результате сплавления CaO, SiO2, AI2О3 и других окислов, находящихся в составе флюса и пустой породы. При определенных соотношениях по массе эти тугоплавкие окислы могут образовывать легкоплавкие смеси - сплавы с Тпл = 1150…1200°С. Стекая вниз и накапливаясь в горне, шлак существенно изменяет свой состав. В результате взаимодействия с расплавленным чугуном и остатками несгоревшего кокса в шлаке восстанавливаются окислы железа и марганца, в нем растворяются FeS, MnS, зола кокса и т.д. Химический состав шлака определяет состав чугуна и поэтому при выплавке передельных, литейных и других чугунов всегда подбирают шлак соответствующего состава. Типовой состав шлака: 40-50% СаО; 38-40% SiO2; 7-10% AI2O3).
Одна из важнейших характеристик шлака - его основность, т.е., отношение содержания основных окислов к содержанию кислотных окислов. В заводской практике основность нередко определяется упрощенно, как В = %(СаО)/%(SiO2).
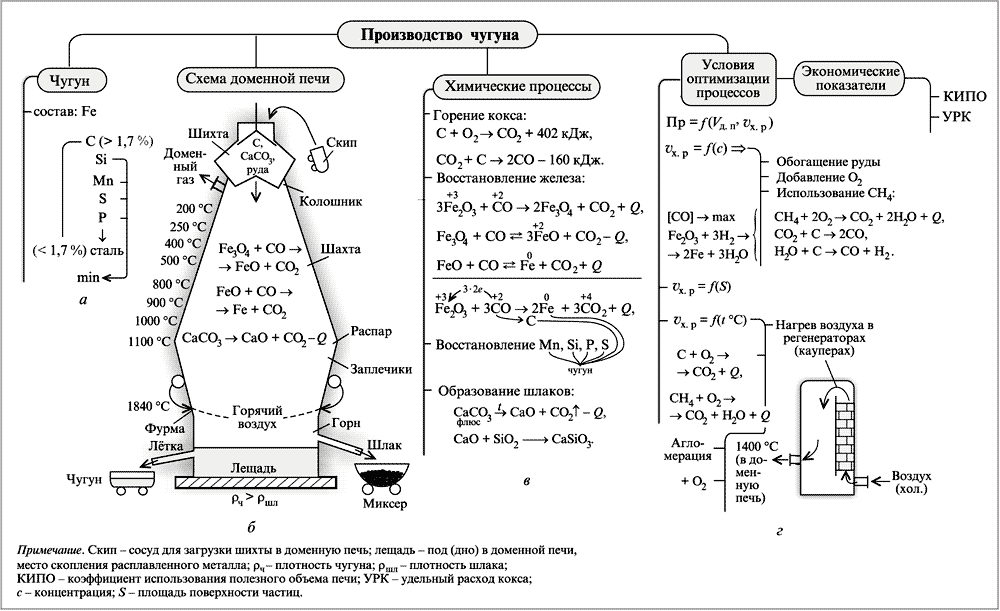
Рисунок - Схема производств чугуна в доменной печи
Задание 4
Проверяемые результаты обучения: З1
Текст задания: Описать тепловые процессы, происходящие при производстве стали в конвертерах
Эталон
Источником теплоты при конвертерном способе являются химические реакции окисления элементов, входящих в состав чугуна. Окисление протекает в основном за счет кислорода дутья (воздуха, технически чистого кислорода, газо-кислородной смеси). В настоящее время дутье подается в различных конвертерах через днище, сбоку или сверху
Процесс производства стали в кислородном конвертере состоит из следующих основных периодов: загрузки металлолома, заливки чугуна, продувки кислородом, загрузки шлакообразующих, слива стали и шлака.
Загрузка конвертера начинается с завалки стального лома. Лом загружают в наклоненный конвертер через горловину при помощи завалочных машин лоткового типа.
Затем с помощью заливочных кранов заливают жидкий чугун температура которого должна быть в пределах 1260…1450° С, конвертер устанавливают в вертикальное положение, вводят фурму и включают подачу кислорода с чистотой не менее 99,5 % О2. Одновременно с началом продувки загружают первую порцию шлакообразующих и железной руды (40 - 60 % от общего количества). Остальную часть сыпучих материалов подают в конвертер в процессе продувки одной или несколькими порциями, чаще всего 5 - 7 минут после начала продувки.
Последовательность технологических операций при выплавке стали в кислородных конвертерах представлена на рисунке.
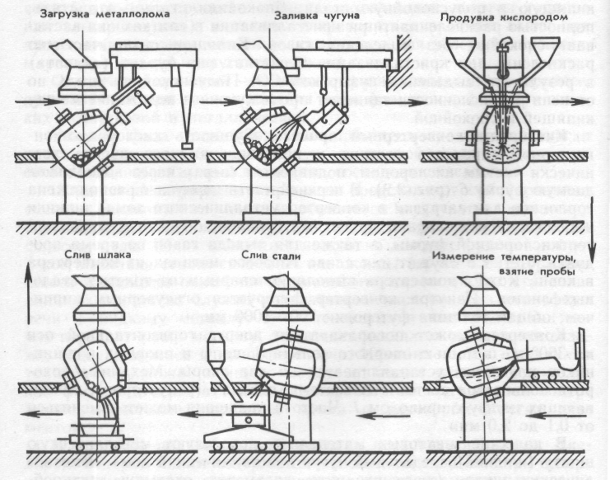
Рисунок - Схема производства стали в конвертерах
Кислородное дутье подают вертикальной водоохлаждаемой фурмой, которую можно перемещать по высоте. Она состоит из трех друг в друге сваренных труб. По внутренней трубе подается кислород, по наружным — подводится и отводится охлаждающая вода. Формирование кислородной струи производится медной головкой с одним или несколькими соплами. Сопло Лаваля позволяет подавать кислород со скоростью более 500 м/с.
Изменяя расстояние от фурмы до поверхности ванны, управляют глубиной внедрения струи и образования зоны контакта ее со шлаком и металлом. Окисление всех примесей чугуна начинается с самого начала продувки. При этом наиболее сильно окисляется кремний и марганец, это объясняется высоким сродством к кислороду этих элементов при сравнительно низких температурах 1450..1500° С. Окисление углерода в кислородо-конвертерном процессе играет важную роль, т.к. влияет на температурный режим плавки, процесс шлакообразования, рафинирование металла от фосфора, серы, газов и неметаллических включений.
Окислительные процессы в шлаке и на границе шлак — металл регулируют изменением расхода кислорода. В реакционной зоне возникают высокие температуры, достигающие 2200—2400° С. Они вызывают испарение железа и его окисление в газах с выделением из конвертера бурого дыма. Продувка в зависимости от интенсивности подачи кислорода продолжается
С первых минут продувки идет интенсивное удаление фосфора идет при сравнительно низкой температуры металла, высоком содержании в шлаке (FeO); основность шлака и его количество быстро увеличивается. Кислородно-конвертерный процесс позволяет получить
Условия для удаления серы при кислородно-конвертерном процессе нельзя считать таким же благоприятным, как для удаления фосфора. Причина заключается в том, что шлак содержит значительное количество (FeO) и высокая основность шлака ( 2,5) достигается лишь во второй половине продувки.
Степень десульфурации при кислородно-конвертерном процессе находится в пределах 30 - 50 % и содержание серы в готовой стали составляет 0,02 - 0,04 %. По достижении заданного содержания углерода дутые отключают, фурму поднимают, конвертер наклоняют и металл через летку (для уменьшения перемешивания металла и шлака) выливают в ковш. Полученный металл содержит повышенное содержание кислорода, поэтому заключительной операцией плавки является раскисление металла, которое проводят в сталеразливочном ковше.
Для этой цели одновременно со сливом стали по специальному поворотному желобу в ковш попадают раскислители и легирующие добавки. Шлак из конвертера сливают через горловину в шлаковый ковш, установленный на шлаковозе под конвертером. Течение кислородно-конвертерного процесса обусловливается температурным режимом и регулируется изменением количества дутья и введением в конвертер охладителей - металлолома, железной руды, известняка. Температура металла при выпуске из конвертера около 1600° С.
Задание 5. Проверяемые результаты обучения: З1
Текст задания: Описать тепловые процессы, происходящие при производстве стали в электродуговой печи
Эталон:
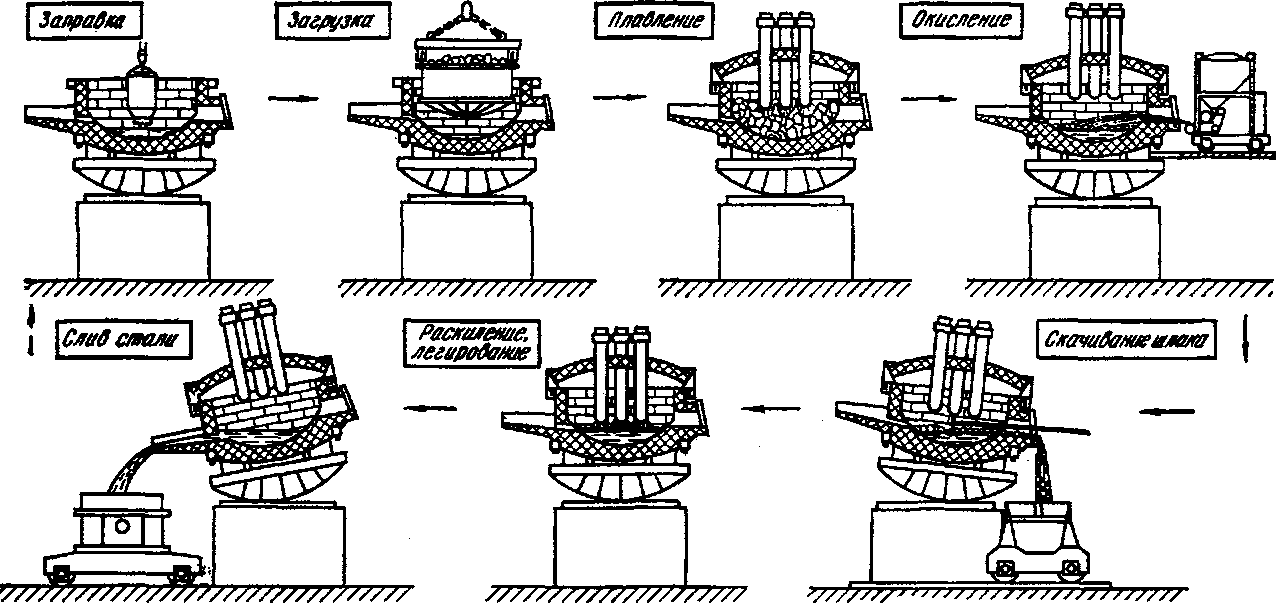
Рисунок - Схема производства стали в электродуговой печи
Электропечь – наиболее совершенный агрегат для производства стали. В них выплавляются качественные легированные стали. Это объясняется тем, что здесь можно точно регулировать температуру металла, создавать окислительную, восстановительную, нейтральную атмосферу или вакуум, более полно раскислить металл.
Источником тепла в дуговой печи является электрическая дуга, возникающая между электродами и жидким металлом или шихтой при приложении к электродам электрического тока необходимой силы. Дуга представляет собой поток электронов, ионизированных газов и паров металла и шлака. Температура электрической дуги превышает 3000 °С.
Шихта при плавке с полным окислением состоит, главным образом, из стального лома и чугуна, а также шлакообразующих (известь, известняк, плавиковый шпат, шамотный бой).
Плавка включает следующие основные периоды - заправка печи, загрузка шихты, плавление, окислительный период, восстановительный период, выпуск.
Заправка печи выполняется для поддержания футеровки плавильного пространства в рабочем состоянии. Для этого после выпуска очередной плавки на поврежденные места подины и откосов - места перехода подины печи в стены - с помощью заправочной машины забрасывают сухой магнезитовый порошок, а в случае больших повреждений - порошок с добавками пека или смолы.
Завалка шихты начинается сразу после окончания заправки. Завалку шихты осуществляют сверху с помощью загрузочной корзины (бадьи). Затем с помощью заливочных кранов заливают жидкий чугун температура которого должна быть в пределах 1260…1450° С. Приспособления кислородных для интенсивной продувки ванны кислородом, позволило использовать в их шихте жидкий чугун. Заливка чугуна осуществляется примерно в середине периода плавления через специальную заливочную воронку в своде печи. Сразу же после этого начинается продувка ванны кислородом.
Плавление. После окончания завалки свод с электродами устанавливают на печь, электроды опускают и включают ток. Под действием высокой температуры электрической дуги шихта плавится сначала под электродами, жидкий металл стекает вниз и накапливается в центральной части подины. Постепенно происходит полное расплавление шихты. Для ускорения плавления куски переплавившейся шихты с откосов печи сталкивают в зону электрических дуг. Характерной особенностью первого периода плавления является проплавление «колодцев» в шихте, в которые опускают электроды (или одного «колодца» в сверхмощных печах). В период плавления происходит образование шлака как за счет присадок извести, так и за счет окисления элементов, входящих в состав шихты. За время плавления полностью окисляется кремний, 50-60 % марганца, частично окисляются углерод и железо, окисляется фосфор.
Окислительный период
Окислительный период проводится для решения следующих задач: обезуглероживание металла до содержания углерода, соответствующего требованиям готовой стали; дефосфорация металла до содержания фосфора на 0,010- 0,015% ниже требуемого в готовой стали; нагрев металла до температуры, превышающей температуру плавления на 100-130°С; удаление из металла серы и газов (водорода и азота) в той мере, в какой это возможно.
Для окисления примесей используют твердые окислители (железная руда, агломерат), а также газообразный кислород. Присадки руды или продувка кислородом вызывают интенсивное окисление углерода, и выделяющиеся при этом пузырьки СО создают активное кипение ванны. Это способствует быстрому нагреву металла, удалению газов - водорода и азота, а также неметаллических включений. Окислительный период заканчивается, когда содержание углерода становится несколько ниже заданного предела, содержание фосфора ниже 0,01 %. В конце окислительного периода полностью удаляют из печи шлак.
Восстановительный период плавки имеет целью раскисление металла, удаление серы, доведение химического состава стали до заданного, регулирование температуры. Все эти задачи решаются параллельно в течение всего восстановительного периода. После полного удаления окислительного шлака в печь присаживают шлакообразующие смеси вместе с раскислителями, т. е. наводится новый шлак (карбидный или белый). В качестве раскислителей обычно используют ферромарганец, ферросилиций, алюминий. В печь присаживают также легирующие добавки для введения в металл необходимых легирующих элементов.
После этого металл выпускают из печи в установленный под желобом сталеразливочный ковш, для чего печь наклоняют в сторону сталевыпускного отверстия. Температура металла при выпуске электродуговой печи около 1600 … 1680° С.
При необходимости в ковше можно проводить дополнительное раскисление и легирование стали. Так осуществляется двушлаковый процесс выплавки.
Задание 6. Проверяемые результаты обучения: З1
Текст задания: Описать тепловые процессы, происходящие при непрерывной разливке стали.
Эталон:
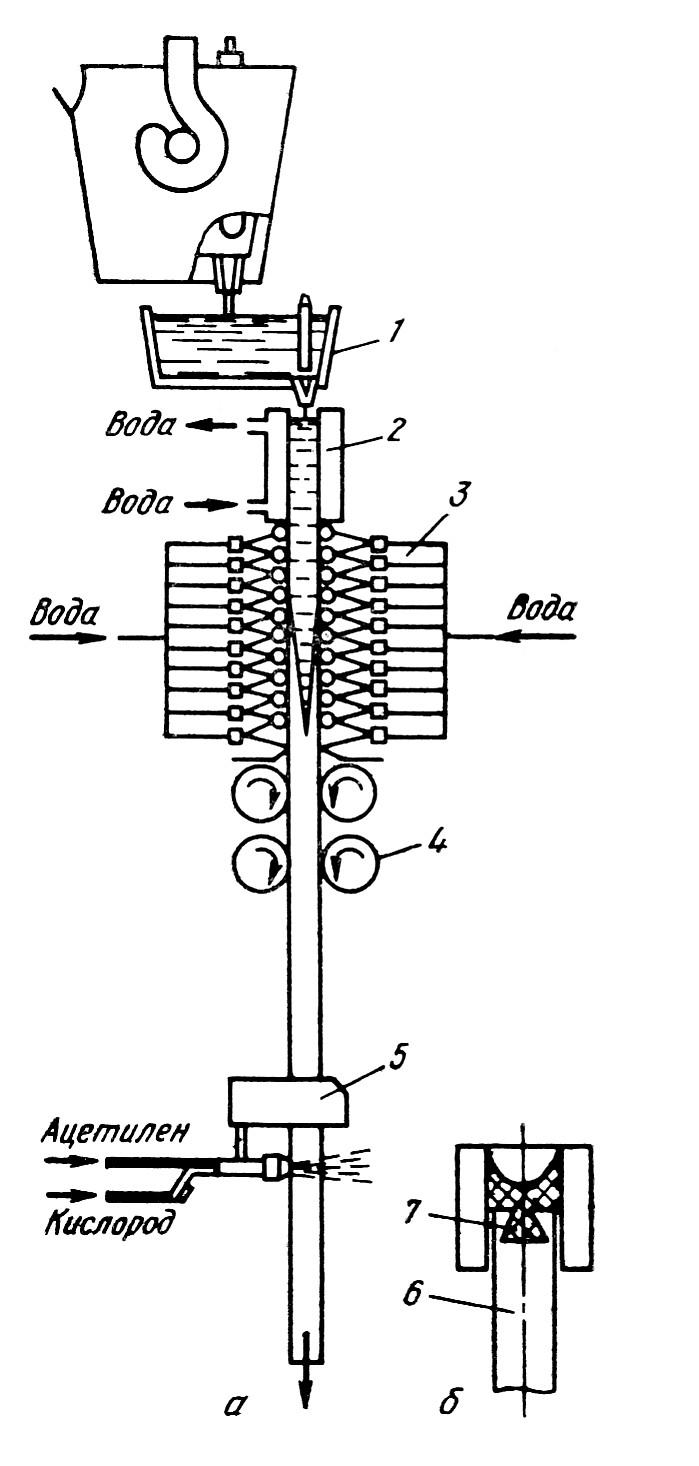
Рисунок – Схема разливки стали на МНЛЗ (а) и действие затравки (б): 1- промежуточный
ковш;2-кристаллизатор;3-зона вторичного охлаждения;4-тянущая клеть; 5-резка;6-
затравка;7-закристаллизовавшийся металл
Жидкая сталь поступает в разливочное отделение при t = 1560 - 1580°С. Из сталеразливочного металл подается в промежуточный ковш, предварительно нагретый до 1100°С.
Если принять температуру кристаллизации tкр для большинства сталей 1500°С, то в промежуточный ковш сталь должна поступать с небольшим перегревом. Обычно температура стали в промковше поддерживается на уровне 1540 — 1560°С, что обеспечивает удовлетворительное качество поверхности слитков и стабильность процесса разливки. Однако с повышением температуры металла более 1570°С возрастает пораженность слитков наружными продольными и поперечными трещинами.
Для обеспечения стабильности процесса разливки температура металла в кристаллизаторе должна быть на 15 — 20°С выше температуры затвердевания, однако по условиям качества слитка перегрев должен быть не более 30°С.
В кристаллизаторе за счет интенсивного охлаждения но периметру слитка затвердевают поверхностные слои металла, образуя твердую корочку или оболочку слитка. Внутри слитка по центральной оси сохраняется жидкая фаза. Стальная заготовка формируется в соответствии с формой и размерами кристаллизатора. Застывшая в кристаллизаторе сталь сцепляется с затравкой, а образующийся слиток вытягивается вниз с помощью тянущих клетей.
Для предотвращения прилипания жидкой стали к стенке кристаллизатора предусмотрен механизм качания. Кристаллизатор совершает возвратно-поступательное движение с заданной частотой качания, а в зазор между стенкой кристаллизатора и поверхностью слитка подается специальная смазка.
Толщина затвердевшей корочки на выходе из кристаллизатора должна быть (25-30) мм, чтобы обеспечить достаточную механическую прочность вытягиваемой заготовки и исключить возможность прорыва жидкого металла. По некоторым зарубежным данным толщина корочки должна быть (15 -25) мм в зависимости от размеров заготовки.
Температура поверхности слитка на выходе из кристаллизатора составляет
Слиток с затвердевшей корочкой, попадающий из кристаллизатора в зону вторичного охлаждения, в результате форсированного поверхностного охлаждения затвердевает по всему сечению. Форма слитка сохраняется за счет специальной поддерживающей системы (роликовой, брусьевой и др.). После прекращения подачи воды слиток охлаждается на воздухе.
В конце зоны вторичного охлаждения температура поверхности (tп) слитка снижается до уровня 800-900°С. Слиток принудительно вытягивается с помощью тянущих клетей, а затем поступает в газорезку, где разрезается на мерные куски заданной длины. Далее заготовки по рольгангу транспортируются на склад.
Задание 7. Проверяемые результаты обучения: З1
Текст задания: Описать тепловые процессы, происходящие при процесса прокатки стали
Эталон:
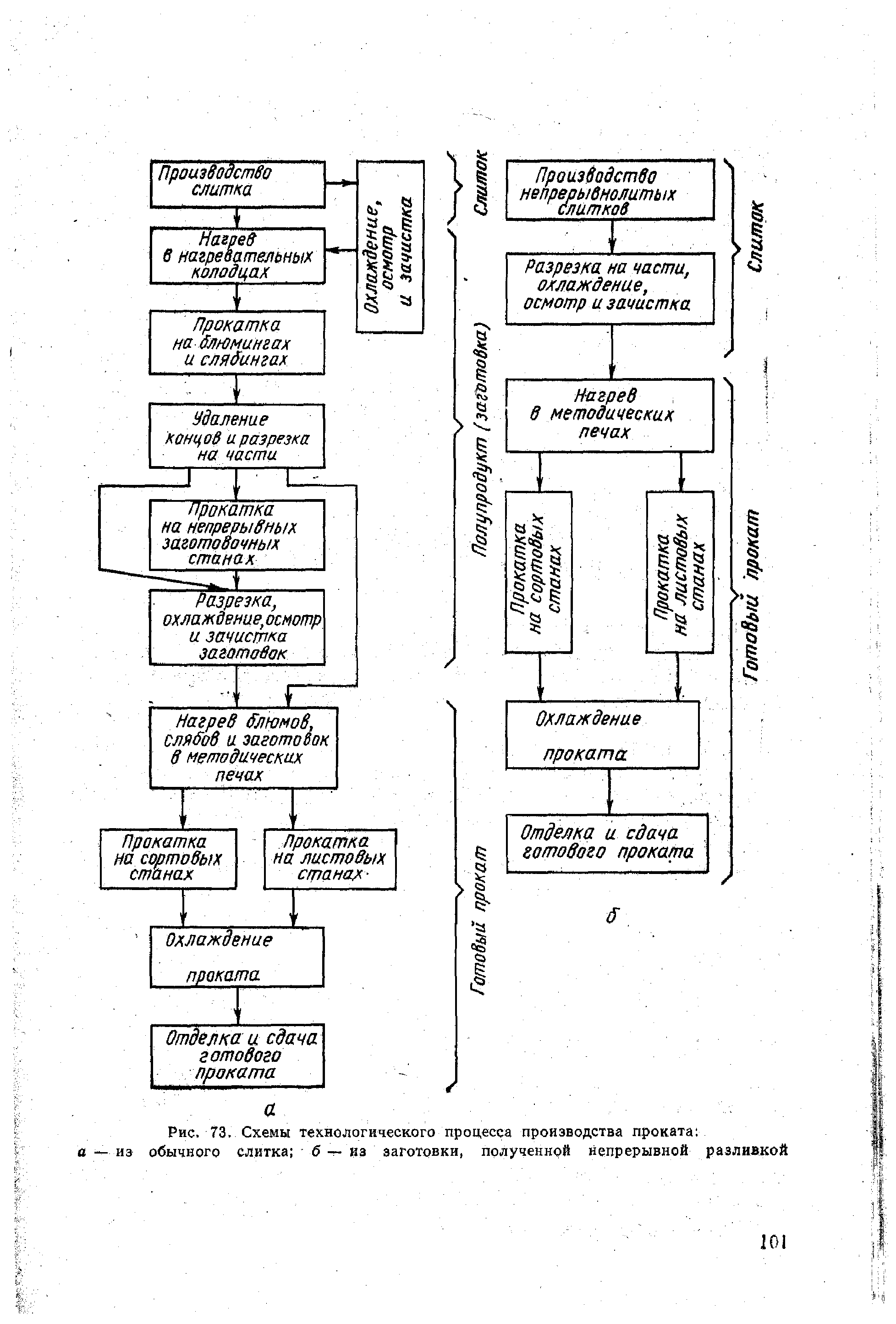
Основными технологическими операциями прокатного производства являются подготовка исходных слитков или заготовок к прокатке, нагрев металла перед прокаткой, прокатка и охлаждение, термическая обработка и отделка готовой продукции.
В результате проведения технологических операций происходит изменение свойств металла, геометрической формы и размеров. Однако не всегда осуществляются все перечисленные технологические операции. Их перечень зависит от вида производства
(горячего или холодного).
подготовка исходных слитков или заготовок к прокатке включает удаление различных поверхностных дефектов (трещин, царапин, закатов), что увеличивает выход готового проката.
нагрев металла перед прокаткой обеспечивает высокую пластичность, высокое качество готового проката и получение требуемой структуры. Необходимо строгое соблюдение режимов нагрева. Основное требование при нагреве: равномерный прогрев слитка или заготовки по сечению и длине до соответствующей температуры за минимальное время с наименьшей потерей металла в окалину и экономным расходом топлива.
Прокатка и охлаждение (температуры начала и конца горячей деформации) определяются в зависимости от температур плавления и рекристаллизации. Прокатка большинства марок углеродистой стали начинается при температуре 1200…1150 0С, а заканчивается при температуре 950…9000С.
Существенное значение имеет режим охлаждения. Быстрое и неравномерное охлаждение приводит к образованию трещин и короблению.
При прокатке контролируется температура начала и конца процесса, режим обжатия, настройка валков в результате наблюдения за размерами и формой проката. Для контроля состояния поверхности проката регулярно отбирают пробы.
Отделка проката включает резку на мерные длины, правку, удаление поверхностных дефектов и т.п. Готовый прокат подвергают конечному контролю.
Процесс прокатки осуществляют на специальных прокатных станах.
Задание 8. Проверяемые результаты обучения: З1
Текст задания: Описать тепловые процессы, происходящие при литье металла в оболочковые формы
Эталон:
Литье - это способ изготовления заготовки или изделия заполнением полости заданной конфигурации жидким металлом с последующим его затвердеванием. Иными словами, процесс литья заключается в заливке расплавленного и перегретого (до оптимальной температуры) металла в литейную форму, внутренняя полость которой соответствует (с определенным допуском) конфигурации и размерам будущей детали. Заготовку или изделие, получаемое методом литья, называют отливкой.
Литье в оболочковые формы - это способ получения отливок свободной заливкой расплава в оболочковые формы из термореактивных смесей.
Оболочковые формы отличаются высоким комплексом технологических свойств: достаточной прочностью, газопроницаемостью, податливостью, негигроскопичностью. По сравнению с отливками, полученными в песчаных формах, детали, отлитые в оболочковые формы, имеют в 1,5 раза меньший припуск на механическую обработку.
Оболочковые формы изготавливают из формовочных песчано-смоляных смесей с термопластичными или термореактивными связующими смолами.
Оболочковые формы получают с помощью нагретых металлических моделей, изготавливаемых из серого чугуна, стали и алюминиевых сплавов. Каждая форма состоит из двух соединенных (путем склеивания пульвербакелитом и жидким клеем или с помощью скоб, струбцин) оболочковых полуформ. Толщины оболочек для мелких и среднего размера отливок колеблются соответственно в пределах 8 - 10 мм и 12 - 15 мм. Технология изготовления оболочек включает в себя следующие операции.
Нагрев модельной оснастки до 200 - 250°С.
Нанесение на рабочую поверхность модельной оснастки (пульверизатором) разделительного состава - быстро затвердевающей силиконовой жидкости, образующей при этом разделительную пленку, которая предотвращает прилипание оснастке формовочной смеси и тем самым упрощает последующее отделение оболочки от модели.
Нагретая и обработанная разделительным составом модельная плита с моделью закрепляется на приемной рамке поворотного бункера. Засыпка модели и модельной плиты смесью осуществляется поворотом бункера на 180°. Для формирования оболочки толщиной 5 - 15 мм плиту выдерживают под смесью в течение 15 -20 с. При этом смола быстро плавится и затвердевает, образуя полутвердую оболочку. Затем бункер возвращают в исходное положение. С него снимают модельную плиту с налипшей оболочкой и помещают ее в печь для доотверждения оболочки (режим окончательного отверждения смолы - 300 -350°С, 1 - 3 мин).
Съем оболочковой полуформы после ее изготовления с модели осуществляется с помощью толкателей.
Перед заливкой собранные формы с вертикальной плоскостью разъема (а также формы крупных размеров) помещают в контейнеры и засыпают чугунной дробью. Этим предотвращается коробление и разрушение форм при их заливке расплавом. Небольшие формы с горизонтальной плоскостью разъема устанавливаются для заливки на слой песка.
Способом литья в оболочковые формы получают отливки массой от 0,2 до 200 кг из практически любых литейных сплавов. Этим способом изготавливают ребристые мотоциклетные цилиндры, коленчатые валы автомобильных двигателей.
Преимущества способа литья в оболочковые формы: возможность получения тонкостенных отливок сложной формы; гладкая и чистая поверхность отливок; небольшой расход смеси; качественная структура металла за счет повышенной газопроницаемости форм; широкая возможность автоматизации; небольшие допуски на обработку резанием.
Недостатки: ограниченный размер отливок (до 1500 мм); высокая стоимость смесей; выделение вредных паров и газов из смесей при изготовлении форм.
Задание 9. Проверяемые результаты обучения: З1
Текст задания: Описать тепловые процессы, происходящие при литье в кокиль
Эталон
Кокильным литьем называют процесс получения отливок посредством свободной заливки расплавленного металла в многократно используемые металлические формы - кокили.
Кокили бывают неразъемные и разъемные. Все перечисленные типы кокилей могут быть одно- и многогнездные (то есть для получения одной отливки или одновременно нескольких), немеханизированные (ручные), механизированные, автоматизированные и автоматические.
Материалы, используемые для изготовления кокилей, должны хорошо противостоять термическим ударам, возникающим при заливке металла, легко обрабатываться, быть недефицитными и недорогими. Кокили изготавливают из серого и высокопрочного чугуна, конструкционных углеродистых и легированных сталей, медных (латуни) и алюминиевых сплавов. С помощью одной формы (или большей части ее элементов) кокильным литьем получают до 500 мелких стальных, 5000 чугунных или десятки тысяч алюминиевых отливок. Отдельные элементы кокиля (в первую очередь - стержни, оформляющие внутренние полости отливки) могут изготавливаться как из металла, так и из стержневой смеси; в последнем случае они предназначаются лишь для разового использования. Металлические стержни сложной формы целесообразно делать разборными.
Технологический процесс кокильного литья требует специальной подготовки кокиля к заливке и включает следующие операции:
1) очистку рабочей поверхности кокиля от остатков отработанного покрытия, загрязнений и ржавчины;
2) нанесение (пульверизатором или кистью) на предварительно подогретые до 100 - 150°С рабочие поверхности кокиля специальных теплоизоляционных слоев и противопригарных красок, одновременно повышающих качество поверхности отливок;
3) нагрев кокиля до оптимальной (для каждого сплава своей) температуры в пределах 115 - 475°С в целях повышения заполняемости формы расплавом и тем самым улучшения качества отливок. Необходимость предварительного подогрева кокиля обуславливается скоплением в нем (на холодных стенках, щелях по разъему, в вентах) водного конденсата, взаимодействие которого с расплавом при заливке может привести к взрыву и разрушению кокиля;
4) сборку формы, состоящую из простановки стержней и соединения металлических полуформ;
5) заливку расплава в форму;
6) охлаждение отливок до установленной температуры. Искусственное охлаждение кокиля применяют с целью увеличения скорости затвердевания и охлаждения отливки, уменьшения продолжительности цикла литья, и ,как следствие, повышения стойкости кокиля. Искусственному охлаждению могут подвергаться как рабочая или наружная поверхности, так и их фрагменты;
7) разборку кокиля с извлечением отливки.
Основные достоинства кокильного литья - многократное использование формы, более высокая производительность труда, точность отливок, качество их поверхности и стабильность размеров.
Недостатками литья в кокиль являются их высокая стоимость, трудоемкость изготовления кокилей, отсутствие податливости, особенно при получении сложных фасонных отливок из легированных сталей и тугоплавких металлов.
Данным способом получают в основном отливки из сплавов на основе меди, алюминия, магния, а также стали и чугуна массой до 2000 кг.
Часть Б
Задание. 10 Проверяемые результаты обучения: У1
Текст задания: Рассчитать суточный расход кокса для доменной печи, используя следующие исходные данные:
Полезный объем доменной печи, Vп,м3 | Удельный расход кокса, К,кг/т | Удельная производительность доменной печи, Пуд, т/сут |
2014 | 450 | 2,3 |
Эталон
Решение
Определяем суточную производительность доменной печи
Псут= Vп * Пуд = 2014*2,3=4632,2 т чугуна/сут.
Определяем суточный расход кокса (в тоннах):
Ксут= Псут* К= 4632,2*0,45=2084,49 т кокса/сут.
Задание.11 Проверяемые результаты обучения: У1
Текст задания: Рассчитать суточный расход кокса для доменной печи, используя следующие исходные данные:
Полезный объем доменной печи, Vп,м3 | Удельный расход кокса, К,кг/т | Удельная производительность доменной печи, Пуд, т/сут |
2014 | 480 | 2,25 |
Эталон
Решение
Определяем суточную производительность доменной печи
Псут= Vп * Пуд = чугуна/сут.
Определяем суточный расход кокса (в тоннах):
Ксут= Псут* К= кокса/сут.
Задание. 12 Проверяемые результаты обучения: У1
Текст задания: Рассчитать суточный расход кокса для доменной печи, используя следующие исходные данные:
Полезный объем доменной печи, Vп,м3 | Удельный расход кокса, К,кг/т | Удельная производительность доменной печи, Пуд, т/сут |
1380 | 460 | 2,29 |
Эталон
Решение
Определяем суточную производительность доменной печи
Псут= Vп * Пуд = чугуна/сут.
Определяем суточный расход кокса (в тоннах):
Ксут= Псут* К= кокса/сут.
Задание.13 Проверяемые результаты обучения У1
Текст задания: Рассчитать суточный расход кокса для доменной печи, используя следующие исходные данные:
Полезный объем доменной печи, Vп,м3 | Удельный расход кокса, К,кг/т | Удельная производительность доменной печи, Пуд, т/сут |
1380 | 472 | 2,35 |
Эталон
Решение
Определяем суточную производительность доменной печи
Псут= Vп * Пуд = чугуна/сут.
Определяем суточный расход кокса (в тоннах):
Ксут= Псут* К= кокса/сут.
Задание.14 Проверяемые результаты обучения: У1
Текст задания: Рассчитать суточный расход кокса для доменной печи, используя следующие исходные данные:
Полезный объем доменной печи, Vп,м3 | Удельный расход кокса, К,кг/т | Удельная производительность доменной печи, Пуд, т/сут |
5000 | 445 | 2,35 |
Эталон
Решение
Определяем суточную производительность доменной печи
Псут= Vп * Пуд = чугуна/сут.
Определяем суточный расход кокса (в тоннах):
Ксут= Псут* К= кокса/сут.
Задание. 15 Проверяемые результаты обучения: У1
Текст задания: Рассчитать суточный расход кокса для доменной печи, используя следующие исходные данные:
Полезный объем доменной печи, Vп,м3 | Удельный расход кокса, К,кг/т | Удельная производительность доменной печи, Пуд, т/сут |
5500 | 452 | 2,36 |
Эталон
Решение
Определяем суточную производительность доменной печи
Псут= Vп * Пуд = чугуна/сут.
Определяем суточный расход кокса (в тоннах):
Ксут= Псут* К= кокса/сут.
Задание.16 Проверяемые результаты обучения: У1
Текст задания: Рассчитать суточный расход кокса для доменной печи, используя следующие исходные данные:
Полезный объем доменной печи, Vп,м3 | Удельный расход кокса, К,кг/т | Удельная производительность доменной печи, Пуд, т/сут |
3800 | 461 | 2,26 |
Эталон
Решение
Определяем суточную производительность доменной печи
Псут= Vп * Пуд = чугуна/сут.
Определяем суточный расход кокса (в тоннах):
Ксут= Псут* К= кокса/сут.
Задание. 17 Проверяемые результаты обучения: У1
Текст задания: Рассчитать необходимую суточную производительность агломерационного цеха ОАО «ММК» при среднем расходе агломерата на выплавку 1т чугуна, равным 1620 кг/т.
№ доменной печи | 1 | 2 | 4 | 6 | 7 | 8 | 9 | 10 |
Удельная производительность доменной печи, Пуд, т/сут | 2,3 | 2,25 | 2,29 | 2,35 | 2,35 | 2,36 | 2,26 | 2,35 |
Полезные объемы доменных печей доменного цеха ОАО «ММК», Vп,м3 | 1380 | 1380 | 1380 | 1380 | 1380 | 1380 | 2014 | 2014 |
Определить суточную производительность доменного цеха
Определить суточную потребность доменного цеха в агломерате
Эталон
Решение
Определяем суточную производительность доменного цеха (поочередно складывая суточную производительность для каждой доменной печи):
Псут= Vп *Пуд
Псут = 1380 * 2,3 + 1380 * 2,25 + 1380 * 2,29 + 1380 * 2,3 5+ 1380 * 2,35 + 1380 * 2,36 + 2014 * 2,26 + 2014 * 2,35 = 28466,54 т чугуна / сут.
Определяем суточную потребность доменного цеха в агломерате, а значит и необходимую суточную производительность агломерационного цеха ОАО «ММК»:
Асут= Псут* А. =т чугуна / сут.
Асут= 28466,54*1,620=46115,8 т/сут = 46,1 тыс.т агломерата/сут
Задание. 18 Проверяемые результаты обучения: У1
Текст задания: Рассчитать необходимую суточную производительность агломерационного цеха ОАО «ММК» при среднем расходе агломерата на выплавку 1т чугуна, равным 1620 кг/т.
№ доменной печи | 1 | 2 | 4 | 6 | 7 | 8 | 9 | 10 |
Удельная производительность доменной печи, Пуд, т/сут | 2,32 | 2,36 | 2,40 | 2,31 | 2,30 | 2,29 | 2,27 | 2,28 |
Полезные объемы доменных печей доменного цеха ОАО «ММК», Vп,м3 | 1380 | 1380 | 1380 | 1380 | 1380 | 1380 | 2014 | 2014 |
Определить суточную производительность доменного цеха
Определить суточную потребность доменного цеха в агломерате
Эталон
Решение
Определяем суточную производительность доменного цеха (поочередно складывая суточную производительность для каждой доменной печи):
Псут= Vп *Пуд = т чугуна / сут.
Определяем суточную потребность доменного цеха в агломерате, а значит и необходимую суточную производительность агломерационного цеха ОАО «ММК»:
Асут= Псут* А.= тыс.т агломерата/сут
Задание. 19 Проверяемые результаты обучения: У1
Текст задания: Рассчитать необходимую суточную производительность агломерационного цеха ОАО «ММК» при среднем расходе агломерата на выплавку 1т чугуна, равным 1620 кг/т.
№ доменной печи | 1 | 2 | 4 | 6 | 7 | 8 | 9 | 10 |
Удельная производительность доменной печи, Пуд, т/сут | 2,28 | 2,34 | 2,31 | 2,32 | 2,28 | 2,35 | 2,30 | 2,29 |
Полезные объемы доменных печей доменного цеха ОАО «ММК», Vп,м3 | 1380 | 1380 | 1380 | 1380 | 1380 | 1380 | 2014 | 2014 |
Определить суточную производительность доменного цеха
Определить суточную потребность доменного цеха в агломерате
Эталон
Решение
Определяем суточную производительность доменного цеха (поочередно складывая суточную производительность для каждой доменной печи):
Псут= Vп *Пуд = т чугуна / сут.
Определяем суточную потребность доменного цеха в агломерате, а значит и необходимую суточную производительность агломерационного цеха ОАО «ММК»:
Асут= Псут* А.= тыс.т агломерата/сут
Задание.20 Проверяемые результаты обучения: У1
Текст задания: Рассчитать необходимую суточную производительность коксохимического цеха ОАО «ММК» при среднем расходе кокса на выплавку 1т чугуна, равным 470 кг/т, используя следующие исходные данные:
Полезные объемы доменных печей доменного цеха ОАО «ММК», Vп,м3 : 1,2,4,6,7,8-1380; 9 и 10 – 2014.
№ доменной печи | 1 | 2 | 4 | 6 | 7 | 8 | 9 | 10 |
Удельная производительность доменной печи, Пуд, т/сут | 2,3 | 2,25 | 2,29 | 2,35 | 2,35 | 2,36 | 2,26 | 2,35 |
Полезные объемы доменных печей доменного цеха ОАО «ММК», Vп,м3 | 1380 | 1380 | 1380 | 1380 | 1380 | 1380 | 2014 | 2014 |
Определить суточную производительность доменного цеха
Определить суточную потребность доменного цеха в коксе
Эталон
Решение
Определяем суточную производительность доменного цеха (поочередно складывая суточную производительность для каждой доменной печи):
Псут= Vп *Пуд
Псут = 1380 * 2,3 + 1380 * 2,25 + 1380 * 2,29 + 1380 * 2,3 5+ 1380 * 2,35 + 1380 * 2,36 + 2014 * 2,26 + 2014 * 2,35 = 28466,54 т чугуна / сут.
Определяем суточную потребность доменного цеха в коксе, а значит необходимую суточную производительность коксохимического цеха ОАО «ММК»:
Ксут= Псут* К= 28466,54 * 0,47 = 13379,3 т кокса / сут = 13,4 тыс. т кокса/сут.
Задание.21 Проверяемые результаты обучения: У1
Текст задания: Рассчитать необходимую суточную производительность коксохимического цеха ОАО «ММК» при среднем расходе кокса на выплавку 1т чугуна, равным 470 кг/т, используя следующие исходные данные:
Полезные объемы доменных печей доменного цеха ОАО «ММК», Vп,м3 : 1,2,4,6,7,8-1380; 9 и 10 – 2014.
№ доменной печи | 1 | 2 | 4 | 6 | 7 | 8 | 9 | 10 |
Удельная производительность доменной печи, Пуд, т/сут | 2,32 | 2,36 | 2,40 | 2,31 | 2,30 | 2,29 | 2,27 | 2,28 |
Полезные объемы доменных печей доменного цеха ОАО «ММК», Vп,м3 | 1380 | 1380 | 1380 | 1380 | 1380 | 1380 | 2014 | 2014 |
Определить суточную производительность доменного цеха
Определить суточную потребность доменного цеха в коксе
Эталон
Решение
Определяем суточную производительность доменного цеха (поочередно складывая суточную производительность для каждой доменной печи):
Псут= Vп *Пуд т чугуна / сут.
Определяем суточную потребность доменного цеха в коксе, а значит необходимую суточную производительность коксохимического цеха ОАО «ММК»:
Ксут= Псут* К= тыс. т кокса/сут.
Задание.22 Проверяемые результаты обучения: У1
Текст задания: Рассчитать необходимую суточную производительность коксохимического цеха ОАО «ММК» при среднем расходе кокса на выплавку 1т чугуна, равным 470 кг/т, используя следующие исходные данные:
Полезные объемы доменных печей доменного цеха ОАО «ММК», Vп,м3 : 1,2,4,6,7,8-1380; 9 и 10 – 2014.
№ доменной печи | 1 | 2 | 4 | 6 | 7 | 8 | 9 | 10 |
Удельная производительность доменной печи, Пуд, т/сут | 2,28 | 2,34 | 2,31 | 2,32 | 2,28 | 2,35 | 2,30 | 2,29 |
Полезные объемы доменных печей доменного цеха ОАО «ММК», Vп,м3 | 1380 | 1380 | 1380 | 1380 | 1380 | 1380 | 2014 | 2014 |
Определить суточную производительность доменного цеха
Определить суточную потребность доменного цеха в коксе
Эталон
Решение
Определяем суточную производительность доменного цеха (поочередно складывая суточную производительность для каждой доменной печи):
Псут= Vп *Пуд т чугуна / сут.
Определяем суточную потребность доменного цеха в коксе, а значит необходимую суточную производительность коксохимического цеха ОАО «ММК»:
Ксут= Псут* К= тыс. т кокса/сут.
Задание.23 Проверяемые результаты обучения: У1
Текст задания: Рассчитать производительность одного ручья сортовой МНЛЗ при работе методом «плавку на плавку»
скорость разливки = v, | 3 м/мин |
площадь поперечного сечения слитка= F, | 100х100 мм |
плотность металла =ρм | 7,8 т/м3 |
Эталон
Решение
Производительность МНЛЗ для одного ручья рассчитывается по формуле: G = vF ρм 60
Задание.24 Проверяемые результаты обучения: У1
Текст задания: Рассчитать производительность одного ручья сортовой МНЛЗ при работе методом «плавку на плавку»
скорость разливки = v, | 3,2 м/мин |
площадь поперечного сечения слитка= F, | 124х124 мм |
плотность металла =ρм | 7,8 т/м3 |
Эталон
Решение
Производительность МНЛЗ для одного ручья рассчитывается по формуле: G = vF ρм 60
Задание.25 Проверяемые результаты обучения: У1
Текст задания: Рассчитать производительность одного ручья слябовой МНЛЗ при работе методом «плавку на плавку»
скорость разливки = v, | 1,5 м/мин |
площадь поперечного сечения слитка= F, | 1250х250 мм |
плотность металла =ρм | 7,8 т/м3 |
Эталон
Решение
Производительность МНЛЗ для одного ручья рассчитывается по формуле: G = vF ρм 60
Задание.26 Проверяемые результаты обучения: У1
Текст задания: Рассчитать производительность одного ручья слябовой МНЛЗ при работе методом «плавку на плавку»
скорость разливки = v, | 1,2 м/мин |
площадь поперечного сечения слитка= F, | 750х250 мм |
плотность металла =ρм | 7,8 т/м3 |
Эталон
Решение
Производительность МНЛЗ для одного ручья рассчитывается по формуле: G = vF ρм 60
Задание.27 Проверяемые результаты обучения: У1
Текст задания: Рассчитать количество шихтовых материалов для конвертера садкой 100т , если металлического лома 30%, шлакообразующих 5% от садки печи
Эталон
Решение
Находим % пропорции от садки печи, лом 30т, чугун 65т, шлакообразующих 5т
Задание.28 Проверяемые результаты обучения: У1
Текст задания: Рассчитать количество шихтовых материалов для конвертера садкой 120т , если металлического лома 30%, шлакообразующих 5% от садки печи
Эталон
Решение
Находим % пропорции от садки печи, лом т, чугун т, шлакообразующих т
Задание.29 Проверяемые результаты обучения: У1
Текст задания: Рассчитать количество шихтовых материалов для конвертера садкой 180т , если чугуна 45%, шлакообразующих 5% от садки печи
Эталон
Решение
Находим % пропорции от садки печи, лом т, чугун т, шлакообразующих т
Задание.30 Проверяемые результаты обучения: У1
Текст задания: Рассчитать количество шихтовых материалов для конвертера садкой 380т , если чугуна 55%, шлакообразующих 6% от садки печи
Эталон
Решение
Находим % пропорции от садки печи, лом т, чугун т, шлакообразующих т
Задание.31 Проверяемые результаты обучения: У1
Текст задания: Рассчитать количество шихтовых материалов для конвертера садкой 200т , если чугуна 62%, шлакообразующих 5% от садки печи
Эталон
Решение
Находим % пропорции от садки печи, лом т, чугун т, шлакообразующих т
Задание.32 Проверяемые результаты обучения: У1
Текст задания: Пересчитать на рабочую массу заданный состав мазута
Сг % | Нг % | Ог % | Nг % | Sг % | Aс % | Wр % |
85 | 11,8 | 0,2 | 2,3 | 0,7 | 0,3 | 10 |
1.Ищем содержание золы в рабочей массе:
Ар = Ас (100 - Wр) /100 = 0,3 * 0,897 = 0,296 = 0,3 %
2. Пересчитываем остальные элементы
Ср = Сг (100 -Ар – Wр) / 100 = 85 * 0,897 =76,2 %
Нр = 11,8*0,897 =10,6%
Ор = 0,2*0,897 = 0,18%
Nр = 0,6 *0,897 = 0,54%
Sр = 2,3 * 0,897 =2,1%
Задание.33 Проверяемые результаты обучения: У1
Текст задания: Пересчитать на рабочую массу заданный состав мазута
Сг % | Нг % | Ог % | Nг % | Sг % | Aс % | Wр % |
84 | 10 | 1,0 | 1,6 | 4,0 | 0,3 | 10 |
1.Ищем содержание золы в рабочей массе:
Ар = Ас (100 - Wр) /100 %
2. Пересчитываем остальные элементы
Ср = Сг (100 -Ар – Wр) / 100 %
Нр %; Ор %; Nр %; Sр %
Задание.34 Проверяемые результаты обучения: У1
Текст задания: Пересчитать на рабочую массу заданный состав мазута
Сг % | Нг % | Ог % | Nг % | Sг % | Aс % | Wр % |
84 | 10 | 1,0 | 1,6 | 5,0 | 0,3 | 9 |
1.Ищем содержание золы в рабочей массе:
Ар = Ас (100 - Wр) /100 %
2. Пересчитываем остальные элементы
Ср = Сг (100 -Ар – Wр) / 100 %
Нр %; Ор %; Nр %; Sр %
Задание.35 Проверяемые результаты обучения: У1
Текст задания: Пересчитать на рабочую массу заданный состав мазута
Сг % | Нг % | Ог % | Nг % | Sг % | Aс % | Wр % |
86 | 10 | 1,0 | 1,6 | 3,0 | 0,3 | 9 |
1.Ищем содержание золы в рабочей массе:
Ар = Ас (100 - Wр) /100 %
2. Пересчитываем остальные элементы
Ср = Сг (100 -Ар – Wр) / 100 %
Нр %; Ор %; Nр %; Sр %
3 ИНФОРМАЦИОННЫЕ ИСТОЧНИКИ
Выполнение дифференцированного зачета не предполагает использование информационных источников.