Самостоятельная работа №2
Определение твердости металлов.
1.Как определяют твердость металла по методу Бринелля?
2.Как определяют твердость металла по методу Роквелла?
3.Как определяют твердость металла по методу Виккерса?
Для того чтобы детали и механизмы служили длительно и надежно, материалы, из которых они изготовлены, должны соответствовать необходимым условиям работы. Именно поэтому важно контролировать допустимые значения их основных механических показателей. К механическим свойствам относятся твердость, прочность, ударная вязкость, пластичность. Твердость металлов - первичная конструкционная характеристика. Понятие Твердость металлов и сплавов - это свойство материала создавать сопротивление при проникновении в его поверхностные слои иного тела, которое не деформируется и не разрушается при сопутствующих нагрузках (индентора). Определяют с целью: - Читайте подробнее на получения информации о допустимых конструкционных особенностях и о возможностях эксплуатации; анализа состояния под действием времени; контроля результатов температурной обработки. От этого показателя частично зависят прочность и устойчивость поверхности к старению. Исследуют как исходный материал, так и уже готовые детали. Варианты исследования Показателем является величина, которая называется числом твердости. Существуют различные методы измерения твердости металлов. Наиболее точные исследования заключаются в использовании различных видов вычисления, инденторов и соответствующих твердомеров: Бринелля: суть работы аппарата – вдавливание шарика в исследуемый металл или сплав, вычисление диаметра отпечатка и последующее математическое вычисление механического параметра. Роквелла: используются шарик или алмазный конусный наконечник. Значение отображается на шкале или определяется расчётно. Виккерса: наиболее точное измерение твердости металла с применением алмазного пирамидального наконечника. Для определения параметрических соответствий между показателями разных способов измерения для одного и того же материала существуют специальные формулы и таблицы. Факторы, определяющие вариант измерения В лабораторных условиях, при наличии необходимого ассортимента оборудования, выбор способа исследования осуществляется в зависимости от определенных характеристик заготовки. Ориентировочное значение механического параметра. Для конструкционных сталей и материалов с небольшой твердостью до 450-650 НВ применяют метод Бринелля; для инструментальных, легированных сталей и других сплавов – Роквелла; для твердосплавов – Виккерса. Размеры испытуемого образца. Особо маленькие и тонкие детали обследуются с помощью твердомера Виккерса. Толщина металла в месте замера, в частности, цементированного или азотированного слоя. Все требования и соответствия задокументированы ГОСТом
Особенности методики Бринелля
Испытания на твердость металлов и сплавов с помощью твердомера Бринелля проводятся со следующими особенностями:
Индентор – шарик из легированной стали или из карбидо-вольфрамового сплава диаметром 1, 2, 2,5, 5 или 10 мм (гост 3722-81).
Продолжительность статического вдавливания: для чугуна и стали – 10-15 с., для цветных сплавов – 30, также возможна длительность в 60 с., а в некоторых случаях – 120 и 180 с.
Граничное значение механического параметра: 450 НВ при измерении стальным шариком; 650 НВ при использовании твердосплава.
Возможные нагрузки. С помощью входящих в комплект грузов корректируется фактическая сила деформации на испытуемый образец. Их минимальные допустимые значения: 153,2, 187,5, 250 Н; максимальные – 9807, 14710, 29420 Н (гост 23677-79).
С помощью формул, в зависимости от диаметра выбранного шарика и от испытуемого материала, можно вычислить соответствующее допустимое усилие вдавливания.
Тип сплава | Математическое вычисленные нагрузки |
Сталь, сплавы никеля и титана | 30D2 |
Чугун | 10D2, 30D2 |
Медь и медные сплавы | 5D2, 10D2, 30D2 |
Легкие металлы и сплавы | 2,5D2, 5D2, 10D2, 15D2 |
Свинец, олово | 1D2 |
Пример обозначения:
400HB10/1500/20, где 400HB – твердость металла по Бринеллю; 10 – диаметр шарика, 10 мм; 1500 – статическая нагрузка, 1500 кгс; 20 – период осуществления вдавливания, 20 с. Для установления точных цифр рационально исследовать один и тот же образец в нескольких местах, а общий результат определять путем нахождения среднего значения из полученных.
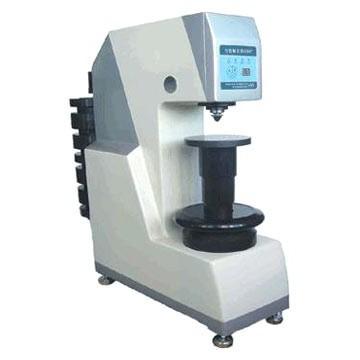
Определение твердости по методу Бринелля
Процесс исследования протекает в следующей последовательности:
Проверка детали на соответствие требованиям (ГОСТ 9012-59, гост 2789).
Проверка исправности аппарата.
Выбор необходимого шарика, определение возможного усилия, установка грузов для его формирования, периода вдавливания.
Запуск твердомера и деформация образца.
Измерение диаметра углубления.
Эмпирическое вычисление. НВ=F/A,
где F – нагрузка, кгс или Н; A – площадь отпечатка, мм2. НВ=(0,102*F)/(π*D*h), где D – диаметр шарика, мм; h – глубина отпечатка, мм.
Твердость металлов, измеренная этим способом, имеет эмпирическую связь с вычислением параметров прочности.
Метод точен, особенно для мягких сплавов. Является основополагающим в системах определения значений этого механического свойства.
Особенности методики Роквелла
Этот способ измерения был изобретен в 20-х годах XX века, более автоматизирован, чем предыдущий. Применяется для более твердых материалов. Основные его характеристики (ГОСТ 9013-59; гост 23677-79):
Наличие первичной нагрузки в 10 кгс.
Период выдержки: 10-60 с.
Граничные значения возможных показателей: HRA: 20-88; HRB: 20-100; HRC: 20-70.
Число визуализируется на циферблате твердомера, также может рассчитываться арифметически.
Шкалы и инденторы. Известно 11 различных шкал в зависимости от типа индентора и предельно-допустимой статической нагрузки. Наиболее распространённые в использовании: А, В и С.
А: алмазный конусный наконечник, угол при вершине 120˚, общая допустимая сила статического влияния – 60 кгс, HRA; исследуются тонкие изделия, в основном прокат.
С: также алмазный конус, рассчитанный на максимальное усилие 150 кгс, HRC, применим для твердых и закаленных материалов.
В: шарик размером 1,588 мм, изготовленный из закаленной стали или из твердого карбидо-вольфрамового сплава, нагрузка – 100 кгс, HRB, используется для оценки твердости отожжённых изделий.
Шарикообразный наконечник (1,588 мм) применим для шкал Роквелла B, F, G. Также существуют шкалы E, H, K, для которых используется шарик диаметром 3,175 мм (ГОСТ 9013-59).
Количество проб, проделанных с помощью твердомера Роквелла на одной площади, ограничивается размером детали. Допускается повторная проба на расстоянии 3-4 диаметра от предыдущего места деформации. Толщина испытуемого изделия также регламентируется. Она должна быть не меньше увеличенной в 10 раз глубины внедрения наконечника.
Пример обозначения: 50HRC – твердость металла по Роквеллу, измерена с помощью алмазного наконечника, ее число равно 50.
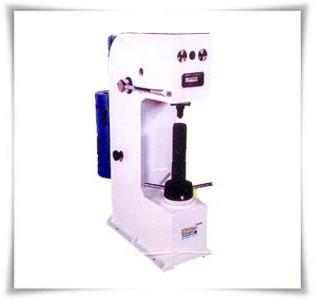
План исследования по методу Роквелла
Измерение твердости металла более упрощено, нежели для способа Бринелля.
Оценка размеров и характеристик поверхности детали.
Проверка исправности аппарата.
Определение типа наконечника и допустимой нагрузки.
Установка образца.
Осуществление первичного усилия на материал, величиной в 10 кгс.
Осуществление полного соответствующего усилия.
Чтение полученного числа на шкале циферблата.
Также возможен математический расчет с целью точного определения механического параметра. При условии использования алмазного конуса с нагрузкой 60 или 150 кгс:
HR=100-((H-h)/0,002;
при совершении испытания с помощью шарика под усилием 100 кгс: HR=130-((H-h)/0,002,
где h – глубина внедрения индентора при первичном усилии 10 кгс;
H – глубина внедрения индентора при полной нагрузке;
0,002 – коэффициент, регламентирующий величину перемещения наконечника при изменении числа твердости на 1 единицу.
Метод Роквелла является простым, но недостаточно точным. В то же время он позволяет измерять показатели механического свойства для твердых металлов и сплавов.
Характеристики методики Виккерса
Определение твердости металлов по данному способу наиболее просто и точно. Работа твердомера основана на вдавливании в образец алмазного пирамидального наконечника.
Основные особенности:
Индентор: алмазная пирамида с углом при вершине 136°.
Предельно допустимая нагрузка: для легированного чугуна и стали - 5-100 кгс; для медных сплавов - 2,5-50 кгс; для алюминия и сплавов на его основе - 1-100 кгс.
Период выдержки статической нагрузки: от 10 до 15 с.
Испытуемые материалы: сталь и цветные металлы с твердостью более 450-500 НВ, в том числе изделия после химико-термической обработки. Пример обозначения:
700HV20/15,
где 700HV – число твердости по Виккерсу;
20 – нагрузка, 20 кгс;
15 – период статического усилия, 15 с
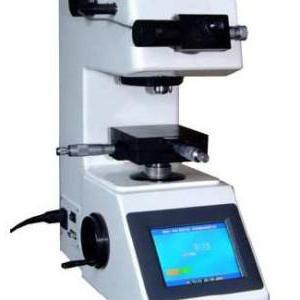
Последовательность исследования Виккерса
Порядок действий предельно упрощен.
Проверка образца и аппаратуры.
Особое внимание уделяется поверхности детали.
Выбор допустимого усилия.
Установка испытуемого материала.
Запуск твердомера в работу.
Чтение результата на циферблате.
Математический расчет по этому способу выглядит следующим образом: HV=1,8544*(F/d2),
где F – нагрузка, кгс;
d – среднее значение длин диагоналей отпечатка, мм.
Он позволяет измерять высокую твердость металлов, тонких и небольших деталей, при этом предоставляя высокую точность результата.
Способы перехода между шкалами
Определив диаметр отпечатка с помощью специального оборудования, можно с помощью таблиц определить твердость. Таблица твердости металлов – проверенный помощник в вычислении данного механического параметра. Так, если известно значение по Бринеллю, можно легко определить соответствующее число Виккерса или Роквелла.
Пример некоторых значений соответствия:
Диаметр отпечатка, мм | Метод исследования |
Бринелля | Роквелла | Виккерса |
А | В | С | |
3,90 | 241 | 62,8 | 24,0 | 99,8 | 242 |
4,09 | 218 | 60,8 | 20,3 | 96,7 | 218 |
4,20 | 206 | 59,6 | 17,9 | 94,6 | 206 |
4,99 | 143 | 49,8 | | 77,6 | 143 |
Таблица твердости металлов составлена на основе экспериментальных данных и имеет высокую точность. Также существуют графические зависимости твердости по Бринеллю от содержания углерода в железоуглеродистом сплаве. Так, в соответствии с такими зависимостями, для стали с количеством карбона в составе равному 0,2% она составляет 130 НВ.
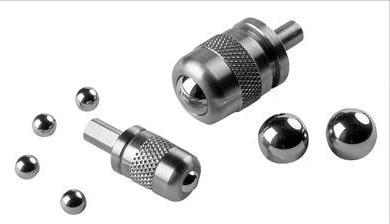
Требования к образцу
В соответствии с требованиями ГОСТов, испытуемые детали должны соответствовать следующим характеристикам:
Заготовка должна быть ровная, твердо лежать на столе твердомера, ее края должны быть гладкими или тщательно обработаны.
Поверхность должна иметь минимальную шероховатость.
Должна быть отшлифована и очищена, в том числе с помощью химических составов. Одновременно, во время процессов механической обработки, важно предупредить образование наклепа и повышения температуры обрабатываемого слоя.
Деталь должна соответствовать выбранному методу определения твердости по параметрическим свойствам.
Выполнение первичных требований – обязательное условие точности измерений.
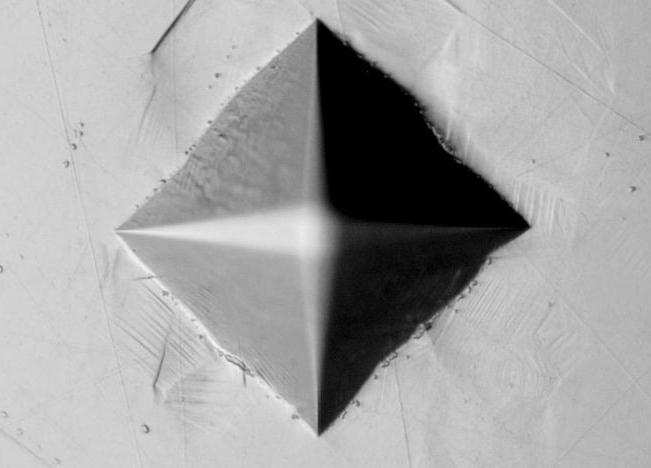
Твердость металлов - важное основополагающее механическое свойство, определяющее их некоторые остальные механические и технологические особенности, результаты предыдущих процессов обработки, влияние временных факторов, возможные условия эксплуатации. Выбор методики исследования зависит от ориентировочных характеристик образца, его параметров и химического состава.
4.Устройство разрывной машины?
Разрывная машина Р-100
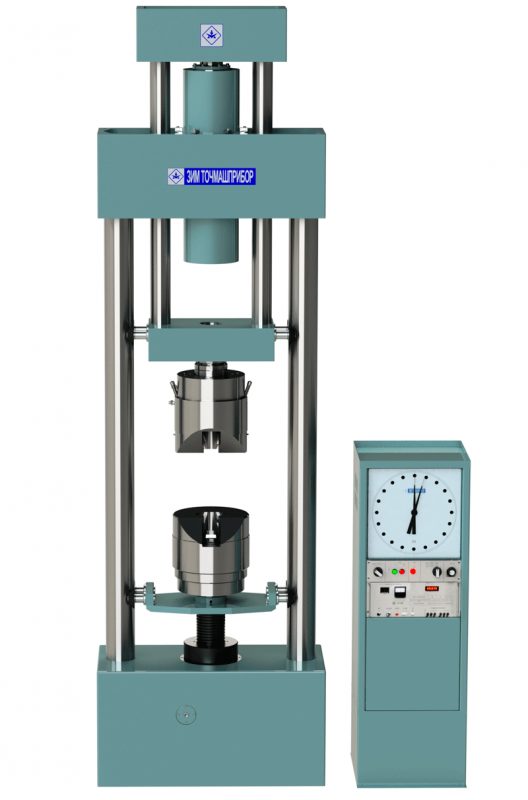
Разрывная машина Р-100 является одной из самых надежных испытательных машин на растяжение, изготавливаемых ООО «ЗИМ Точмашприбор».
Соответствие ГОСТ 28840, двухколонная вертикальная конструкция и возможность одновременной с проведением испытаний записи диаграмм делают её не только удобной в эксплуатации, но и выгодной в плане проведения непосредственно испытаний.
Разрывная машина Р-100 дает возможность тестирования образцов металлов и сплавов на растяжение с наибольшей предельной нагрузкой 1000 кН при нормальной температуре по ГОСТ 1497, ГОСТ 12004, а также изделий из них.
Одним из плюсов конструкции машины является то, что она выполнена с верхним расположением силового гидроцилиндра. Это позволяет проводить испытания образцов как на растяжение, так и на сжатие и изгиб.
Нагружающее же устройство состоит из основания, неподвижной траверсы, рабочего гидроцилиндра, подвижной траверсы и двух захватов. Основание и подвижная траверса соединены между собой колоннами.
Группой разработчиков ООО «ЗИМ Точмашприбор» в машине была предусмотрена одновременно с испытанием запись диаграмм. Данный принцип весьма полезен, ведь координаты для быстрой фиксации располагаются так: «нагрузка-перемещение», «нагрузка-деформация», «нагрузка-время», «перемещение-время» и «деформация-время».
Испытания образцов на испытательной машине серии Р-100 происходит путем деформирования образца вплоть до разрушения при контроле нагрузки, перемещения активного захвата, деформации образца, скорости нагружения.
В нижней части пульта расположена насосная установка, от которой осуществляется питание рабочего цилиндра машины.
Р-100 - это простая в обращении, высококачественная испытательная машина, на которой при применении дополнительных приспособлений могут проводиться испытания на сжатие, а также на изгиб по ГОСТ 14019-80.
В комплект базовой поставки входят:
Устройство нагружающее с гидравлическими клиновыми захватами.
Пульт, включающий установку насосную, электрооборудование, торсионный силоизмеритель, блок измерения, прибор самопишущий двухкоординатный Н307/1 ТУ25-0045.048-25.
Приспособление Хб 6.894.020 для механических испытаний образцов на сжатие по ГОСТ 27208.
Комплект сменных частей, комплект инструмента и принадлежностей, комплект запасных частей.
В базовой комплектации машина обеспечивает испытание на растяжение:
цилиндрических образцов типов VI, VII ГОСТ 1497;
цилиндрических образцов с головками тип. III №1…5 ГОСТ 1497;
плоских образцов типов I, II ГОСТ 1497;
Машина обеспечивает:
деформирование образцов до разрушения;
измерение нагрузки, перемещения активного захвата и деформации (при укомплектовании машин тензометрами);
поддержание скорости нагружения;
запись нагрузки, перемещения активного захвата и деформации;
электрический выход на ЭВМ или цифропечать величины нагрузки и перемещения активного захвата.
Рабочее пространство машины позволяет устанавливать термо- и криокамеры, а также производить механические испытания различных узлов и деталей.
5.Что называют законом пропорциональности?
Закон пропорциональности означает существование определенных количественных соотношений (соразмерностей, соответствий или зависимостей) между различными частями целого. Такие соотношения называются пропорциями. Они могут быть объективными и субъективными, статичными и динамичными.
Реализация данного закона ведет к повышению жизнеспособности системы и эффективности ее функционирования. Несоответствия между частями целого называются диспропорциями, которые снижают эффективность организации и способствуют ее разрушению.
При использовании слова «пропорциональность» в значении «соотношение» имеются ввиду определенные количественные соотношения между частями целого. Соблюдение определенных соотношений позволяет говорить о соразмерности, правильных пропорциях и соответствии между ними.
Сознательно или неосознанно, человек всегда стремился к гармонии, к определенным пропорциям в окружающих его вещах, процессах и явлениях. Пропорции отражают объективно существующие связи и зависимости между частями целого. Данный закон, в связи с этим, называют еще «законом гармонии» или «законом красоты».
Закон пропорциональности начал проявлять себя задолго до его осознания и теоретического обоснования. В наиболее яркой форме закон проявился в архитектуре и живописи. Существование там правильных пропорций подтверждает египетский треугольник (треугольник с соотношением сторон 3:4:5) и «золотое сечение» (деление отрезка АС на две части таким образом, что большая его часть АВ относится к меньшей ВС так, как весь отрезокАС относится к АВ, т.е. АВ:ВС=АС:АВ. Этот термин ввел Леонардо да Винчи).
Аналогичные пропорции существуют и в живой природе: строение молекул органических веществ, развитие и строение организма, численность каких-либо особей в природе и др.
Предел пропорциональности — механический параметр в сопротивлении материалов:
Максимальная величина напряжения, при котором ещё выполняется закон Гука, то есть деформация тела прямо пропорциональна приложенной нагрузке (силе). Следует заметить, что во многих материалах нагружение до предела упругости вызывает обратимые (то есть, упругие в общем-то) деформации, но уже не прямо пропорциональные напряжениям. Кроме того, эти деформации могут «запаздывать» относительно роста нагрузки как при нагружении, так и при снятии нагрузки.
Напряжение, при котором отступление от линейной зависимости между нагрузкой и удлинением достигает такой величины, что тангенс угла наклона, образованный касательной к кривой нагружения в координатах «нагрузка-удлинение» в точке предела пропорциональности и осью напряжения, увеличивается на 50 % от своего первоначального значения на упругом участке.
6.Что называют физическим пределом текучести?
Предел текучести — механическое напряжение σ0, дальше которого упругая деформация тела (исчезающая после снятия напряжения) переходит в пластическую (необратимую, когда геометрия тела не восстанавливается после снятия деформирующего напряжения). Предел текучести соответствует площадке текучести материала. В случае, если такая площадка отсутствует, вместо σт используется напряжение σ0,2 (читается: сигма ноль-два), которое соответствует напряжению, при котором остаточные деформации конструкции (пластические деформации) составляют 0,2% от длины испытываемого образца.
7.Как определяют модуль упругости?
Модуль упругости — общее название нескольких физических величин, характеризующих способность твёрдого тела (материала, вещества) упруго деформироваться (то есть не постоянно) при приложении к нему силы. В области упругой деформации модуль упругости тела в общем случае зависит от напряжения и определяетсяпроизводной (градиентом) зависимости напряжения от деформации, то есть тангенсом угла наклона начального линейного участка диаграммы напряжений-деформаций.
В наиболее распространенном случае зависимость напряжени деформации линейная (закон Гука):{\displaystyle E={\frac {\sigma }{\varepsilon }}}
Если напряжение измеряется в паскалях, то, поскольку деформация является безразмерной величиной, единицей измерения λ также будет паскаль. Альтернативным определением является определение, что модуль упругости — это напряжение, достаточное для того, чтобы вызвать увеличение длины образца в два раза. Такое определение не является точным для большинства материалов, потому что это значение намного больше чем предел текучести материала или значения, при котором удлинение становится нелинейным, однако оно может оказаться более интуитивным.
Разнообразие способов, которыми могут быть изменены напряжения и деформации, включая различные направления действия силы, позволяют определить множество типов модулей упругости. Здесь даны три основных модуля:
Модуль Юнга (E) характеризует сопротивление материала растяжению/сжатию при упругой деформации, или свойство объекта деформироваться вдоль оси при воздействии силы вдоль этой оси; определяется как отношение напряжения к деформации сжатия (удлинения). Часто модуль Юнга называют просто модулем упругости.
Модуль сдвига или модуль жесткости (G или {\displaystyle \mu }) характеризует способность материала сопротивляться изменению формы при сохранении его объёма; он определяется как отношение напряжения сдвига к деформации сдвига, определяемой как изменение прямого угла между плоскостями, по которым действуют касательные напряжения. Модуль сдвига является одной из составляющих явления вязкости.
Модуль объёмной упругости или Модуль объёмного сжатия (K) характеризует способность объекта изменять свой объём под воздействием всестороннего нормального напряжения (объёмного напряжения), одинакового по всем направлениям (возникающего, например, при гидростатическом давлении). Он равен отношению величины объёмного напряжения к величине относительного объёмного сжатия. В отличие от двух предыдущих величин, модуль объёмной упругости невязкой жидкости отличен от нуля (для несжимаемой жидкости — бесконечен).
Существуют и другие модули упругости: коэффициент Пуассона, параметры Ламе.
Гомогенные и изотропные материалы (твердые), обладающие линейными упругими свойствами, полностью описываются двумя модулями упругости, представляющими собой пару любых модулей. Если дана пара модулей упругости, все другие модули могут быть получены по формулам, представленным в таблице ниже.
В невязких течениях не существует сдвигового напряжения, поэтому сдвиговый модуль всегда равен нулю. Это влечёт также и равенство нулю модуля Юнга.