§ 2. Свойства электрической сварочной дуги
Дуга — это устойчивый вид разряда, существующий при токе от десятых долей ампера до тысяч ампер. Известно несколько способов возбуждения дугового разряда. По способу В. В. Петрова два электрода сводят до соприкосновения и сразу же разводят на небольшое расстояние. В этот момент между ними возникает дуга. Упрощенное объяснение этого явления следующее. При соприкосновении электродов электрическая цепь замыкается и по ней идет ток. В соответствии с законом джоуля-Ленца в проводниках выделяется теплота. Место контакта двух электродов, которое обладает самым большим сопротивлением, нагревается сильнее и быстрее остальных участков цепи. При высокой температуре начинается испарение материала электрода и возникает явление термоэлектронной эмиссии (термоэмиссия) — испускание электродов под действием теплового возбуждения. Если в этот момент разорвать контакт между электродами, возникает электрическое поле, подобное полю, возникающему между обкладками кондёнсатора. На катоде, подключенном к отрицательному полюсу источника тока, собираются те электроны, которые вылетают благодаря термоэмиссии. При достаточной напряженности электрического поля возникает явление автоэлектронной эмиссии — испускание электронов с поверхности катода под действием электростатических сил. В результате этих процессов в пространстве между электродами появляются свободные электроны, которые, сталкиваясь с молекулами и атомами газа и испарившегося электродного металла, «раскалывают» их на ионы и новые электроны (вторичная
эмиссия).В ионизированном таким образом пространстве развивается дуговой разряд.
В установившейся сварочной дуге конец электродного стержня и поверхность изделия расплавлены, так что дуга горит между жидкими электродами (рис. 4.6). Столб дуги имеет обычно коническую или сферическую форму, расширенную от электродного стержня к изделию. Пламя имеет значительные размеры и содержит главным образом пары материалов электродов, реагирующие с окружающим воздухом. Поверхность жидкой ванны на изделии не плоскогоризонтальна.
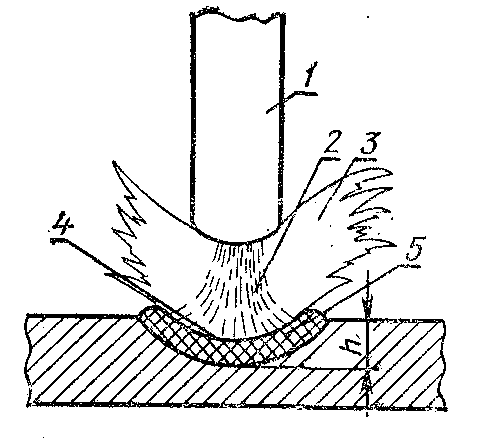
Рис. 4.6. Схема установившейся сварочной дуги
1 — электрод; 2 — столб дуги; З — пламя дуги; 4— кратер; 5—сварочная ванна; h — глубина расплавления.
Она вдавливается под действием механических сил, Образующееся углубление (ямка) называют кратером. дуга расплавляет металл на определенную глубину h (глубина расплавления, глубина провара, или просто провар).
Столб дуги заполнен заряженными частицами. Почти всегда в нем присутствуют нейтральные атомы и даже молекулы паров веществ, из которых сделаны электроды, и газов, окружающих дугу.
На движение частиц оказывают действие силы, вызванные разностью давлений из-за неодинаковой концентрации частиц, кулоновским взаимодействием между электронами и ионами и другими причинами.
Маленькие подвижные электроны быстро перемещаются, легко разгоняются и, сталкиваясь с атомами и ионами, передают им свою энергию. Столкновения электронов с атомами бывают упругими и неупругими.
При упругих столкновениях ничего заметного не происходит. Эти столкновения похожи на удары теннисных мячей. Атом, в который попал электрон, начинает двигаться быстрее (увеличивается его кинетическая энергия). В результате повышается температура плазмы.
Тот электрон, который в электрическом поле приобрел достаточную энергию, участвует в неупругих столкновениях (рис. 4.7), Попав в атом (молекулу), он возбуждает его, а когда удар достаточно силен, то и выбивает из атома его собственные электроны. Атом становится однозарядным положительным ионом, если выбит один электрон, двухзарядным — если два и т. д.
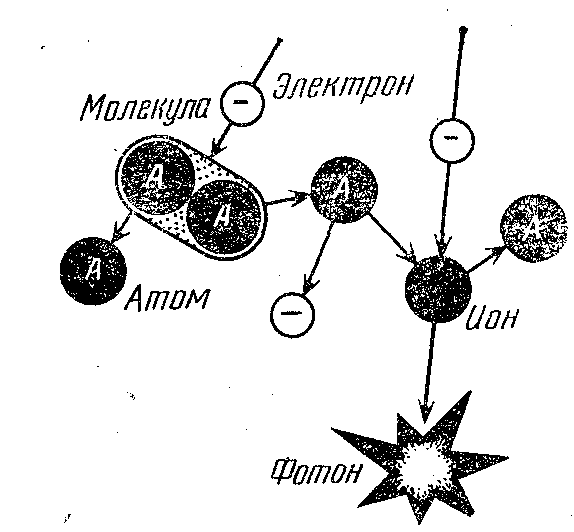
Рис. 4.7. Схема неупругих столкновений.
Сложные процессы идут у поверхности электродов. Именно здесь прерывается течение электронов по металлическому проводнику (электроду) и начинается другой вид тока (ток дуги), который создается как электродами, так и ионами. Изменяется характер явлений не только электрических, но и термических. Здесь горячая плазма граничит со сравнительно холодной (2...З тыс. °С) поверхностью электродов.
Кроме электрического поля, на поведение частиц в столбе дуги влияет еще много факторов: термическая диффузия — стремление разогретых частиц «разбежаться» в разные стороны; пинч-эффект—воздействие магнитного поля, возникающего вокруг столба и стремящегося его сжать и др. В зависимости от условий, в которых существует дуга, влияние этих факторов может ослабевать или усиливаться.
При сварке применяют прямую и обратную полярность. При прямой полярности источника тока подключают к электроду, плюс — к свариваемой детали, а при обратной полярности наоборот.
При сварке угольным электродом на постоянном токе и прямой полярности дуга легче возбуждается и устойчивее, чем при сварке на обратной полярности. При использовании металлических плавящихся электродов полярность дуги меньше влияет на ее устойчивость, поэтому сварку осуществляют как на переменном, так и на постоянном токе с прямой и обратной полярностью в зависимости от состава покрытия электродов и флюсов.
При сварке металлическим электродом длина дуги до 4 мм и не более О,6...О,8 диаметра электрода (короткая дуга). При сварке длинной дугой (больше 4 мм) увеличивается разбрызгивание, окисление металла, снижается качество шва.
§ 5. Электроды для дуговой сварки и наплавки
Электродами называют металлические и угольные стержни, предназначенные для электродуговой сварки и резки металлов.
Электроды для ручной дуговой сварки делят на неплавящиеся и плавящиеся. К первым относятся угольные, графитовые и вольфрамовые, ко вторым — электроды, имеющие стержень из стали, меди, чугуна, алюминия и различных сплавов. Как правило, они имеют специальные покрытия, которые служат для повышения устойчивости горения дуги и улучшения качества наплавляемого металла.
Покрытия электродов бывают тонкие (стабилизирующие) и качественные (толстые). Тонкие наносят слоем 0,1...О,3 мм, толстые—слоем О,5...2,5 мм. В состав качественных покрытий электродов входят стабилизирующие, шлакообразующие, газообразующие, раскисляющие, легирующие и связывающие компоненты.
Стабилизирующие вещества вводят в покрытие для снижения потенциала ионизации паров металла и повышения устойчивости горения сварочной дуги.
Шлакообразующие компоненты служат для защиты расплавленного металла от воздействия кислорода и азота воздуха. Они представляют собой окислы металлов и металлоидов, которые вводят в покрытие в виде титанового концентрата (ильменит), марганцевой руды (пиромозит), полевого шпата, мрамора, мела, каолина, кварцевого песка, доломита.
Газообразующие вещества при сгорании создают газовую защитную атмосферу, которая предохраняет расплавленный металл от воздействия кислорода и азота воздуха. Их вводят в покрытие электрода в виде органических соединений (древесная мука, хлопчатобумажная пряжа, крахмал, пищевая мука, декстрин, оксицелюлоза и др.).
Раскисляющие элементы (марганец, кремний, титан, алюминиевый, графит и др.), находясь в расплавленном металле сварного шва, легче вступают в химические соединения с кислородом, чем железо. Они нерастворимы в стали или обладают ограниченной растворимостью и в виде окислов всплывают на поверхность сварочной ванны. Большинство раскислителей вводят в покрытие не в чистом виде, а в виде ферросплавов.
Легирующие вещества вводят в покрытие для придания наплавленному металлу специальных свойств (повышение механических свойств, износостойкости, жаростойкости, сопротивления коррозии). Наиболее часто применяемые легирующие элементы — хром, никель, молибден, вольфрам, марганец, титан.
Связующие вещества (клеящие) служат для скрепления компонентов покрытия между собой и со стержнем электрода. Обычно применяют жидкое стекло (содовое или калиевое), декстрин, желатин, пластмасс.
Для стальных электродов используют специальную сварочную проволоку, которую выпускают диаметрами
0,3; 0,5; 0,8; 1; 1,2; 1,6; 2; 2,5; 3; 3,5; 4; 5; 6; 8; 10 и 12 мм.
Электроды в зависимости от назначения делят на ряд групп:
У — для сварки углеродистых и низколегированных конструкционных сталей с временным сопротивлением разрыву до 600 Н/мм2
Л — для сварки легированных конструкционных сталей с временным сопротивлением разрыву свыше 600 Н/мм2
Т — для сварки легированных теплоустойчивых сталей
В — для сварки высоколегированных сталей с особыми свойствами;
Н — для наплавки поверхностных слоев с особыми свойствами.
Электроды разделяют на марки по техническим условиям и паспортам. Каждому типу электродов могут соответствовать одна или несколько марок (табл. 1).
1. Наиболее распространенные покрытые Электроды и их назначение
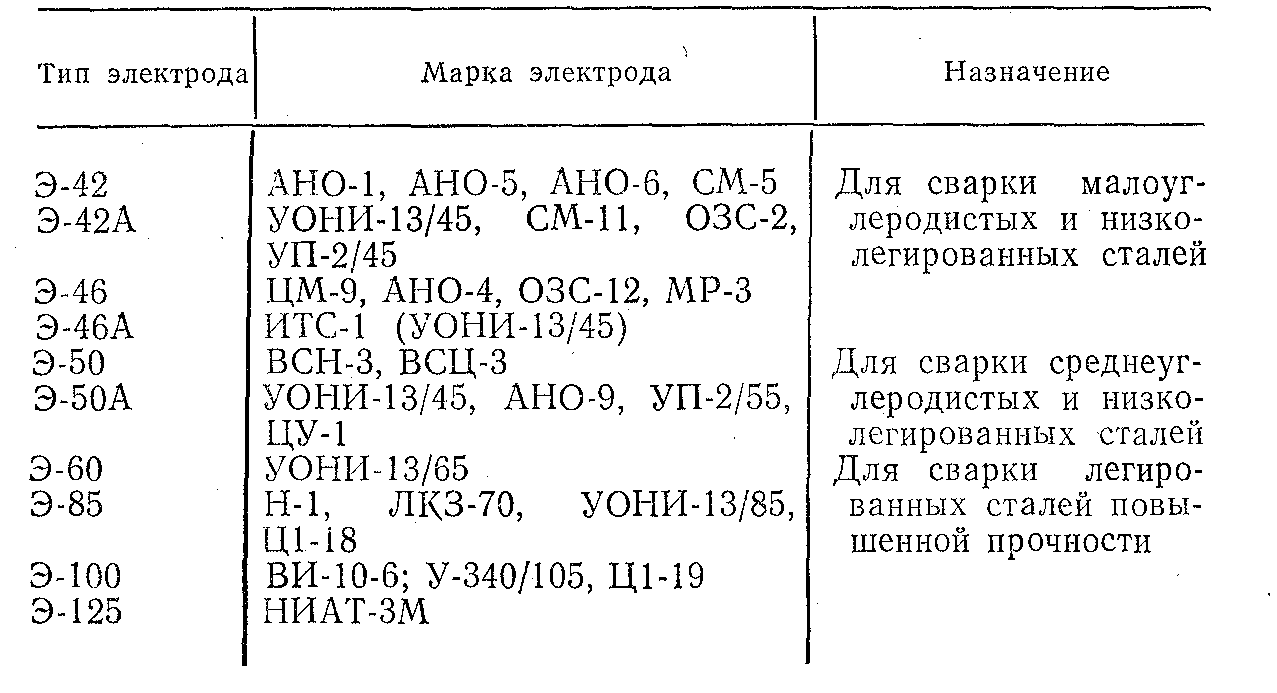
Электроды делят по толщине покрытия в зависимости от отношения D/d (D — диаметр покрытия, d — диаметр стержня):
М — с тонким покрытием (D/d ≤1,2);
С—со средним покрытием (1,2 D/d
Д — с толстым покрытием (1,45D/d
Г — с особо толстым покрытием (D/d 1,8).
Тип покрытия обозначают следующими буквами:
Р — руднокислое покрытие. Электродами с руднокислым покрытием (ОММ-5, ЦМ-7 и др.) производят сварку в любом пространственном положении шва, с ржавыми кромками и окалиной, переменным и постоянным током. Недостаток их в том, что наблюдается повышенное разбрызгивание металла и выделение соединений, вредно влияющих на организм человека.
Ф — фтористокальциевое покрытие. Электроды с фтористокальциевым покрытием (УОНИ-13/45, ЦЛ-18 и др.) применяют преимущественно при сварке постоянным током обратной полярности, во всех пространственных положениях шва. Они чувствительны к ржавчине, маслу, влаге и удлинению дуги.
Т — рутиловое покрытие. Электроды с таким покрыием (ЦМ-9, ОЗС-З, ОЗС-4 и др.) дают устойчивое горение дуги, хорошее формирование шва, небольшое разбрызгивание, нечувствительны к ржавчине. Их используют при сварке постоянным и переменным током в любом пространственном положении шва.
О – органическое покрытие. Электроды с органическим покрытием (ОМА-2 и др.) имеют умеренное разбрызгивание металла, дают малое количество шлака и пригодны для сварки во всех пространственных положениях шва как переменным, так и постоянным током.
По международной классификации тип покрытия условно обозначают следующими буквами: А — кислое (руднокислое); В — основное (фтористокальциевое); С — органическое (Целлюлозное); О — окислительное; R – рутиловое; У – специальное.
Условное обозначение электродов для сварки конструкционных сталей состоит из обозначения марки электрода, типа электрода, диаметра стержня, типа покрытия и номера ГОСТа. Например, условное обозначение электрода УОНИ-13/45-Э-42А-4,0ф ГОСТ 9467—75 расшифровывают следующим образом: УОНИ-13/45 — марка электрода; Э-42А—тип электрода (Э—электрод для дуговой сварки; 42 — минимальный гарантируемый предел прочности металла, Н/мм2; А — гарантируется получение повышенных пластических свойств металла шва); 4,0 — диаметр электродного. стержня, мм; Ф — фтористокальциевый тип покрытия; номер ГОСТа, по которому стандартизирован электрод.
Электроды применяют не только для сварки, но и для наплавки металла на различные детали при их ремонте и восстановлении (табл. 2).
для сварки чугуна при ремонте тракторов применяют стальную проволоку Св.08, Св.13Х25Н18, Св.О6ХI9Н9Т, чугунные Прутки и стержни марок А, Б,
2. Электроды для наплавки быстроизнашивающихся деталей сельскохозяйственных машин
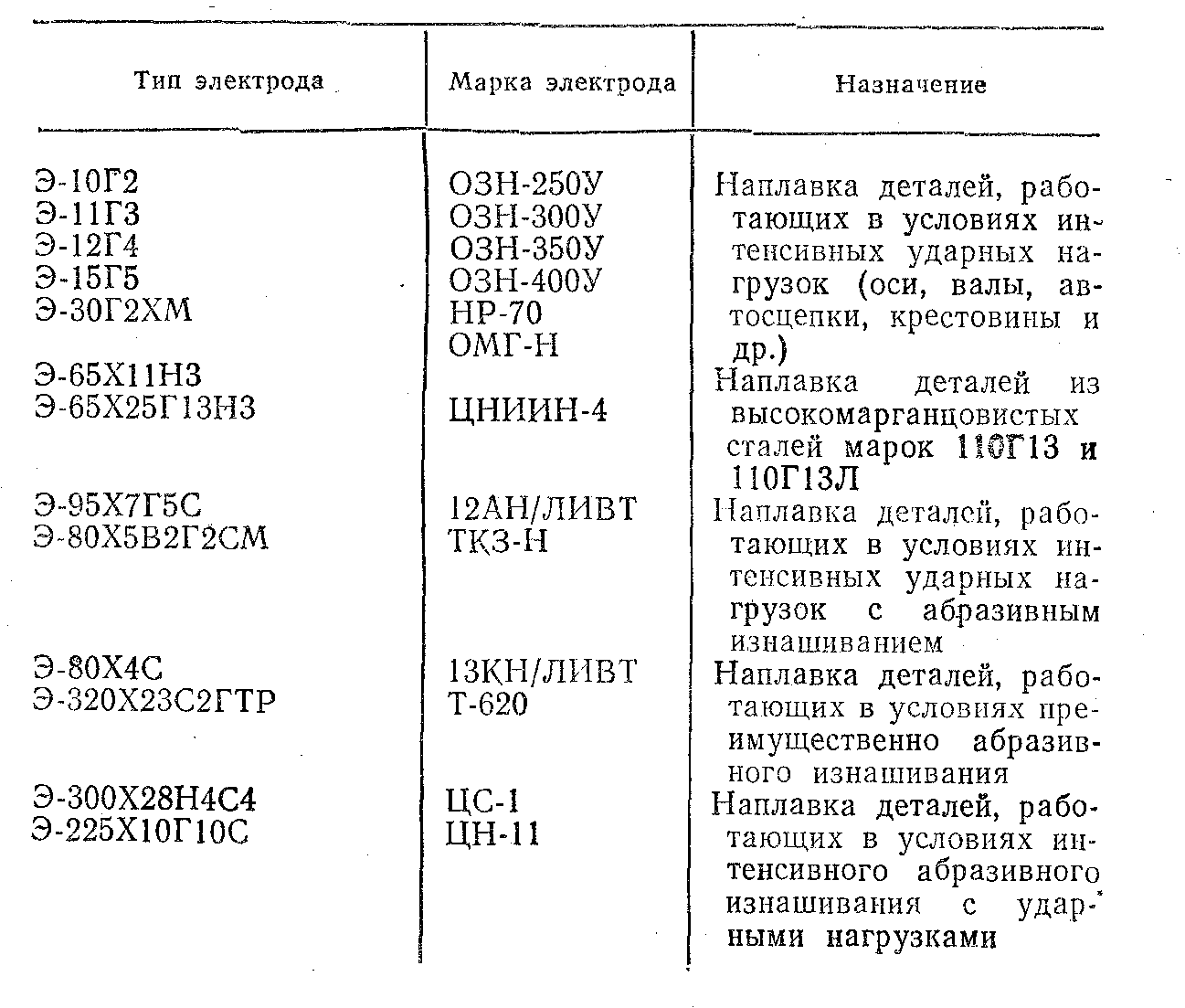
ЭМ4, АМ4, чугунные прутки для низкотемпературной сварки-пайки марок Н4-1, Н4-2 и некоторые другие.
Для сварки меди и медноникелевых сплавов и в ремонтных целях используют электроды марок «Комсомолец», ЭТ. В состав покрытий указанных марок входят различные раскислители и шлакообразующие компоненты. В качестве электродных стержней для электродов ЭТ используют проволоку из меди М1, проволоку из кремнемарганцевой бронзы Бр.КМцЗ-1, литые стержни из латуни Л90 или оловянисто-фосфористой бронзы Бр.ОФ-4-О,25; для электродов «Комсомолец-100» — медную проволоку М1
Бронзы сваривают электродами со стержиями из бронзовых прутков и покрытиями, содержащими мрамор, плавиковый шпат и различные раскислители или покрытиями, состоящими из криолита, хлористого калия, хлористого натрия и древесного угля.
6.Атоматическая и полуавтоматическая электродуговая сварка и наплавка
Наибольшее применение имеет автоматическая и полуавтоматическая сварка плавящимся электродом, под слоем флюса или в среде защитных газов, которая дает более стабильный шов с повышением производительности в 2...8 раз по сравнению с ручной дуговой сваркой.
Основное промышленное применение находит сварка под флюсом одной вертикально расположенной электродной проволокой сплошного сечения (рис. 4.13). Нагрев и плавление основного и присадочного металлов происходят за счет тепла, получаемого при преобразовании подводимой к дуге электрической энергии. дуга 1 возникает между электродной проволокой 2 и основным металлом 3, подсоединенным к полюсам источника питания. В качестве такого источника используют специальные однофазные или трехфазные сварочные транс-
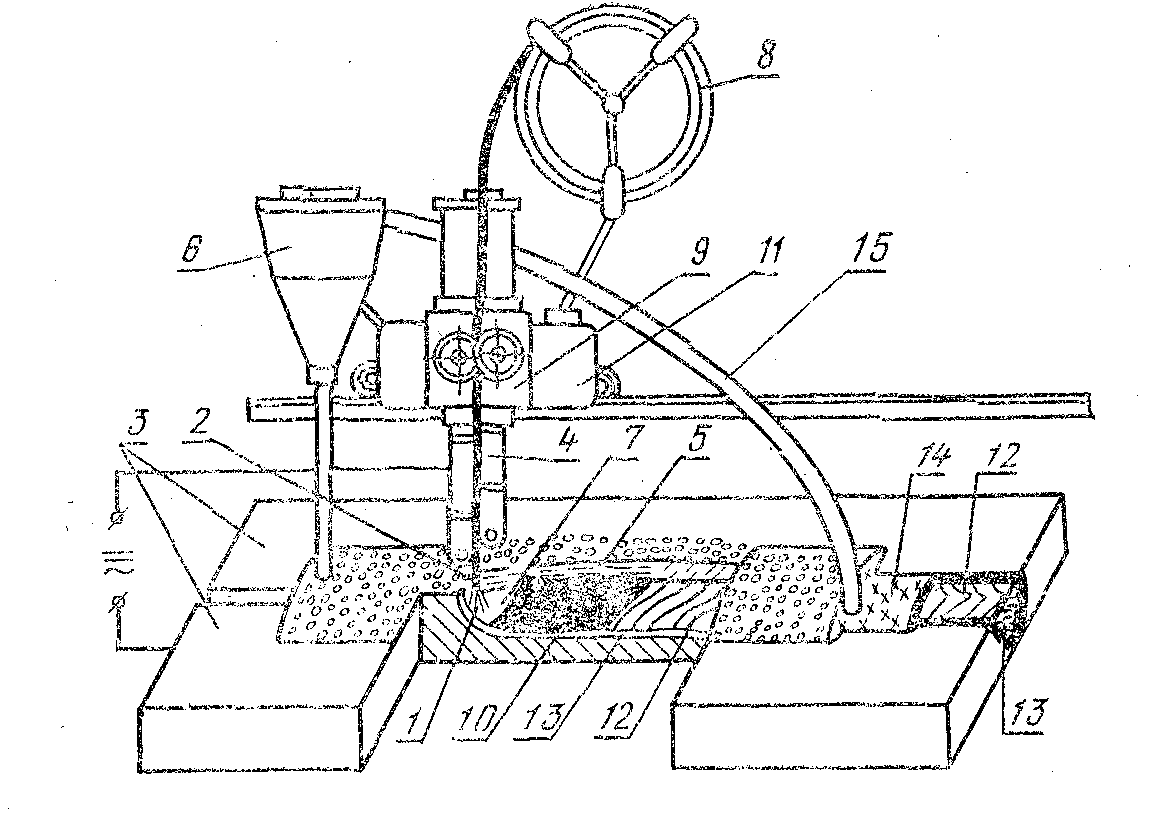
Рис. 4.13. Схема автоматической сварки под слоем флюса:
1 — электрическая дуга; 2 — электродная проволока; 3 — основной металл; 4— мундштук; 5 — слой флюса; 6 - флюсоаппарат; 7 — прослойка жидкого шлака; 8 — бухта электродной проволоки; 9— сварочная головка; 10—сварочная ванна; 11 — тележка для перемещения Сварочной головки; 12 — Сварной шов; 13 — зона термического влияния; 14 — шлаковая корка; 15 — шланг для возврата флюса в флюсоаппарат.
форматоры переменного тока с пологопадающей внешней характеристикой, генераторы и выпрямители с пологопадающей или падающей внешней характеристикой. Сварку на постоянном токе преимущественно ведут при обратной полярности. Возможна сварка и при прямой полярности.
Подвод тока к электродной проволоке и ориентацию ее конца по отношению к свариваемым кромкам осуществляют мундштуком 4. Ток к изделию подводят через неподвижные или подвижные контактные устройства (струбцины, щетки и др.). Режим существования дуги при сварке под слоем флюса определяется силой тока, напряжением и длиной дуги. Обычно применяют силу тока 1000...1200 А, что при открытой дуге невозможно вследствие разбрызгивания металла юна. Сварку ведут короткой дугой. Некоторые современные автоматы поддерживают отклонение длины дуги в пределах 0,2... 0,3 мм. Напряжение колеблется в пределах 18...55 В.
В процессе сварки электрод и основной металл со всех сторон окружены слоем флюса 5, насыпаемым из флюсоаппарата 6, работающего обычно от заводской сети сжатого воздуха (при массовом производстве). Высоту и ширину слоя устанавливают, исходя из условия обеспечения эффективной изоляции зоны сварки от окружающего воздуха и создания плотного формирующего жидкий металл барьера. Обычная высота слоя флюса 20...б0 мм. При нагреве и плавлении флюс выделяет газы и пары, способствующие стабилизации дугового разряда.
Дуга находится в заполненном парами и газами пузыре, сводом которого является прослойка 7 из жидкого шлака. Таким образом, флюс при этом способе сварки защищает расплавленный металл электрода и ванны от воздуха; концентрирует тепло в зоне сварки; замедляет остывание ванны, позволяя попавшим в нее газам выйти наружу; облегчает ионизацию дугового промежутка, обеспечивая стабильность процесса; легирует металл шва дополнительными элементами; предотвращает выгорание полезных примесей.
для автоматической сварки применяют плавленые и керамические наплавленные флюсы. Керамические наплавленные флюсы представляют собой крупинки (гранулы) размером 1...3 мм, изготовленные из материалов, входящих в состав обычных покрытий электродов для электродуговой ручной сварки. По характеру шлака различают кислые и основные флюсы, а по назначению — для сварки низкоуглеродистых сталей, легированных спецсталей, цветных металлов для наплавочных работ и т. д.
Довольно широко применяют флюсы марок АН348А, ОСЦ-45, АН-15, АВ-5, 48-ОФ-10, в которых основой служат окислы марганца и кремния. Дополнительно в флюс добавляют компоненты для повышения жидкотекучести шлаков (СаЕ2), стабилизации горения дуги (СаО, МО) и легирования металла шва (феррохром, ферротитан и др.).
В качестве электрода для сварки малоуглеродистой и низколегированной стали используют сварочную проволоку марок Св.08, Св.08А, Св.О8ГА, Св.18ХМА, Св.1ОХ16Н25М6 диаметром 1,6; 2; 3 и 4 мм.
При сварке под слоем флюса используют источники питания переменного и постоянного тока с падающей характеристикой: трансформаторы ТДФ-1001, ТДФ-1601, ТШС-.1 000-3; преобразователи ПСО-300, ПСО-500, ПСГ-500 в выпрямители ВДУ- 1001, ВДУ-504, ВДУ- 1601 и др.
Для автоматической сварки и наплавки промышленность выпускает аппараты марок АБСК, А1401, А1423, АЗ84МК, А580М, трактора ТС- 17М- 1, АДС- 1004-04, АДФ-1001, ТС-44, ДТС-38 и др.
Полуавтоматическая сварка отличается от автоматической тем, что применяют более тонкую электродную проволоку и сварщик перемещает полуавтомат вдоль выполняемого юна вручную. Промышленность выпускает полуавтоматы общего применения АК6Б, А1197С и специализированные А1114М, А 1530.
При ремонте сельскохозяйственной техники широко используют наплавку под слоем флюса для восстановления геометрических размеров изношенных деталей (рис. 4.14)
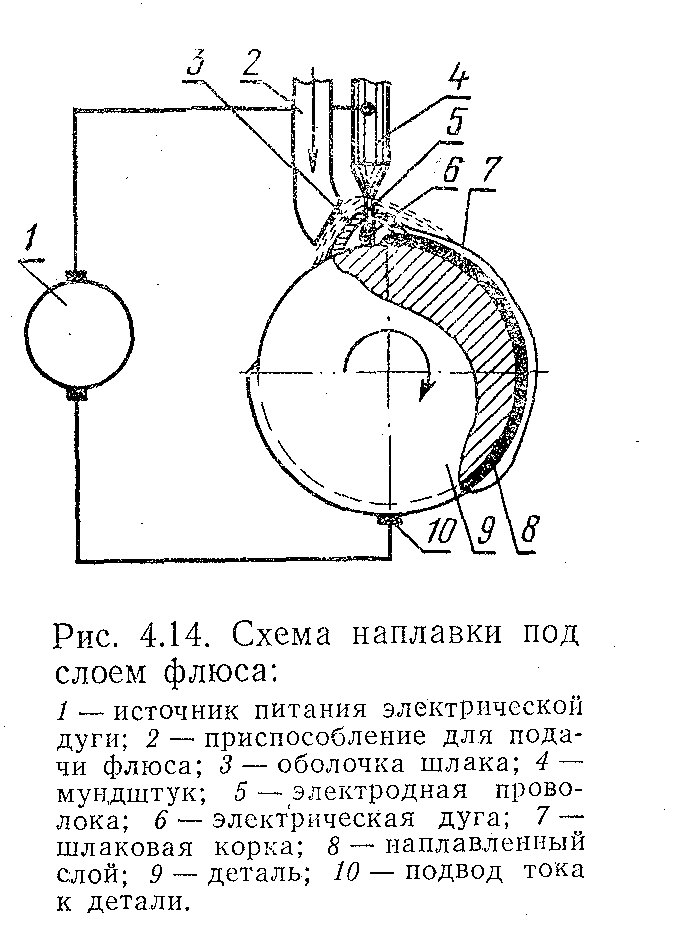
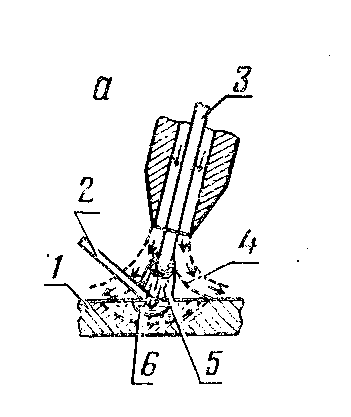
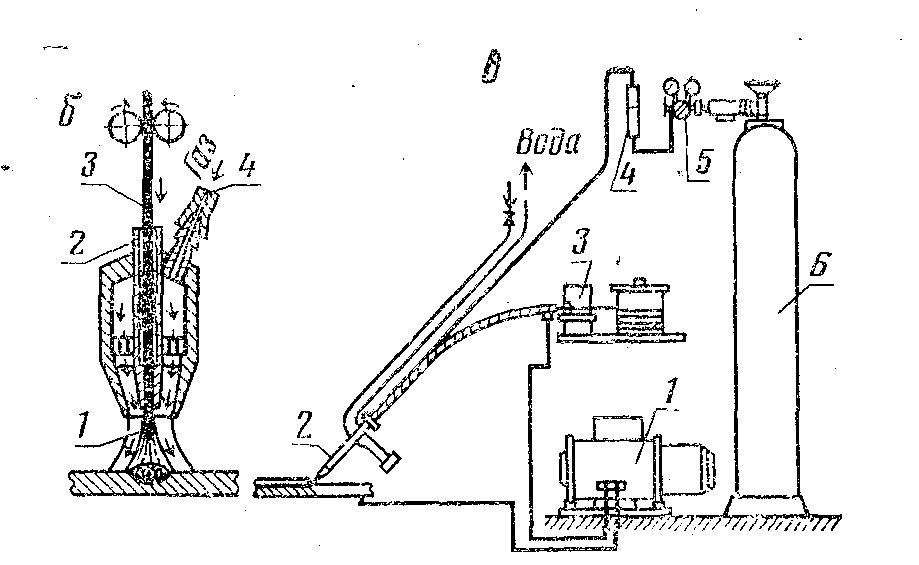
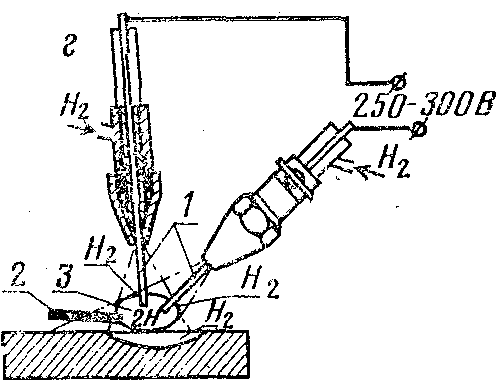
Рис. 4.15. Схема сварки в среде защитных газов:
а — аргонодуговая сварка неплавящимся электродом; 1 — свариваемое изделие; 2 — присадочный пруток; 3 —электрод; 4 — газ аргон; 5 — электрическая луга; 6 — ванна жидкого металла;
б — аргонно-дуговая сварка плавящимся электродом: 1 — электрическая дуга; 2 — наконечник горелки; 3 — электродная проволока; 4 — канал для подвода аргона;
в — сварка в атмосфере углекислого газа: 1 — источник питания электрической дуги; 2 — газоэлектрическая горелка; 3 — механизм подачи электродной проволоки; 4— ротаметр; 5— редуктор; 6— баллон с углекислым газом;
г — атомно-водородная сварка: 1 — вольфрамовые или угольные электроды; 2 — присадочный металл; 3—зона сварки.
Для защиты металла от воздействия воздуха, кроме шлакового покрытия, применяют газовую защиту вокруг дуги и расплавленного металла. В качестве защитных применяют инертные (аргон, гелий) и активные газы (водород, окись углерода или их смесь с азотом). Наибольшее распространение получили аргонно-дуговая сварка и сварка в среде углекислого газа.
При аргонно-Дуговой сварке неплавящимся электродом (рис. 4.15,а) через специальную горелку, в которой установлен вольфрамовый электрод 3, пропускают инертный газ (аргон или гелий). Возбуждение дуги происходят между электродом и свариваемым изделием, Для заполнения разделки кромок в зону вводят присадочный материал 2, химический состав которого близок к составу свариваемого материала. Применяют электроды диаметром 2...6 мм. Аргон подают в горелку под давлением 0,03...0,05 МПа.
Аргонно-дуговую сварку применяют для сварки легированных сталей, алюминия и его сплавов, титана, магниевых сплавов.
В ряде случаев сварку выполняют и плавящимся электродом. В этом случае применяют проволоку диаметром 0,6...3 мм, которую автоматически подают в наконечник 2 горелки (рис. 4.15,б). Защитный газ через специальный канал 4 наконечника горелки попадает в пламя дуги 1.
Атомно-водородная сварка — разновидность сварки в среде защитных газов (рис. 4.15,г). Особенность процесса заключается в том, что молекулярный водород под влиянием высокой температуры дуги в промежутке между электродами превращается в атомарный. В нижней части дуги при соприкосновении газа с холодным свариваемым металлом атомарный водород превращается в молекулярный. При этом выделяется значительное количество тепла. Сварочная дуга возбуждается между двумя электродами 1 (вольфрамовые или угольные).
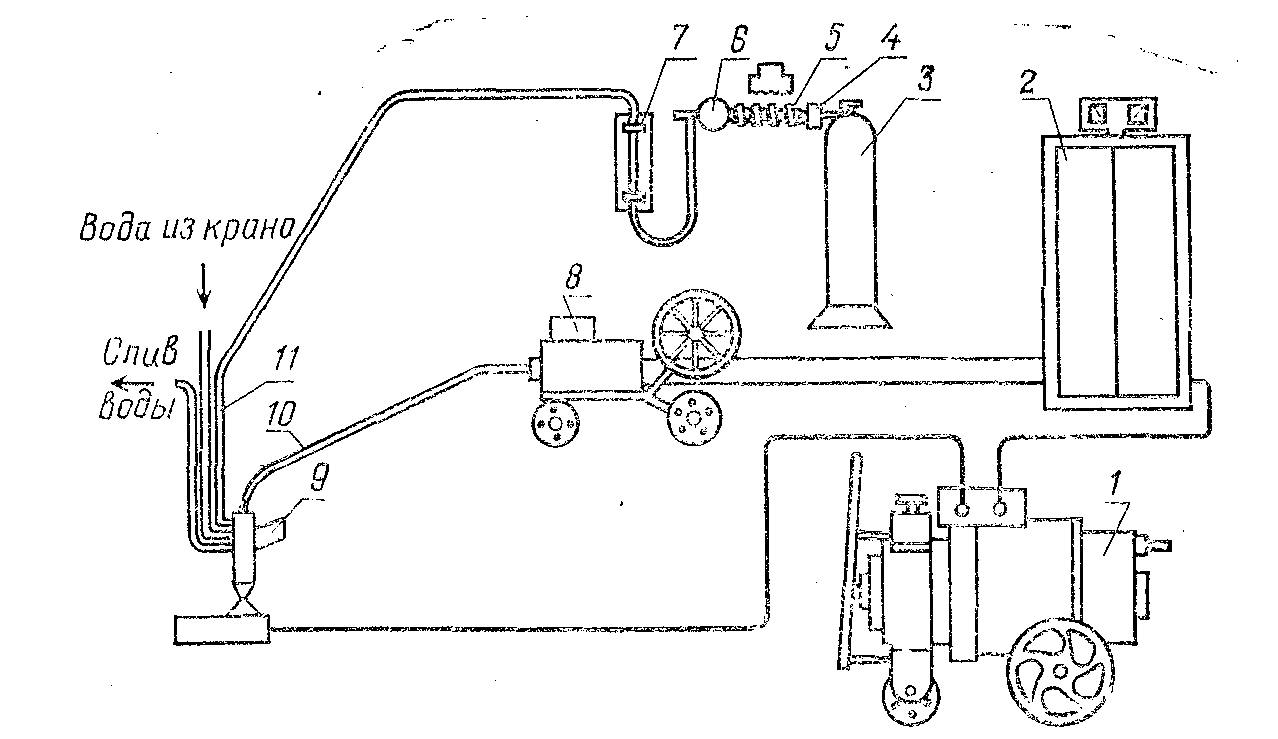
Рис. 4.16. Схема установки для наплавки в среде углекислого газа:
1 — сварочный генератор; 2 — аппаратный ящик; 3— баллон с углекислым газом; 4 — осушитель газа; 5— подогреватель газа; 6 — редуктор; 7— ротаметр; 8 — механизм подачи сварочной проволоки; 9 — газоэлектрическая горелка; 10—шланг для подвода электродной проволоки и тока; 11—шланг для подачи газа.
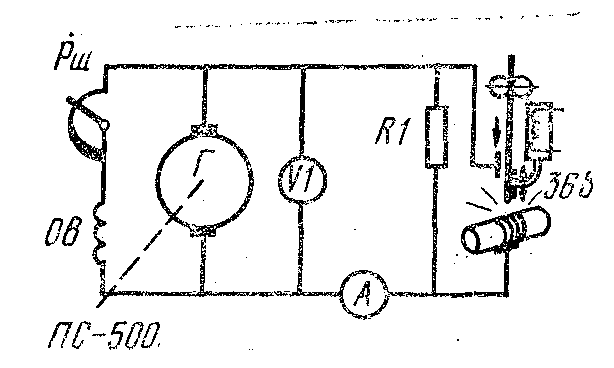
Рис. 4.17. Принципиальная электрическая схема вибродуговой установки.
Напряжение источника тока составляет 250...350 В, рабочее напряжение — 30... 120 В; сварочный ток—
10...70 А. Присадочный металл 2 вводят в зону сварки 3 обычным способом.
Сварка в углекислом газе наиболее дешевый способ по сравнению с другими видами сварки в защитных средах — широко применяется при восстановлении деталей сельскохозяйственных машин, особенно чугунных (рис. 4.15, в). Процесс наплавки в среде углекислого газа по существу аналогичен процессу сварки (рис. 4.16)
Для наплавки в среде углекислого газа используют электродные проволоки с повышенным содержанием кремния, марганца и титана (Св.08ГС, Св.08Г2С, Св.10ХГ2С и др.). Для образования износостойкого наплавленного слоя применяют порошковые проволоки (ПП-6ХЗВ10, ПП-сормайт-1, ПП-сормайт-2, ПП-10Х10В4 и др.).
Наплавку тел вращения производят, используя токарно-винторезный станок.
Для восстановления изношенных деталей в ремонтной практике нередко применяют вибродуговую наплавку, в основе которой — контактная сварка и электрическая дуга. Наплавку можно вести на воздухе, в среде защитного газа, в жидкости. Процесс состоит из трех этапов: замыкание электрода с деталью, размыкание, холостой ход. В момент короткого замыкания конец электрода оплавляется. При отрыве электрода перемычка взрывообразно разрушается и процесс переходит в дуговой. В этот момент и происходит перенос металла электрода на наплавляемую деталь. Наплавку чаще ведут на постоянном токе, что обеспечивает лучшую стабильность процесса.
Установки для автоматической вибродуговой наплавки обычно монтируют на базе токарно-винторезных станков, на суппорте которых устанавливают вибродуговую головку ЭВГ-2, КУМА-5М, ОКС-1252 и др. (рис. 4.17).