Раздел I.
Введение.
Предисловие из книги по сварке («+»…..(-).
Для общего понятия.
Характеристика материала конструкции.
1. Углеродистую сталь обыкновенного качества изготовляют следующих марок: Ст 0, Ст 1 пс, Ст 1 кп, Ст 1 сп, Ст 2 пс, Ст 2 кп, Ст 2 сп, Ст 3 пс, Ст 3 кп, Ст 3 сп, Ст 3 Гпс, Ст 3 Гсп, Ст 4 кп, Ст 4 пс, Ст 4 сп, Ст 5 пс, Ст 5 сп, Ст 5 Гпс, Ст 6 пс, Ст 6 сп.
Буквы Ст обозначают “Сталь”, цифры - условный номер марки в зависимости от химического состава стали, буквы “кп”, “пс”, “сп” – способ раскисления (“кп” – кипящая, “пс” – полуспокойная, “сп” – спокойная).
Способ раскисления, если он не указан в заказе, устанавливает изготовитель.
3. Химический состав стали по плавочному анализу ковшовой пробы должен соответствовать нормам, указанным в таблице 1.
4. В стали марки Ст 3 сп, предназначенной для дальнейшего передела на листовой прокат, изготовляемый с нормированием ударной вязкости, массовая доля кислоторастворимого алюминия должна быть не менее 0,02%. При раскислении стали титаном алюминий не нормируют, а массовая доля остаточного титана – не более 0,03%.
5. Массовая доля хрома, никеля и меди в стали должна быть не более 0,30% каждого.
5.1. В стали, изготовленной скрап-процессом, допускается массовая доля меди до 0,40%, хрома и никеля – до 0,35% каждого при массовой доле углерода не более 0,20%.
5.2. Для стали марок Ст 3 кп, Ст 3 пс, Ст 3 сп, Ст 3 Гпс и Ст 3 Гсп, изготовленной скрап – процессом, допускается массовая доля меди до 0,40% при массовой доле углерода не более 0,20% и массовой доле хрома, никеля и меди в сумме не более 0,80% (Таб.1).
6. В стали, предназначенной для изготовления сортового, фасонного и листового проката, верхний предел массовой доли марганца увеличивается на 0,2%, кроме стали марок Ст 3 Гпс, Ст 3 Гсп, Ст 5 Гпс.
7. Массовая доля азота в стали – не более 0,008%, а при выплавке в электропечах – не более 0,012%.
8. Массовая доля серы в стали всех марок, кроме Ст 0, должна быть не более 0,050%, фосфора – не более 0,040%, в стали марки Ст 0 серы – не более 0,060%, фосфора – не более 0,070%.
9. Массовая доля мышьяка в стали должна быть не более 0,08%.
В стали, выплавленной на базе керченских руд, массовая доля мышьяка – не более 0,15%, фосфора – не более 0,050%.
10. Предельные отклонения по химическому составу в готовом прокате должны соответствовать приведенным в таблице 2.
11. Химический анализ стали на содержание хрома, никеля, меди, мышьяка. Азота, а в кипящей стали также на содержание кремния, допускается не проводить, если нормы обеспечиваются технологией изготовления.
В стали, выплавленной на базе керченских руд, определение мышьяка обязательно.
12. Методы отбора проб для определения химического состава стали – по ГОСТ 7565-81.
13. Химический анализ стали – по:
ГОСТ 22536.0-87, ГОСТ 22536.1-88, ГОСТ 22536.2-87, ГОСТ 22536.3-88, ГОСТ 22536.4-88,
ГОСТ 22536.5-87, ГОСТ 22536.6-88, ГОСТ 22536.7-88, ГОСТ 22536.8-87, ГОСТ 22536.9-88,
ГОСТ 22536.10-88,ГОСТ 22536.11-87, ГОСТ 27809-88, ГОСТ 17745-72, ГОСТ 18895-81 или другими методами, утвержденными в установленном порядке и обеспечивающими необходимую точность.
При разногласиях между изготовителем и потребителем оценку производят стандартными методами.
14. Для маркировки продукции используют краску цветов, приведенных в таблице 3.
1.2.Требования к сборке конструкции под сварку.
Подготовка металла под сварку.
Подготовка металла под сварку заключается в правке, очистке, разметке, резке и сборке.
Правкой устраняют деформацию прокатной стали. Листовой и сортовой металл правят в холодном состоянии на листоправйльных и углоправйльных вальцах и прессах. Сильно деформированный металл правят в горячем состоянии.
Перенос размеров детали в натуральную величину с чертежа на металл называют разметкой. При этом пользуются инструментом: рулеткой, линейкой, угольником и чертилкой. Проще и быстрее разметка выполняется шаблоном, изготовляемым из тонкого металлического листа. При разметке заготовок учитывается укорачивание их в процессе сварки конструкции. Поэтому предусматривается припуск из расчета 1 мм на каждый поперечный стык и 0,1—0,2 мм на 1 м продольного шва.
При подготовке деталей к сварке применяют преимущественно термическую резку. Механическую резку целесообразно выполнять при заготовке однотипных деталей, главным образом с прямоугольным сечением. Часто кислородную резку, особенно машинную, сочетают со снятием угла скоса кромок. После термической резки иногда проводят механическую обработку по кромкам для удаления науглероженного металла.
Кромки свариваемых деталей подготавливают к сборке в соответствии с ГОСТ 14771-76 УП (сварка в защитных газах; газ-СО2). Номер соединения зависит от толщины металла, вида сварки, пространственного положения и др. При сварке кронштейна используются соединения под индексом Т3 и Н2 (см. чертеж).
Геометрические параметры стыкового шва.
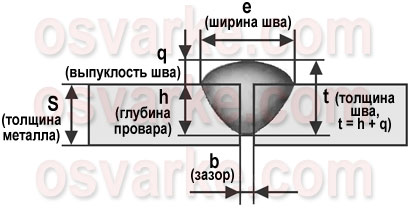
S – толщина свариваемого металла;
e – ширина сварного шва;
q – выпуклость стыкового шва (высота усиления) – наибольшая высота (глубина) между поверхностью сварного шва и уровнем расположения поверхности сваренных деталей;
h – глубина провара (глубина проплавления) – наибольшая глубина расплавления основного металла;
t – толщина шва, t = q+h;
b – зазор.
Основные геометрические параметры углового шва:
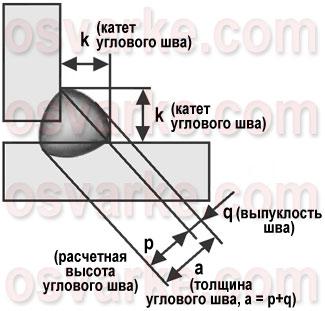
k – катет углового шва – кратчайшее расстояние от поверхности одной из свариваемых деталей до границы углового шва на поверхности второй свариваемой детали;
q – выпуклость шва;
p – расчетная высота углового шва – длина перпендикулярной линии, проведенной из точки наибольшего проплавления в месте сопряжения свариваемых частей к гипотенузе наибольшего прямоугольного треугольника, вписанного во внешнюю часть углового шва;
a – толщина углового шва, a = q+p.
Коэффициент формы шва – отношение ширины шва к его толщине.
Kn = e / t
Значение коэффициента формы шва обычно бывает в пределах от 0,5 до 4. Оптимальным считается значение от 1,2 до 2.
Коэффициент выпуклости шва – отношение ширины шва к его выпуклости.
Ky = e / q
Значение коэффициента выпуклости шва не должно быть более 7–10.
Коэффициент долей основного металла в металле шва:
Kо = Fо / (Fо + Fэ),
где Fо – площадь сечения расплавленного основного металла,
Fэ – площадь сечения наплавленного электродного металла.
Угол разделки кромок выполняется при толщине металла более 3 мм (при сварке алюминия и его сплавов более 4мм), поскольку ее отсутствие (разделки кромок) может привести к непровару по сечению сварного соединения, а также к перегреву и пережогу металла; при отсутствии разделки кромок для обеспечения провара электросварщик должен увеличивать величину сварочного тока.
Зачистка кромок осуществляется металлической щеткой.
Сборка деталей под сварку.
Трудоемкость сборки деталей под сварку составляет около 30% от общей трудоемкости изготовления изделия. Она зависит от ряда условий (серийности производства, типа изделий и др.). Для уменьшения времени сборки, а также для повышения ее точности применяют различные приспособления. Приспособления могут быть предназначены только для сборки деталей под сварку или только для сварки уже собранного изделия (например, для выполнения швов в изделии только в нижнем положении) или пользуются комбинированными сборочно-сварочными приспособлениями.
Основным назначением сборочного оборудования является фиксация и закрепление собираемого сварного узла в заданном положении. Для этой цели применяются специальные узлы и установки. Установочные и закрепляющие элементы сборочного оборудования. К первым относятся упоры, опоры, призмы, фиксаторы, шаблоны и домкраты (рис. 1). Закрепляющими элементами являются прижимы, которые могут быть ручными и механизированными. В качестве привода механизированных прижимов чаще всего применяются пневматические и гидравлические системы. В некоторых случаях прижим объединяют с упором или фиксатором и выполняют в виде комплексного узла. Установочные и зажимные элементы могут быть съемными и регулируемыми. Из отдельных элементов могут быть собраны приспособления и установки, в частности кондукторы и стенды. Указанные установки применяют для сборки плосколистовых и коробчатых конструкций, а также цилиндрических обечаек. При сборке осуществляют следующие операции; устанавливают все необходимые элементы конструкции на соответствующих местах с заданными зазорами и закрепляют их, совмещают кромки свариваемых элементов, при необходимости производят прихватки. В результате получают конструкцию, готовую для сварки. Для обеспечения необходимой точности сборки, сокращения времени на разметку и проверку собранной конструкции, а также облегчения процесса сварки (возможность выполнения швов в нижнем положении) целесообразно использовать при изготовлении фундамента под механизм специального кондуктора.
Изделия чаще собирают на сварочных прихватках. Сварочные прихватки представляют собой неполноценные короткие швы с поперечным сечением до 1/3 сечения полного шва. Длина прихватки от 20 до 100 мм в зависимости от толщины свариваемых листов и длины шва; расстояние между прихватками в зависимости от различных условий достигает 1м. Прихватки придают изделию жесткость и препятствуют перемещению деталей, что может привести к трещинам в прихватках при их охлаждении. Чем больше толщина свариваемых листов, тем больше растягивающая усадочная сила в прихватках и больше возможность образования трещин. Поэтому сборку на сварочных прихватках применяют для конструкций из листов небольшой толщины (до 6 — 8мм). При значительной толщине листов необходимо обеспечить податливость деталей и сборку изделия выполняют на механических приспособлениях. После того как кронштейн собрана её надо установить в кантователь (устройство, облегчающее установку собранной конструкции в удобноу для сварки положение) для последующей обварки.
Точность сборки проверяют с помощью специального инструмента.
Рис2.Инструмент для проверки качества сборки и сварки.
Цифровой шаблон Ушерова-Маршака
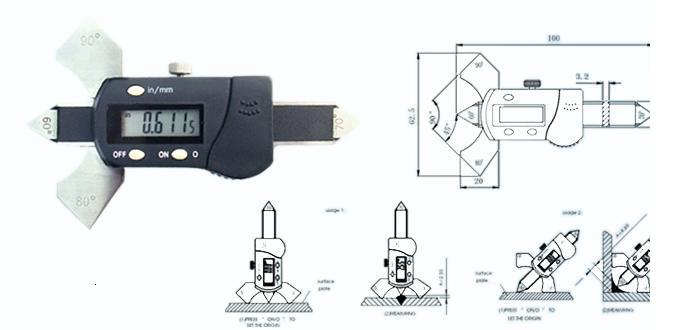
Назначение:
измерения угла скоса разделки кромки;
измерения высоты катета углового шва;
измерения высоты валика усиления и выпуклости корня шва стыкового сварного соединения;
измерения зазора в соединении при подготовке деталей к сварке.
Технические параметры:
диапазон измерения - 0-20 мм
цена деления - 0,01 мм
питание – одна батарея типа SR 44 (1,55 В)
габаритные размеры - 100х64х14 мм
размеры углов - 60 / 70 / 80 / 90 градусов
Раздел II.
Специальная часть.
2.1.Технология полуавтоматической сварки в защитном газе кронштейна из стали Ст1пс.
При сварке плавящимся электродом в защитном газе (рисунок) в зону дуги, горящей между плавящимся электродом (сварочной проволокой) и изделием через сопло подаётся защитный газ, защищающий металл сварочной ванны, капли электродного металла и закристаллизовавшийся металл от воздействия активных газов атмосферы. Теплотой дуги расплавляются кромки свариваемого изделия и электродная (сварочная) проволока. Расплавленный металл сварочной ванны, кристаллизуясь, образует сварной шов.
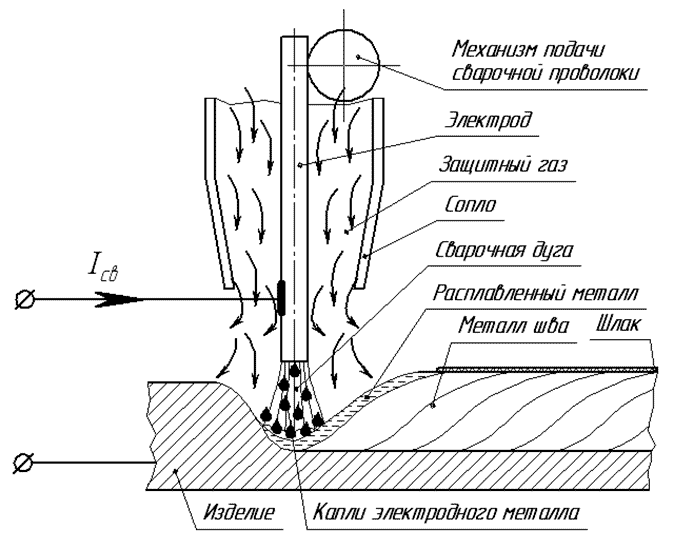
Рисунок . Схема сварки в защитных газах
При сварке в защитных газах плавящимся электродом в качестве электродного металла применяют сварочную проволоку близкую по химическому составу к основному металлу. Выбор защитного газа определяется его инертностью к свариваемому металлу, либо активностью, способствующей рафинации металла сварочной ванны. Для сварки цветных металлов и сплавов на их основе применяют инертные одноатомные газы (аргон, гелий и их смеси). Для сварки меди и кобальта можно применить азот. Для сварки сталей различных классов применяют углекислый газ, но так как углекислый газ участвует в металлургических процессах, способствуя угару легирующих компонентов и компонентов - раскислителей (кремния, марганца), то сварочную проволоку следует выбрать с повышенным их содержанием. В ряде случаев целесообразно применять смесь инертных и активных газов, чтобы повысить устойчивость дуги, улучшить формирование шва, воздействовать на его геометрические параметры, уменьшить разбрызгивание.
Сварку в защитных газах плавящимся электродом ведут на постоянном токе обратной полярности, т.к. на переменном токе из-за сильного охлаждения столба дуги защитным газом, дуга может прерываться. Скорость подачи сварочной проволоки определяет силу сварочного тока.
Для сварки в защитных газах плавящимся электродом характерно высокий процент потерь электродного металла вследствие угара и разбрызгивания.
Достоинства способа:
Повышенная производительность (по сравнению с дуговой сваркой покрытыми электродами);
Отсутствуют потери на огарки, устранены затраты времени на смену электродов;
Надёжная защита зоны сварки;
Минимальная чувствительность к образованию оксидов;
Отсутствие шлаковой корки;
Возможность сварки во всех пространственных положениях.
Недостатки способа:
Большие потери электродного металла на угар и разбрызгивание (на угар элементов 5-7%, при разбрызгивании от 10 до 30%);
Мощное излучение дуги;
Ограничение по сварочному току;
Сварка возможна только на постоянном токе.
Области применения:
Сварка тонколистового металла и металла средних толщин (до 20мм);
Возможность сварки сталей всех классов, цветных металлов и сплавов, разнородных металлов.
2.2.Основные характеристики сварочных материалов, оборудования и приспособлений. Диоксид углерода (СО2).
Диоксид углерода |
|
Другие названия | углекислый газ, углекислота, сухой лед(твердый) |
Формула | CO2 |
Молярная масса | 44.0095(14) г/моль |
В твердом виде | сухой лед |
Вид | бесцветный газ |
Номер CAS | [124-38-9] |
Свойства |
Плотность и фазовое состояние | 1.98 кг/м³, при н.у.; 771 кг/м³, жидкий; 1512 кг/м³, твёрдый |
Растворимость в воде | 1.45 кг/м³ |
Удельная теплота плавления | 25.13 кДж/моль |
Точка плавления | −57 °C (216 K), под давлением |
Точка кипения | −78 °C (195 K), возгоняется |
Константа диссоциации кислоты (pKa) | 6.35 and 10.33 |
Вязкость | 0.07 пз при −78 °C |
Строение |
Форма молекулы | линейная |
Кристаллическая решётка | кварцевидная |
Дипольный момент | ноль |
Техника безопасности |
MSDS | External MSDS |
Главные опасности | удушающее, раздражающее |
| |
| |
S-phrases | S9, S23, S36 (ж) |
RTECS number | FF6400000 |
|
Подбор сварочной проволоки при сварке в углекислом газе.
В зоне сварки протекает ряд химических реакций, в том числе реакция между низшим оксидом железа и углеродом, находящимся в зоне сварки.
Образование газа СО и потом СО2 приводит к образованию пор. Кроме того, поры при сварке в углекислом газе могут быть следствием влаги и влияния азота воздуха.
Для подавления образования СО в состав сварочной проволоки вводят повышенное количество марганца и кремния (марки Св-08Г2С, Св-08ГС и др.). При сварке низкоуглеродистых сталей содержание в металле шва кремния больше 0,2% и марганца более 0,4% препятствует образованию пор.
Для сварки конструкции будет использована сварочная проволока марки Св-08ГС, содержащая 0,08% углерода, марганца и кремния до 1% каждого.
Сварочное оборудование
Устройство сварочного трансформатора.
Сварочный трансформатор преобразует переменный ток одного напряжения в переменный ток другого напряжения той же частоты и служит для питания сварочной дуги. Трансформатор имеет стальной сердечник (магнитопровод) и две изолированные обмотки. Обмотка, подключенная к сети, называется первичной, а обмотка, подключенная к электрододержателю и свариваемому изделию – вторичной. Для надежного зажигания дуги вторичное напряжение сварочных трансформаторов должно быть не менее 60 — 65 В; напряжение дуги при ручной сварке обычно не превышает 20 — 30 В.Трансформатор имеет винт с рукояткою для перемещения подвижной обмотки. Сварочный ток регулируют изменением расстояния между первичной и вторичной обмотками.
Устройство сварочного выпрямителя.
Свойство некоторых материалов пропускать электрический ток в одном направлении используется в сварочной технике для преобразования переменного тока в пульсирующий постоянный ток. Материалами выпрямительного элемента (вентиля) служат селен и кремний. Сварочные выпрямители выполняют в большинстве случаев по трехфазной схеме, преимущества которой заключаются в большом числе пульсаций напряжения и более равномерной загрузке трехфазной сети.
Одним из распространенных является сварочный выпрямитель ВД-306. Он состоит из понижающего трехфазного трансформатора с подвижной обмоткой, блока вентилей и устройства, регулирующего сварочный ток. Трансформатор выпрямителя имеет два диапазона регулирования сварочного тока: малых токов — при включении обмоток трансформатора звездой и больших токов — при включении треугольником. Первичная обмотка сварочного трансформатора выпрямителя ВД-306 подвижная, катушки вторичной обмотки закреплены в верхней части сердечника. Сварочный выпрямитель имеет три панели с зажимами для присоединения к ним электрических проводов. Две из них предназначены для подключения проводов сети и сварочных проводов, третья — для переключения диапазонов сварочного тока.
Сварка пульсирующим постоянным током может производиться на прямой и обратной полярности. При прямой полярности изделие присоединяется к зажиму «+» выпрямителя, а электрод — к зажиму «-»; при обратной полярности и наоборот.
Включение сварочного выпрямителя ВД-306 осуществляется пакетным выключателем ПВ.
Устройство сварочного преобразователя
Сварочный преобразователь состоит из сварочного генератора постоянного тока и приводного электродвигателя, размещенных обычно в общем корпусе и на общем валу. Приводной электродвигатель преобразует электрическую энергию переменного тока в механическую, а сварочный генератор преобразует механическую энергию постоянного тока в электрическую энергию постоянного тока, питающую сварочную дугу. Для вращения генератора в сварочных генераторах применяется трехфазный асинхронный электродвигатель. Сварочный генератор постоянного тока состоит из статора с магнитными полюсами и якоря с обмоткой и коллектором. Регулирование сварочного тока производится реостатом, включенным в обмотку магнитных полюсов.
Для сварки кронштейна целесообразно применить универсальный выпрямитель ВДУ-506С, так как он позволяет работать и полуавтоматической сваркой.
Выпрямитель сварочный ВДУ-506С
| Описание ![]() Предназначен для комплектации полуавтоматов и автоматов дуговой сварки, а так же для ручной дуговой сварки покрытыми электродами на постоянном токе (режим ММА). ВДУ-506С в комплекте с полуавтоматом предназначен для полуавтоматической сварки плавящейся электродной проволокой в среде защитных газов на постоянном токе (режим МИГ/МАГ). Выпрямитель ВДУ-506С является полным аналогом ранее выпускаемых выпрямителей типа ВДУ-506, ПРЕИМУЩЕСТВА: Плавная регулировка сварочного тока в режиме ММА и сварочного напряжения в режиме МИГ/МАГ. Универсальный, так как имеет два вида внешних характеристик: жесткие и падающие. Легкое зажигание и устойчивое горение дуги. Наличие термозащиты от перегрузки. Дистанционное регулирование сварочных параметров с помощью пульта. Наличие розетки 36В для питания подогревателя газа. Класс изоляции Н по ГОСТ 8865-70. Быстроразъемные, безопасные токовые разъемы. Надежность работы и простота обслуживания. По заказу потребителей возможна поставка выпрямителей с комплектом колес для удобства перемещения. Режим сварки | ММА | МИГ/МАГ | Номинальный сварочный ток, А (при ПВ, %) | 500 (60%) | 390 (100%) | Пределы регулирования сварочного тока, А | 50-500 | 60-500 | Номинальное рабочее напряжение, В | 46 | 50 | |
Сварочный универсальный выпрямитель ВДУ-506С предназначен для ручной дуговой сварки покрытыми электродами на постоянном токе, комплектации сварочных полуавтоматов и автоматов для сварки изделий из стали в среде защитных газов на постоянном токе. Сварочный выпрямитель ВДУ-506С – регулируемый тиристорный выпрямитель с жесткой или падающей внешней характеристикой, ВДУ-506С широко известен и имеет одну из самых высоких сварочных характеристик в своем классе. Отличие от известных версий сварочных выпрямителей ВДУ-506 и ВДУ-505 заключается в том, что сварочный выпрямитель ВДУ-506С-5 в режиме полуавтоматической сварки имеет специальную комбинированную вольтамперную характеристику, обеспечивающую уменьшение разбрызгивания в 5 раз, увеличение производительности на 15%, улучшенное качество формирования сварного шва. В комплекте с полуавтоматом сварочным ПДГО-510-5, со стабилизацией скорости подачи сварочной проволоки и возможностью удаления подающего механизма от сварочного выпрямителя на расстояние до 50м, оптимален для цеховых условий при сварке на токах дуги до 450А (ПВ=100%). Сварочные свойства выпрямителя ВДУ-506С-5 приближены к лучшим инверторным источникам при сварке в смесях газов, а при сварке в углекислом газе он превосходит их. Обеспечивает эффективную сварку в вертикальном пространственном положении как «снизу-вверх», так и «сверху-вниз» с формированием обратного валика. Обеспечивает разбрызгивание электродного металла на уровне 3,5% в углекислом газе и не более 2% при сварке в смесях газов.
Преимущества:
Плавное регулирование сварочного тока в режиме ММА и сварочного напряжения в режиме МIG/MAG;
Специальная комбинированная внешняя вольтамперная характеристика;
Возможность предустановки напряжения на дуге при полуавтоматической сварке;
Наличие розетки 36 В для питания подогревателя газа;
Защита от тепловой перегрузки;
Быстросъемные, безопасные токовые разъемы;
Класс изоляции Н;
Принудительное охлаждение.
Устройство полуавтомата
В сварочном автомате две основные операции сварки автоматизированы: подача сварочной проволоки в зону дуги и перемещение дуги по линии шва; в полуавтомате механизирована лишь одна операция — подача электродной проволоки в дугу, а перемещение дуги для образования, шва производится сварщиком вручную (рис. 127). Автоматическая подача проволоки с катушки 1 осуществляется подающим механизмом 2, состоящим из электродвигателя М переменного или постоянного тока, коробки скоростей ведущего 7 и прижимного ролика 6. Проволока 8 подается роликами с постоянной заданной скоростью через внутренний канал гибкого шланга 3, держатель 4 и наконечник 5. Сварщик держит горелку и вручную перемещает ее по шву.
Одйой из основных частей полуавтомата является шланг 3, состоящий из проволочной спиралис оплеткой и резиновой оболочкой, по внутреннему каналу которой проходит электродная проволока. Сварочный ток, защитный газ и охлаждающая вода подводятся отдельно. В комбинированных шлангах кроме электродной проволоки в одной оболочке проходят токопроводящий провод, провода цепи управления, защитный газ и охлаждающая вода. Комбинированный гибкий шланг имеет большую массу, сварщику трудно управлять им. Современные полуавтоматы снабжаются автономными шлангами.
Длина шланга составляет не более 3,5 м. На горелке находится кнопка включения подающего механизма.
Подача электродной проволоки вперед и назад осуществляется переключением пакетного переключателя.
В полуавтоматах для сварки в защитном газе одновременно с пуском электродвигателя срабатывает реле для автоматического включения газового клапана. При этом начинается подача электродной проволоки и газа. При размыкании сварочной цепи реле обесточивается и размыкает свои контакты. Подача электродной проволоки и газа прекращается.
Электродвигатель для подачи сварочной проволоки подключается чаще всего к источнику питания сварочной дуги или сети через понижающий трансформатор 380/36 В.
Полуавтоматы подразделяют по назначению на стационарные, где в одном корпусе смонтированы все части аппарата вместе с источником питания; передвижные, где механизм подачи и катушка с проволокой размещены на тележке; переносные, где механизм подачи и катушка с проволокой максимально облегчены ; ранцевого типа — для сварки в условиях монтажа и специализированные — для выполнения определенных операций.
Расположение подающего механизма. Для полуавтоматической сварки применяют шланговые полуавтоматы толкающего типа (рис.1) и тянущего типа (рис.2). Тип полуавтомата определяется местом расположения электродвигателя. Сопротивление прохождению проволоки зависит от количества изгибов шланга, его длины и материала трущихся поверхностей проволоки и канала.
Это сопротивление при работе полуавтомата меняется, что ведет к нарушению равномерности подачи проволоки и стабильности процесса сварки. Сопротивление проталкиванию проволоки может настолько увеличиться, что двигатель механизма подачи остановится или начнется пробуксовка проволоки в подающих роликах.
Для порошковых проволок из алюминия и титана, имеющих повышенный коэффициент трения, сопротивление проталкиванию намного больше, чем для стальных проволок сплошного сечения. Поэтому для снижения сопротивления проталкиванию применяют спирали, изготовленные из материалов с малым коэффициентом трения или обычные спирали, смазанные нейтральной смазкой (например, дисульфидом молибдена, снижающим сопротивление проталкиванию в 1,5 — 2 раза). Применение спиралей из бронзы снижает сопротивление в 2 — 3 раза по сравнению со сталью, а в трубках из фторопласта — в 6 — 10 раз.
Для мягких проволок из алюминия и его сплавов или порошковой проволоки с высоким коэффициентом трения (за счет неровностей поверхности проволоки), а также для проволок малого диаметра (менее 0,8 мм), способных сминаться в канале, полуавтоматы толкающего типа неприменимы.
В этих случаях применяют полуавтоматы тянущего типа, механизм подачи которых расположен в горелке. Однако длина шлангов этих полуавтоматов ограничивается малой мощностью электродвигателя (до 100 Вт) и не превышает 1 м. Более длинные шланги требуют увеличенной мощности и массы двигателей, а следовательно, большой массы горелки.
В полуавтоматах со шлангами более 5 м применяются механизмы подачи тянуще-толкающего типа, в которых имеется толкающий механизм с двигателем, расположенный рядом с катушкой электродной проволоки, и тянущий механизм с двигателем, расположенный в горелке. Это значительно утяжеляет горелку, но устраняет неравномерность подачи проволоки в зону сварки.
Особенности в конструкциях полуавтоматов.
Сварочные полуавтоматы могут быть использованы как для сварки, так и для наплавочных работ. Различают полуавтоматы универсальные и специализированные.
Для сварки алюминия и его сплавов можно применять полуавтомат типа ПДА или ПДГО.
Особенностью конструкции полуавтоматов ПДА-300 является наличие толкающе-тянущей системы подачи алюминиевой электродной проволоки. В полуавтомате имеются стандартный подающий механизм и вспомогательный тянущий механизм, состоящий из малогабаритного двигателя с редуктором и падающими роликами, расположенными в пластмассовой головке полуавтомата. Вспомогательный механизм создает натяжение электродной проволоки, облегчает прохождение ее через спираль шланга. Полуавтомат рассчитан на сварку током до 300 а электродной проволокой диаметром от 1,6 до 2 мм. Скорость подави электродной про
волоки от 1,5 до 7,5 м/мин.
Фото | Характеристики | Значение |
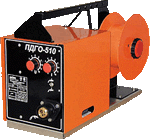 | Напряжение | ~27 В |
Номинальный сварочный ток | 500 А |
Скорость подачи электродной проволоки | 120-1100 м/ч |
Количество пар подающих роликов | 4 шт |
Диаметр электродной проволоки: стальная порошковая | 1,2-1,6 мм 1,6-2,0 мм |
Тип разъема сварочной горелки | евроразъем |
Размер сварочной кассеты | 300 мм |
Вместимость сварочной кассеты | 15 кг |
Габаритные размеры | 252х642х411 мм |
Масса блока управления | 18 кг |
Описание.
Сварочный полуавтомат ПДГО-510 предназначен для полуавтоматической сварки сплошной и порошковой проволокой на постоянном токе в среде защитных газов в комплекте с источниками для МИГ/МАГ сварки.
Сварочный полуавтомат ПДГО-510 - подающий механизм полузакрытого типа.
Механизм подачи сварочной проволоки ПДГО-510 предназначен для работы с выпрямителем сварочным ВДУ-506С и др. сварочными выпрямителями, имеющими жесткую или комбинированную вольт-амперную характеристику.
Внутри механизма подачи сварочной проволоки ПДГО-510 установлен 4-х роликовый редукторный привод с двумя прижимными регулировочными устройствами, электромагнитный клапан, плата управления сварочным процессом и газовый тракт. Органы управления сварочным режимом расположены на лицевой панели (резисторы регулировки скорости подачи сварочной проволоки и напряжения на дуге, переключатель двухтактный-четырехтактный режим).
На плате механизма подачи сварочной проволоки ПДГО-510 имеется регулировка времени отключения источника после прекращения подачи сварочной проволоки, времени продувки газа до и после сварки, регулировка времени выхода сварочного тока на установленный режим («мягкий старт»). Снаружи на отдельном кронштейне расположена кассета и тормозное устройство.
Сварочный полуавтомат ПДГО-510 может быть использован при работе непосредственно с полной бухтой электродной проволоки, уложенной на разматывающее устройство. Платы управления обеспечивает в отличие от других механизмов, стабилизацию скорости подачи сварочной проволоки и обратную связь по напряжению на двигателе подающего механизма.
Основные преимущества полуавтомата сварочного ПДГО-510:
Плавная регулировка выходного напряжения сварочного источника и скорости подачи электродной проволоки с подающего механизма;
Обеспечивает стабилизацию скорости подачи сварочной проволоки и обратную связь по напряжению на двигателе подачи сварочной проволоки, что позволяет производить качественную сварку на расстоянии до 50 метров от сварочного источника;
Стабильная скорость подачи сварочной проволоки при длине шлейфа горелки 3...5 м и изгибах шлейфа;
Автоматическое управление газовым трактом, сварочным источником и подающим механизмом посредством кнопки на горелке;
Два режима сварки: «Длинные швы» (4-х тактный режим) или «короткие швы» (2-х тактный режим);
Наличие регулируемых режимов «Мягкий старт» и «Время растяжки дуги»;
Продувка газа до и после сварки;
Наличие режима заправки проволоки и режима проверки подачи газа;
Применение 4-х роликового механизма подачи, обеспечивает повышенное тяговое усилие и возможность работы с горелками длиной до 5м;
Универсальное тормозное устройство, соответствует европейскому стандарту;
Зубчатое зацепление подающего и прижимного роликов;
Таррирование усилие прижимного устройства;
Комплектуется немецкой горелкой фирмы «Binzel»;
Подключение горелки через евроразъем;
Обеспечивает установку кассеты (диаметром 300мм) с проволокой весом 15 кг;
Подача сварочной проволоки может производиться непосредственно с кассеты или с бухты, уложенной на разматывающее устройство;
Подключается к любому типу сварочных источников для МИГ/МАГ сварки производства «Фирмы СЭЛМА»;
Подключается к любому типу сварочных источников других производителей через блок питания БП-02.
Подающий механизм обеспечивает:
Плавную регулировку скорости подачи сварочной проволоки и напряжения на дуге;
Управление газовым клапаном, подающим механизмом и сварочным источником от кнопки на горелке;
Стабилизацию скорости подачи сварочной проволоки и обратную связь по напряжению на двигателе подачи сварочной проволоки, что обеспечивает сварку на расстояниях от источника питания до подающего механизма до 50м, возможность сварки в сложных пространственных положениях и при значительных изгибах шланга горелки;
Возможность сварки сплошной и порошковой проволокой в защитных газах с любыми выпрямителями (ВДУ-506С и др.), имеющими жесткую или комбинированную вольт-амперную характеристику;
Стыковка с выпрямитлем ВД-306ДК, производится через блок БП-01, с выпрямителем ВД-506ДК - напрямую;
Регулировку вылета сварочной проволоки, времени продувки защитного газа до и после сварки, времени выхода сварочного тока на установленный режим.
Газовая аппаратура.
Для полуавтоматической сварки в СО2 используется газовая аппаратура состоящая из:
баллона с газом - транспортировка и хранение защитного газа;
-
подогревателя газа – предотвращение замерзания редуктора;
-
осушитель газа – удаление влаги;
-
редуктора – регулировка и поддержание рабочего давления газа;
-
редуктора – измерение давления газа в баллоне и рабочего давления;
-
ротаметра – установка расхода газа.
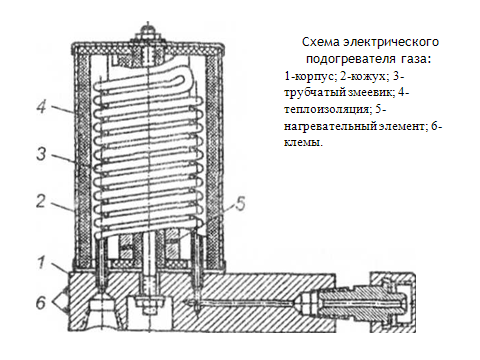



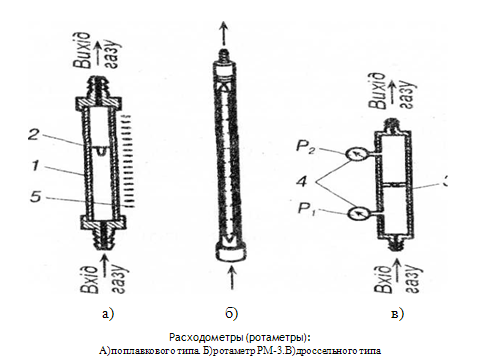
Баллоны для СО2
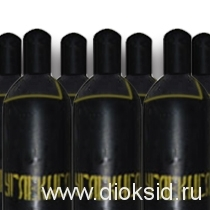
2.3Выбор режима сварки.
На степень окисления металла и образования пор влияют технологические условия сварки (длина дуги, род и полярность тока, диаметр проволоки и плотность тока на электроде). Сварка на постоянном токе обратной полярности дает меньшее окисление и более высокое качество шва, чем на прямой полярности. При сварке проволокой диаметром 0,3 — 1,2 мм, выполняемой с высокими скоростями подачи проволоки в дугу, происходит значительно меньшее окисление элементов, чем при сварке проволокой диаметром 1,6 — 2мм с малыми скоростями подачи проволоки.
Плотность тока на электроде при сварке в углекислом газе должна быть не ниже 80 А/мм2. При таком режиме потери на разбрызгивание электродного металла не превышают 10—15%.
Сила тока можно определить из таблицы: Iсв=120-180А.
При полуавтоматической сварке большое значение играет вылет электродной проволоки (расстояние между точкой подвода сварочного тока к проволоке и изделием). Вылет большой - увеличенное разбрызгивание, маленький - подгорает мундштук.
Скорость подачи проволоки должна соответствовать силе тока, т.е. если скорость маленькая, то проволока будет быстро плавиться и дуга потухнет, скорость большая – короткое замыкание (проволока воткнётся в сварочную ванну).
Диаметр проволоки, мм | 0,5 | 0,8 | 1,0 | 1,2 | 1,6 | 2,0 |
Вылет, мм | 5-8 | 6-12 | 7-13 | 8-15 | 13-20 | 15-25 |
Скорость подачи проволоки сварщик определяет сам.
Расход углекислого газа устанавливается так, чтобы обеспечить полную защиту металла шва от воздействия атмосферного воздуха. При сварке толстых изделий сварочными токами 500—1000 А расход газа достигает 15— 20 л/мин.
2.4.Техника полуавтоматической сварки в защитном газе.
Полуавтоматическую сварку можно вести углом вперед, перемещая горелку справа налево, и углом назад, перемещая горелку слева направо. При сварке углом вперед глубина проплавления меньше, наплавляемый валик получается широкий. Такой метод применяют при сварке тонкостенных изделий и при сварке сталей, склонных к образованию закалочных структур. При сварке углом назад глубина проплавления больше, а ширина валика несколько уменьшается. Угол наклона горелки относительно вертикальной оси составляет 5—15°.
Перед началом сварки следует отрегулировать расход углекислого газа и только спустя 30—40 секунд возбудить дугу и приступить к сварке. Это необходимо, чтобы газ вытеснил воздух из шлангов и каналов сварочной горелки.
В процессе сварки электроду сообщается такое движение, чтобы получилось хорошее заполнение металлом разделки свариваемых кромок и удовлетворительное формирование наплавляемого валика. Эти движения аналогичны движениям электрода при ручной дуговой сварке качественными электродами. Рекомендуется для снижения опасности образования трещин первый слой сваривать при малом сварочном токе. Заканчивать шов следует заполнением кратера металлом. Затем прекращается подача электродной проволоки, и ток выключается. Подача газа на заваренный кратер продолжается до полного затвердевания металла.
Колебательные движения горелки аналогичны сварке покрытыми электродами.
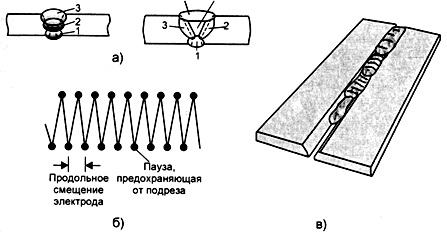
Сварка стыкового соединения со скосом кромок в нижнем положении: a - порядок наложения слоев; б - траектория движения электрода при выполнении последнего прохода; в - сварное соединение
Положение электрода при наплавке валиков с поперечными колебаниями
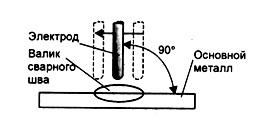
2.5.Контроль качества сварки, возможные дефекты и способы их исправления.
Очередность контроля.
Чтобы обеспечить высокое качество и надежность сварных соединений, необходимо выполнить предварительный контроль, пооперационный контроль и контроль готовых сварных соединений.
При предварительном контроле следует проверить:
сварочные материалы (электроды, сварочную проволоку, флюсы и газы) и материал для дефектоскопии;
сварочное оборудование, сборочно-сварочные приспособления, контрольно-измерительные приборы, инструмент, аппаратуру и приборы для проведения дефектоскопии.
Обязательно должна быть проверена квалификация сварщиков, контролеров-дефектоскопистов и инженерно-технических работников, занимающихся вопросами контроля сварных швов.
Пооперационный контроль включает:
контроль подготовки деталей под сварку, режимов сварки и правильности наложения швов;
контроль в процессе сварки за состоянием оборудования, качеством и соответствием присадочных материалов и контрольно-измерительных приборов.
Контроль готовых сварных сое д и нений выполняют после выполнения термической обработки (если она предусмотрена требованиями технологического процесса).
Способы контроля сварочных материалов и сварных соединений.
При выполнении сварочных работ применяют различные способы контроля сварочных материалов и сварных соединений. Эти способы делятся на две группы:
-разрушающие (когда сварное соединение приходится разрушать);
-неразрушающие (когда сварное соединение не выводится из строя).
В основном на практике стараются применять неразрушающие способы контроля, однако некоторую часть сварных соединений целесообразно подвергать разрушению для получения более надежной и достоверной информации о свойствах выполненных соединений.
Внешний осмотр и замер размеров швов.
Этот вид контроля является необходимым и наиболее распространенным при сварке. Внешний осмотр может быть выполнен невооруженным глазом и с помощью увеличительного стекла. Перед внешним осмотром сварные швы должны быть тщательно очищены от шлака, а если необходимо, то и протравлены. Осматривать детали следует как после прихваток, так и после наложения каждого валика. Размеры швов замеряют специальными шаблонами и измерительными приборами непосредственно после сварки.
Внешним осмотром выявляют излом или неперпендикулярность осей соединенных элементов, смещение кромок соединяемых элементов, несоответствие размеров и формы швов (по высоте, катету и ширине шва, по равномерности усиления, чешуйчатости и т. п.), трещины всех видов и на правлений, наплывы, подрезы, прожоги, незаваренные кратеры, непровары, пористость и другие дефекты, отсутствие плавных переходов от одного сечения к другому, несоответствие общих геометрических размеров сварного узла (изделия) требованиям чертежей и технических условий, отсутствие клейм сварщиков или несоответствие клеймения установленным требованиям.
Осматривать необходимо все без исключения сварные соединения. Внешний осмотр и измерение сварных соединений осуществляют в условиях достаточной освещенности объекта контроля.
Различают пассивные и активные акустические методы контроля сварных соединений. Пассивные методы основаны на исследовании упругих волн, возникающих в контролируемом изделии во время или по окончании технологического процесса, или при нагружении, в частности в момент образования или развития несплошностей. К ним относятся методы контроля, использующие акустическую эмиссию, а также шумо- и вибродиагностика. Активные методы основаны на исследовании распространения колебаний специально вводимых в контролируемое изделие.
Существуют и другие способы выявления внутренних дефектов:
-радиационные виды контроля;
-магнитные виды контроля;
-контроль непроницаемости швов.
ДЕФЕКТЫ СВАРКИ ПЛАВЛЕНИЕМ.
Дефекты сварки плавлением классифицируют по месту расположения на поверхностные, внутренние и сквозные.
К поверхностным дефектам относят:
а) непровары в корне шва; б) подрезы; в) наплывы; г) кратеры;
д) занижение (ослабление) лицевой поверхности шва;
е) вогнутость корня шва;
ж) смещение сваренных кромок;
з) резкий переход от шва к основному металлу (неправильное сопряжение сварного шва);
и) брызги металла; к) поверхностное окисление; л) поверхностные трещины.
К внутренним дефектам относят:
а) поры; б) включения; в) оксидные плёнки; г) внутренние трещины;
д) непровары по кромке с основным металлом и между отдельными слоями;
е) свищи.
К сквозным дефектам относят трещины и прожоги.
Помимо дефектов – несплошностей к дефектам сварки плавлением относят: искажение формы соединения, связанное с деформацией, и несоответствие геометрических размеров сварного шва или точек, регламентированным значениям, установленным НТД (нормативно-технической документацией).
Общие сведения о дефектах сварки плавлением приведены в таблице.
Дефекты | Определение дефекта (ГОСТ 2601-84) | Причины образования дефектов | Особенности дефекта и способы исправления и исключения его образования |
Непровары - в корне шва; - между отдельными слоями; - по кромне с основным металлом; | Дефект в виде местного несплавления вследствие неполного расплавления свариваемых кромок или поверхностей ранее выполненных валиков | - малая погонная энергия; - неудовлетворительная подготовка поверхностей; - неправильная форма разделки; - большая величина притупления; - малые зазоры; - смещение электрода; - некачественная зачистка шва после выполнения прохода | Наиболее характерно при алюминиевых сплавах и под флюсом; Является концентратором напряжения. Трудно выявляются в кольцевых швах. Исправление—подварка с удалением корневой части. |
Прожоги - одиночные; - протяженные; - дискретные | Дефект в виде сквозного отв ерстия, образовавшийся в результате вытекания сварочной ванны | - большая погонная энергия; - увеличенный зазор; - малая величина притупления; - большое смещение кромок; - коробление кромок и отставание их от подкладки при сварке | Характерны при сварке тонкостенных элементов, а так же первого (корневого) шва при многослойной сварке. Как правило, брак, если возможно выполняют подварку. |
Кратеры | Дефекты в виде воронкообразного углубления, образовавшегося в результате внезапного прекращения сварки или быстрого отключения сварочного тока | - нарушение техники сварки | Ослабление сечения. Сопровождается усадкой и трещинами усадочного происхождения. Концентратор напряжения. Исправление – удаление дефектного участка и заварка. При автоматической сварке используют технологические планки для вывода кратера или плавное отключение тока |
Наплывы на сварном соединении | Дефект в виде натекания жидкого металла на поверхность основного или ранее выполненного валика и несплавление с ним | - большой ток; - большая скорость сварки; - длинная дуга (повышенное напряжение); - смещение электрода; - большая скорость подачи присадочной проволоки; - наклон электрода (неправильное ведение) | Возникает с лицевой стороны соединения или обратной стороны из-за некачественного поджатия к подкладке и , как правило, при сварке в горизонтальном и вертикальном положении, а также на спуск и на подъем. Концентратор напряжения. Исправление – зашлифовка.. |
Подрезы зоны сплавления. -односторонний; -двухсторонний | Дефекты в виде протяженного углубления вдоль линии сплавления основного металла и шва | - большой ток; - большая скорость; - длинная дуга; - наклон электрода (неправильное ведение) | Как правило, возникает при сварке концентрированными источниками в режиме глубокого проплавления, а также при сварке угловых швов. Концентратор напряжения. Ослабление сечения. Исправление – заглаживание дугой при неглубоких подрезах и подварка при глубоких |
Неплавное сопряжение сварного шва | Дефект в виде резкого перехода поверхности сварного шва к основному металлу | - несоблюдение техники сварки; - большая скорость подачи присадочной проволоки. | Концентратор напряжения. Возникает в угловых швах. Исправление – зашлифовка или прокатка роликами. |
Брызги металла. | Дефект в виде затвердевших капель жидкости металла на поверхности сварного соединения. | - несоблюдение техники сварки; - длинная дега. | Возникает при сварке толстопокрытыми электродами, в СО2 или электролучевой сварке с глубоким проплавлением. Исправление - вырубка |
Вогнутость корня шва | Дефект в виде углубления на обратной поверхности сварного одностороннего шва. | - большие зазоры; - малое притупление. | Возникают в стыковых и угловых швах. Ослабление сечения шва. Исправление – подварка. |
Занижение шва | Дефект в виде провисания сварного шва. | - большой зазор; - большой угол разделки кромок; - несоблюдение техники сварки. | Возникает при сварке алюминивых сплавов. Исправление – подварка с использованием присадочной проволоки. |
Смещение сваренных кромок. | Дефект в виде несовпадения сваренных кромок по высоте из-за некачественной сборки сварного соединения. | - нарушение технологии сборки. | Возникает , как правило, при сварке стыковых тонкостенных элементов. Концентратор напряжения. Исправление – подварка. |
Свищ сварного шва. | Дефект в виде несквозного углубления в сварном шве. | - некачественный основной металла; - нарушение защиты. | Сопровождает поры и трещины, выходящие на поверхность. Наиболее часто возникают при сварке в СО2. Исправление – подварка с разделкой. |
Поверхностное окисление сварного соединения. | Дефект в виде окисной пленки с различными цветами побежалости на поверхности сварного соединения. | - малый расход защитного газа; - наличие примесей в защитном газе; - загрязнение поверхности сопла; - неправильно подобранный диаметр сопла и расстояние его от поверхности металла; - отсутствие дополнительных защитных козырьков; - нарушение техники сварки. | Возникает при сварке активных металлов. Исправление – зачистка поверхности. |
Трещины: - поверхностные; - внутренние; - сквозные; - продольные; - поперечные; - разветвленные. | Дефект в виде разрыва в сварном шве по линии сплавления или в околошовной зоне | - жесткая конструкция изделия; - сварка в жестко закрепленных приспособлениях; - большой время между сваркой и термообработкой; - большая скорость охлаждения; - ошибка в проектировании сварного шва (близко расположенные концентраторы); - нарушение технологии (температура подогрева, порядок наложения швов); - нарушение защиты; - некачественный основной металл. | Наиболее опасный и недопустимый дефект, как правило , брак. Исправление – подварка с предварительной разделкой или засверловкой концов трещины. |
Поры сварного шва: -одиночные; -рассеянные; -скопления; -цепочка. | Дефект сварного шва в виде полости округлой или продолговатой формы заполненной газом. | - влажный флюс; - отсыревшие электроды; - некачественная подготовка свариваемых кромок и поверхности сварочной проволоки; - увеличенный диаметр электрода; - длинная дуга; - увеличенная скорость сварки; - некачественная защита; - некачественный основной металл. | Как правило, возникает при сварке алюминиевых и титановых сплавов, в глубоких стыковых швах, при затруднении дегазации. Ослабление сечения. Снижение герметичности. Исправление – единичные поры оставляют, во всех остальных случаях подварка. |
Включения: -шлаковые; -оксидные; -вольфрамовые; -нитридные. | Дефекты в виде неметаллических частиц или инородного металла в металле шва. | - некачественная подготовка поверхности; - некачественный основной металл; - нарушение технологии сварки; - нарушение защиты. | Имеют сферическую или продолговатую форму, а также в виде прослоек. Концентраторы напряжения. Исправление – подварка с разделкой. |
Основные методы дефектоскопии сварных соединений, приведены в таблице
Дефекты | Методы неразрушающего контроля |
Наружные | Визуальный и визуально-оптический. Капиллярный, магнитный, вихретоковый. |
Внутренние | Акустический (ультразвуковой), магнитный, радиационный (рентгенографический) |
Сквозные | Капиллярный. Течеискателем. |
Раздел III.
Охрана труда.
Основные требования безопасности труда при ручной дуговой сварке.
При выполнении сборочных и сварочных работ существуют следующие основные опасности для здоровья рабочих: поражение электрическим током, поражение лучами дуги глаз и открытых поверхностей кожи, ушибы и порезы во время подготовки изделий к сварке и во время сварки, отравление вредными газами и пылью, ожоги от разбрызгивания электродного расплавленного металла и шлака.
Поражение электрическим током.
Травма возникает при замыкании электрической цепи сварочного аппарата через тело человека (рис.). Причинами являются: недостаточная электрическая изоляция аппаратов и питающих проводов, плохое состояние спецодежды и обуви сварщика, сырость и теснота помещений и другие факторы.
В условиях сварочного производства электротравмы происходят при движении тока по одному из трех путей: рука — туловище — рука; рука — туловище — нога; обе руки — туловище — обе ноги.
При движении тока по третьему пути сопротивление цепи наибольшее, следовательно, степень травматизма наименьшая. Наиболее сильное действие тока будет при движении его по первому пути.
В зависимости от величины электрический ток, проходящий через тело человека (при частоте 50 Гц), вызывает следующие травмы: при 0,6 — 1,5 мА — легкое дрожание рук; 5 — 7 мА — судороги в руках; 8—10 мА — судороги и сильные боли в пальцах и кистях рук; 20 — 25 мА — паралич рук, затруднение дыхания; 50 — 80 мА — паралич дыхания; 90 — 100 мА — паралич дыхания, при длительности более 3 с — паралич сердца; 3000 мА и при длительности более 0,1с — паралич дыхания и сердца, разрушение тканей тела. Следовательно, смертельным следует считать величину тока 0,1 А. С повышением частоты электрического тока более 500 Гц действие его существенно ослабевает.
Сопротивление организма человека. Электрическое сопротивление разных частей тела человека различно: наибольшее сопротивление имеет сухая кожа, ее верхний роговой слой, в котором нет кровеносных сосудов, а также костная ткань; значительно меньшее сопротивление имеют кровь и спинно-мозговая жидкость. Сопротивление зависит от внешних условий: оно понижается при повышении температуры, влажности, загазованности помещения. Сопротивление зависит от состояния кожных покровов: при наличии повреждений кожи (ссадин, царапин) сопротивление тела уменьшается.
При напряжении выше 100 В происходит пробой верхнего рогового слоя кожи, что также ведет к уменьшению сопротивления тела. Сопротивление человека, находящегося под действием электрического го тока, зависит также от плотности контактов, площади соприкосновения с токоведущими частями поверхности и пути электрического тока (см. рис.). При определении условий электробезопасности считают величину сопротивления, равную 1000 —2000 Ом в зависимости от напряжения.
Безопасным считается напряжение 12 В, а при работе в сухих, отапливаемых и вентилируемых помещениях — 36 В.
Защита от поражения электрическим током. Для защиты сварщика от поражения электрическим током необходимо надежно заземлять корпус источника питания дуги и свариваемое изделие; не использовать контур заземления в качестве сварочного провода; хорошо изолировать рукоятку электрододержателя; работать в сухой и прочной спецодежде и рукавицах (ботинки не должны иметь в подошве металлических шпилек и гвоздей); прекращать работу при дожде и сильном снегопаде (если нет укрытий); не производить ремонта оборудования и аппаратуры (должен выполнять электрик); при работе внутри сосудов пользоваться резиновым ковриком и переносной лампой напряжением не более 12 В.
Заземление. 1 Защитное заземление представляет собой соединение металлическим проводом частей электрического устройства (например, корпуса сварочного трансформатора) с землей.
Заземление служит для защиты от поражения электрическим током при прикосновении к металлическим частям электрических устройств (корпуса источников питания, шкафы управления и др.), оказавшимися под напряжением в результате повреждения электрической изоляции.
Земля в аварийном режиме работы электрооборудования используется в качестве проводника в цепи замыкания. При правильном заземлении электрооборудования образуются параллельные электрические ветви: одна с малым сопротивлением (3 — 4 Ом), а другая, в которую входит человек или группа людей, с большим сопротивлением (2000 Ом). Поэтому практически ток не пройдет через тело человека в случае соприкосновения его с корпусом источника питания, случайно оказавшимся под напряжением.
Включение в работу незаземленных источников питания дуги запрещается (однако имеются некоторые исключения).
Заземление выполняется различно в зависимости от напряжения и системы электроснабжения (с глухозаземленной нейтралью или с изолированной нейтралью). На рис. 2 дана схема сварочного трансформатора при питании его от сети с глухозаземленной нейтралью.
Из схемы видно, что для питания однофазного сварочного трансформатора от пункта подключения до вводной коробки трансформатора приложен трехжильный гибкий шланговый кабель. Третья жила присоединена одним концом к заземляющему болту корпуса сварочного трансформатора и другим концом к корпусу пункта подключения. Зажим-вывод обмотки низкого напряжения сварочного трансформатора присоединен к свариваемой детали и одновременно заземляющим металлическим проводником к заземляющему болту на корпусе сварочного трансформатора. На передвижных установках применяют переносные заземляющие устройства.
Оказание помощи пострадавшему от электрического тока.
В первую очередь необходимо отсоединить токоведущий провод от пострадавшего; это делается перерубанием провода острым инструментом с изолирующей рукояткой или отбрасыванием провода от пострадавшего сухой доской. В лучшем случае (если есть возможность) надо сразу выключить рубильник или предохранители. Оказывающий помощь должен предохранить себя от попадания в электрическую цепь, пользуясь для этого изоляционными материалами (сухие доски, резиновый коврик, стекло, пластмасса). Если пострадавший находится на высоте, должны быть приняты меры, исключающие падение после его отключения от провода.
Пострадавшему должен быть обеспечен приток свежего воздуха, полный покой. При отсутствии дыхания и пульса необходимо немедленно начать искусственное дыхание. Во всех случаях при поражении электрическим током необходимо вызвать врача.
Поражение электрическим током (электрический удар) может вызвать клиническую (мнимую) смерть. Состояние клинической смерти продолжается от 4 до 12 мин. За это время человек может быть возвращен к жизни в результате оказания медицинской помощи (реанимация), непрямого массажа сердца или искусственного дыхания.
Следует иметь в виду, что констатировать смерть может только врач. Поэтому оказывать помощь пострадавшему надо непрерывно до прибытия врача.
Следует иметь в виду, что констатировать смерть может только врач. Поэтому оказывать помощь пострадавшему надо непрерывно до прибытия врача.
Искусственное дыхание.
Пострадавшего укладывают на живот. Надо обеспечить приток свежего воздуха, расстегнуть пояс, ворот и другие части одежды, затрудняющие дыхание и кровообращение, а также вытянуть язык, который при параличе западает в гортань и перекрывает дыхательные пути. Один человек, расположившись у головы, удерживает пальцами язык носовым платком, а два других делают искусственное дыхание — перемещением локтей пострадавшего от нижних ребер до уровня маковки головы. Локти должны перемещаться параллельно земле, необходимо производить легкое нажатие локтями на середину ребер. Число движений равно числу собственных глубоких дыханий.
В настоящее время широкое распространение получил способ искусственного дыхания «рот в рот». В этом случае оказывающий помощь вдувает воздух непосредственно в рот пострадавшего. Пострадавший лежит на спине, под лопатки его подложен мягкий валик (одежда), голова опрокинута назад. Оказывающий помощь делает глубокий вдох, плотно (через марлю, платок) прижимает свой рот ко рту пострадавшего и с силой вдувает воздух. При этом нос пострадавшего должен быть зажат. После вдувания рот и нос пострадавшего освобождают для свободного выхода воздуха. Вдувание производят каждые 5 —6 с.
Этот способ более эффективен, чем ручной, так как при каждом вдувании в легкие пострадавшего воздуха поступает в 3 — 4 раза больше.
Поражение зрения.
Спектр лучистой энергии, выделяемой сварочной дугой, состоит из инфракрасных, световых и ультрафиолетовых лучей. Интенсивность излучения возрастает с повышением тока дуги. При сварке на постоянном токе интенсивность выше по сравнению со сваркой на переменном токе. Различные способы сварки по степени убывания интенсивности излучения дуги можно расположить в такой последовательности: в углекислом газе, покрытыми электродами, вольфрамовым электродом в аргоне и плазменно-дуговая.
Яркость видимой части спектра достигает 16000 кд/см2, что в тысячи раз превышает переносимую человеком дозу.
Ультрафиолетовые лучи вызывают заболевание слизистой и иногда роговой оболочки глаз, называемое электроофтальмией, и ожог открытой кожи. сварщика. Электроофтальмия начинается спустя 5 — 8 ч после облучения глаз. Она сопровождается болью в глазах, ощущением засорения глаз мельчайшими частицами, веки глаз закрываются, их трудно поднять, появляется слезотечение, сопровождаемое головной болью.
Практика изготовления сварных изделий в цехах показывает, что электроофтальмия чаще наблюдается у подсобных рабочих и сборщиков, чем у сварщиков.
Максимальная допустимая продолжительность ультрафиолетового облучения глаз, без получения для глаз болей и вреда, при сварке покрытыми электродами, шланговой сварки в углекислом газе и сварке вольфрамовым электродом в аргоне при токе дуги 200 А (постоянный ток с обратной полярностью) составляет на расстоянии 1 м соответственно 6; 13 и 45 с; на расстоянии 10 м—10; 21 и 75 мин; на расстоянии 30 м—1,6; 3,3 и 11,1 ч.
Электроофтальмия излечивается в течение 2 — 3 дн цинковыми каплями или каплями «Альбуцид», промыванием слабым чаем, холодным компрессом.
Инфракрасные лучи могут вызвать повреждение глаз только при длительном действии. Это повреждение называется катарактой (помутнение) хрусталика и может привести к частичной или полной потере зрения. Однако это заболевание у сварщиков встречается редко.
Защита органов зрения. Электросварщики работают со светофильтрами, которые задерживают и поглощают излучение дуги.
В заводских условиях сварщики работают в изолированных кабинах. При работе на открытом воздухе сварщик должен огородить место сварки (щитами, ширмами и т. п.), учитывая, что вредные излучения дуги распространяются на 15 — 30 м и более.
Стены и потолки сварочных помещений должны окрашиваться матовой краской темных тонов, исключающей отражение лучей дуги.
Отравление вредной пылью и газами.
Отравление возможно при сильном загрязнении воздуха сварочной пылью из оксидов и соединений марганца, углерода, азота, хлора, фтора и др. По существующим нормам запыленность помещения не должна превышать 10 мг/м3 воздуха, содержание Мп2 не более 0,3 мг/м3, СО не более 30 мг/м3, N0 не более 5 мг/м3, паров свинца не более 0,1 мг/м3 и т. д. Количество оксидной и вредной пыли при дуговой сварке образуется от 10 до 150 г на 1 кг расплавленных электродов.
Признаками отравления обычно являются: головокружение, головные боли, тошнота, рвота, слабость, учащенное дыхание и др. Отравляющие вещества могут также откладываться в тканях организма человека и вызывать хронические заболевания.
Мероприятиями по борьбе с загрязнениями воздуха служат внедрение новых марок покрытий электродов и порошков с наименьшими токсичными свойствами; приточно-вытяжная вентиляция; устройство передвижных отсосов; приток свежего воздуха от воздухопроводов через электрододержатель или шлём; пользование респиратором с химическим фильтром, а иногда и противогазом.
Ожоги.
При сварке электродный металл и шлак разбрызгиваются; горячие брызги могут попасть на незащищенную кожу сварщика или вызвать тление и прогорание одежды, а тем самым ожоги. Для защиты от ожогов сварщиков обеспечивают специальной одеждой, обувью, рукавицами и головным убором. При работе рядом с легковоспламеняющимися материалами может возникнуть пожар. Опасность пожара особенно следует учитывать при работе на строительстве. Если сварочные работы проводятся наверху, то необходимо находящиеся внизу аппаратуру и любые легковоспламеняющиеся материалы защищать от падающих сверху искр. Требуется также особая осторожность при сварке в тех случаях, когда около места выполнения работ располагаются деревянные леса или имеются отходы в виде стружки, опилок и т. д. Иногда для выполнения сварочных работ требуется обязательное разрешение пожарной охраны. В местах сварочных работ должны находиться вода, ящик с песком, щит с инструментом и огнетушители.
Ушибы, порезы при сборке и сварке изделий.
Основным причинами механических травм на производстве при сборочно-сварочных работах могут быть: отсутствие приспособлений для транспортировки и сборки тяжелых деталей; неисправные транспортные средства (тележки, краны и т. д.); неисправный и непроверенный такелаж (канаты, цепи, тросы, захваты и др.); неисправный инструмент (кувалды, молотки, зубила, ключи и т. д.); незнание и несоблюдение персоналом основных правил по такелажным работам.
При сборочно-сварочных работах чаще всего наблюдаются травмы в виде ушибов и ранений рук (от неумелого обращения с инструментом и деталями) и ног (от падения собираемых деталей). Правильно оснащенное рабочее место сварщика должно полностью обеспечить работающих от всяких механических повреждений.
При составлении технологии сборки и сварки следует самым тщательным образом продумать все проектируемые операции с точки зрения безопасности работы.
Список использованной литературы.
1.Основы слесарного дела: учебник для студ. учреждений сред. проф. образования / Б.С. Покровский. – М.: Издательский центр «Академия», 2017. – 208с.
2.Подгтовительные и сборочные операции перед сваркой: учебник для студ. учреждений сред. проф. образования / В.В. Овчинников. – М.: Издательский центр «Академия», 2018. – 192с.
3.Технология производства сварных конструкций: учебник для студ. учреждений сред. проф. образования / В.Н. Галушкина. – 6-е изд. - М.: Издательский центр «Академия», 2017. – 192с.
4. Контроль качества сварных соединений : учеб. для студ. учреждений сред. проф. образования / В.В. Овчинников. – М.: Издательский центр «Академия», 2018. – 240с.
5 .Ручная дуговая сварка (наплавка, резка) плавящимся покрытым электродом: учебник для студ. Учреждений сред. Проф. Образования / В.В. Овчинников. – 2-е изд., стер. – М.: Издательский центр «Академия», 2018. – 208с.
6.Частично механизированная сварка (наплавка) плавлением: учебник для студ. Учреждений сред. Проф. Образования / В.П. лялякин, Д.Б. Слинко. – М.: Издательский центр «Академия», 2018. – 192с.
7. Основы материаловедения для сварщиков: учебник для студ. учреждений сред. проф. образования / В.В. Овчинников.–М.: Издательский центр «Академия», 2017. – 208с.
8.Технические измерения: учебник для студ. Учреждений сред. проф. образования / С.А. Зайцев, А.Н. Толстов, - М. : Издательский центр «Академия», 2018. – 368 с.
Интернет – ресурсы:
Образовательный портал: http\\www.edu.sety.ru
Учебная мастерская: http\\www.edu.BPwin -- Мастерская Dr_dimdim.ru
Образовательный портал: http\\www.edu.bd.ru
Электронно-библиотечная система IPRbooks
https://multiurok.ru/svarmet/files
Приложения.
Таблица 1
Марка стали | Массовая доля элементов, % |
углерода | марганца | кремния |
Ст 0 | Не более 0,23 | - | - |
Ст 1 кп | 0,06 – 0,12 | 0,25 – 0,50 | Не более 0,05 |
Ст 1 пс | 0,06 – 0,12 | 0,25 – 0,50 | 0,05 – 0,15 |
Ст 1 сп | 0,06 – 0,12 | 0,25 – 0,50 | 0,15 – 0,30 |
Ст 2 кп | 0,09 – 0,15 | 0,25 – 0,50 | Не более 0,05 |
Ст 2 пс | 0,09 – 0,15 | 0,25 – 0,50 | 0,05 – 0,15 |
Ст 2 сп | 0,09 – 0,15 | 0,25 – 0,50 | 0,15 – 0,30 |
Ст 3 кп | 0,14 – 0,22 | 0,30 – 0,60 | Не более 0,05 |
Ст 3 пс | 0,14 – 0,22 | 0,40 – 0,65 | 0,05 – 0,15 |
Примечание: Допускается в НТД на конкретные виды металлопродукции при обеспечении нормируемого комплекса свойств уточнение:
нижнего предела массовой доли углерода или марганца;
нижнего предела массовой доли кремния при раскислении полуспокойной стали алюминием, титаном или другим раскислителями, не содержащими кремния, а также несколькими раскислителями (ферросилицием и алюминием, ферросилицием и титаном и др.).
Таблица 2
элементы | Предельные отклонения в прокате из стали, % |
кипящей | полуспокойной и спокойной |
Углерод | + 0,03 | + 0,03 - 0,02 |
Марганец | + 0,05 - 0,04 | + 0,05 - 0,03 |
Кремний | ____ | + 0,03 - 0,02 |
Фосфор | + 0,006 | + 0,005 |
Сера | + 0,006 | + 0,005 |
Примечание: для проката из стали марок Ст 3 пс, Ст 3 сп, Ст 3 Гпс и Ст 3 Гсп, предназначенном для сварных конструкций, плюсовые отклонения по массовой доле углерода не допускаются.
Таблица 3
Марка стали | Цвет и маркировка |
Ст 0 | Красный и зеленый |
Ст 1 | Желтый и черный |
Ст 2 | Желтый |
Ст 3 | Красный |
Ст 3 Гпс | Красный и коричневый |
Ст 3 Гсп | Синий и коричневый |
Ст 4 | Черный |
Ст 5 | Зеленый |
Ст 5 Гпс | Зеленый и коричневый |
Ст 6 | синий |
ГОСТ на сварные соединения (в зависимости от вида сварки)
Тип соединения | Форма подготовленных | Характер сварного шва | Форма поперечного сечения | Толщина свариваемых | Условное обозначение |
| кромок | | подготовленных кромок | сварного шва | деталей, мм | соединения |
Стыковое | С отбортовкой кромок | Односторонний | 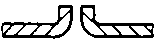 | 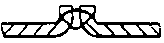 | 1-4 | С1 |
| |
| С отбортовкой одной кромки | | 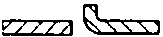 |  | 1-4 | С2 |
| | |  |  | | С3 |
| | Односторонний на съемной подкладке |  |  | 1-4 | С4 |
| Без скоса кромок | Односторонний на остающейся подкладке |  |  | | С5 |
| | Односторонний замковый |  |  | 1-4 | С6 |
| | Двухсторонний | |  | 2-5 | С7 |
| | Односторонний | | | | С8 |
| | Односторонний на съемной подкладке | | | | С9 |
| Со скосом одной кромки | Односторонний на остающейся подкладке | | | 3-60 | C10 |
| | Односторонний замковый | | | | C11 |
| | | | | | C12 |
И т.п.